Passive Fire Protection (PFP)
Published in September 2020 by the Competence Steering Group, Setting the Bar (the final report of the Competence Steering Group), represents two years of challenging work following the Grenfell Fire Tragedy. Initiated by the recommendations within Dame Judith Hackitt's review “Building a safer Future” it identifies the need for competent persons within the construction and built environment industries to ensure buildings are effectively designed, maintained and managed with (fire)...
Once users have conducted a competent fire risk assessment, where necessary, users may then need to plan for what’s known as fire compartmentation, or passive fire protection survey. It’s important to understand that Passive Fire Precautions (PFP) are a vital part of the building fabric, dividing the building into individual fire compartments, constructed, and lined with suitable fire resisting materials to reduce the spread of fire. Individual fire compartments What is the purpos...
As a pioneer manufacturer of high-performance sealing systems for fire doors – they have shown unwavering support for Fire Door Safety Week since its inception in 2013. Kicking off on marks a momentous 10 year anniversary of the campaign. Fire Door Safety Week (FDSW) was launched in response to a legacy of fire door neglect. Know Fire Door Basics The campaign is managed by the British Woodworking Federation and is supported by a number of partners It's a ‘mass market’ aware...
Ranger Fire and Security has announced its first acquisition of 2025, with McGoff & Vickers Fire & Security Systems (MGV) becoming the latest business to join the rapidly growing Ranger Group. Run by industry specialists and service business experts, Ranger brings together high-quality fire and security (F&S) businesses in partnership to share industry expertise, resources and boost cross-selling opportunities. Fire protection services North-West-based F&S business MGV has a h...
Here at FireRite, they believe in providing full training for apprentices in the industry. That involves close mentoring and monitoring the personal development of all their apprentices. They are an award-winning outfit that believes in nurturing young talent. Right now, they have positions available for which they are happy to provide apprenticeships – Fire alarm engineers, Fire Stopping Technicians and Fire Door Fitter Technicians. Fire Alarm Engineer The Fire Alarm Engineer apprentic...
In celebration of 100 years of the IFE and continuing to build on previous event successes, the South Wales IFE Branch organized a CPD event on 19th July 2018 at South Wales Fire and Rescue Service Headquarters. The event, which focused on Fire Compartmentation, attracted over 100 delegates and was supported by Firerite UK, a Fire Protection Company based in South Wales. The presentations were developed to focus on key elements of Compartmentation. How firestop products are tested Fire-Rite U...
News
Firerite is proud to support this year’s Fire Door Safety Week (24th September – 30th September) – a campaign that raises awareness about the critical role of fire doors, drawing attention to specific issues such as poor installation and maintenance. It also encourages building owners and users to check the operation and condition of their fire doors; and understand the legal commitments they have. Fire doors are a crucial part of the passive fire protection of every commercial, public and multiple occupancy building. They save lives and property. New fire doors in the UK There are about three million new fire doors bought and installed every year in the UK, the vast majority made from timber. Fire doors are often the first line of defence in a fire and their correct specification, maintenance and management can be the difference between life and death for building occupants. However, they remain a significant area of neglect, often the first thing to be downgraded on a specification and mismanaged throughout their service life, propped open, damaged and badly maintained.
Allegion UK, alongside its family of pioneering door hardware brands, is set to present a complete fire door solution at The Fire Safety Event, taking place between the 8th and 10th April at the NEC, Birmingham. With a focus on keeping people safe where they live, learn, work and connect, Allegion’s team of experts will be on hand with specification, installation and maintenance advice at this year’s event, and will showcase a flagship range of fire door solutions, including architectural hardware, fire and smoke seals, vision panels and an intumescent fire block louver system. Set of tested and certified products Allegion is inviting visitors to stand 4/K106 where they can experience three full-sized door models To demonstrate the crucial role that fire door hardware plays in fire safety, Allegion is inviting visitors to stand 4/K106 where they can experience three full-sized door models, each displaying a harmonized set of tested and certified products suitable for timber and steel fire doors. Throughout the three-day event, Allegion will also exhibit a working model of its unique XB120 automatic door operator from Boss Door Controls. Available in a choice of seven high-quality finishes, ranging from ‘Light Bronze’ to ‘Matt Black’, all finish options are designed to enhance all architectural styles. Key element of passive fire protection Speaking on their plans for the event, Pete Hancox, country manager at Allegion UK, commented: “Fire doors are a key element of passive fire protection, and in the event of a fire, it’s crucial that essential door hardware has been expertly specified, correctly installed and properly maintained." "As part of our ongoing campaign to raise awareness and reduce knowledge gaps in these areas, we’re delighted to return to The Fire Safety Event, as it provides the perfect platform to offer valuable expertise and support to a key audience." Highest standards in fire safety management Hancox added: “We will be showcasing the Allegion family of brands at this year’s event and plan to offer visitors true peace of mind by presenting a complete fire door solution that combines a range of our certified, highly-engineered and third-party tested fire door safety products. Our team of experts will also share real-time installation advice, with live demonstrations of our unique self-adhesive Accufit system, which has been enhanced to facilitate easy and accurate installation of our Briton door closers.” The Fire Safety Event supports industry practitioners, professionals and organizations in achieving and maintaining the highest standards in fire safety management, and provides visitors with the perfect opportunity to observe the latest products, technology and solutions in fire safety.
Allegion UK, a pioneer in fire safety hardware and manufacturer of ‘Briton’ door controls, has expanded its library of customer support materials with new installation videos for its highly popular 2003 and 2003V surface-mounted door closers. Aim to publish a video Allegion’s newly published video series provides customers with an illustrative set of installation and adjustment instructions for door mount pull, transom mount, and parallel arm mount fixings across its major product lines. With each video, Allegion aims to improve the accuracy of door closer fittings by delivering a comprehensive walkthrough of the 2003 and 2003V installation process, from the product unboxing to its fixing methods and measurements, as illustrated by Briton’s unique self-adhesive Accufit template system. Step-by-step installation guidance Allegion will shortly complete a suite of digitally curated support materials, which includes technical datasheets With plans to further develop the video library to include step-by-step installation guidance for the Briton 2130B overhead closer, Allegion will shortly complete a suite of digitally curated support materials, which includes technical datasheets, product certifications, fixing templates, and downloadable service and maintenance instructions. Speaking on the ambitions behind the new installation videos, John Fairhurst, business development manager at Allegion UK, commented, “Where the safety of buildings and their occupants is reliant on fire door hardware, we too often identify inaccurate installation as a leading cause for inadequate product performance." Fire door safety standards "To prioritize fire safety, we believe it’s crucial to eliminate the issues associated with incorrect hardware installation, and by adding short and engaging video content to our resources, we can further support our customers in this area." “Driven by our ongoing commitment to improving fire door safety standards, and following the success of our updated Accufit system for the 2003 and 2003V, we have also developed a new Accufit template for the Briton 2130B, which is available now and will feature in a standalone series of installation videos set to launch later this year.”
Magenta Security Services has once more demonstrated its leadership in sustainability, securing the coveted "Security or Fire Sustainability Champion" award at the prestigious Security and Fire Excellence Awards 2024 for the second consecutive year. The awards ceremony, a hallmark of excellence in the security and fire sectors, celebrates organizations that set benchmarks in innovation, performance, and commitment to sustainability. Magenta Security’s pioneering sustainability initiatives and steadfast dedication to eco-friendly practices earned them this outstanding recognition. Solar-powered charging stations "Winning this award for the second-year running is an incredible achievement," said Abbey Petkar, Managing Director of Magenta Security Services. Abbey Petkar adds, "It underscores our unwavering commitment to sustainability and reflects the transformative steps we have taken to reduce our environmental impact, while inspiring our industry peers to adopt greener practices. This honor strengthens our resolve to lead by example and continue setting new sustainability standards." Magenta’s groundbreaking achievements include: Achieving carbon zero status in 2022, years ahead of schedule. Fully transitioning its vehicle fleet to electric and installing solar-powered charging stations. Significant investments in energy-efficient infrastructure, reducing energy consumption by 75%. Championing a paperless workplace, saving over 150 trees annually. Engaging in industry forums, contributing to global sustainability conversations, and initiatives like the Carbon Database Initiative (CaDI) for transparency in emissions reporting. Comprehensive sustainability strategy The judging panel applauded Magenta Security’s comprehensive sustainability strategy, which goes beyond operations to influence supply chains, engage communities, and foster collaboration within the industry. "Sustainability is more than a corporate responsibility for us; it is integral to who we are and how we operate," said Abbey Petkar, adding "We are not just protecting today’s world, but actively shaping a sustainable future." This accolade reinforces Magenta Security’s role as a pioneer in both security services and sustainability, setting an inspiring example of environmental stewardship.
For many different stakeholders in building design, construction, and management, security specifications can be a difficult, time-consuming task. Everyone from architects, developers, and contractors to security consultants, distributors, and even building inspectors benefits from trustworthy, transparent specification support for doors and related solutions. Digitalization and personalized service When the goals are better buildings, safer building users, and happier customers, the answer lies in a combination of digitalization and personalized service. A unified digital thread eliminates any confusion that can follow when stakeholders juggle multiple versions of documents. Personalized specification support ensures stakeholders select the right door solutions, project costs accurately, and minimize costly errors along the way. From design to handover, everyone works smarter. Software tools and specification support ASSA ABLOY specification experts can ensure fire safety and barrier-free accessibility are factored in From doors and door closers to wireless digital locking devices and complete digital access ecosystems, ASSA ABLOY has solutions for almost any building or opening. This vast range and breadth of project experience create uniquely broad-based knowledge, including about the latest innovations in low-impact mobile access and other energy-saving digital solutions. ASSA ABLOY specification experts can ensure fire safety and barrier-free accessibility are factored into early versions of a design, for example. This helps building owners and investors to meet compliance and safety requirements directly from project initiation, saving time and stress. Openings Studio™ ASSA ABLOY software tools such as Openings Studio™ help security security specialists and distributors specify accurately and manage stock efficiently. When a digital thread is maintained through building management, fire and safety inspectors complete their tasks time- and cost-efficiently. Openings Studio brings projects together in one intuitive environment by creating a transparent digital platform where everyone contributes. For this reason, it is already deployed all over the world as a trusted design, specification, compliance, and ordering tool – for building projects of every size and type. Benefits Deployed alongside personalized support from locally based ASSA ABLOY specification teams, it offers material benefits to every stakeholder. Stakeholder #1: Architects Openings Studio streamlines this without eating into the time architects need to focus on design To realize their vision for the final building, architects need everyone on the same page. Efficient collaboration and effective management of communication help them stay in control of project quality and timelines. Openings Studio streamlines this without eating into the time architects need to focus on design. Saves time “Openings Studio software introduced us to a whole new way of thinking and efficiency,” says David Zarhy, whose firm Zarhy Architects used Openings Studio for the Broadcom R&D Center at Tel Aviv University. The project transparency and knowledge-sharing that ASSA ABLOY brings to security specification is also invaluable, saving time and preventing mistakes. With detailed specifications supplied digitally at an early stage, architects visualize door and security solutions accurately as soon as possible. This way, aesthetics, and usability are not disrupted by last-minute hardware surprises. Stakeholder #2: Building Developers & Owners Investors want to maximize and future-proof the ROI from their property portfolio. At the same time, they have a responsibility to ensure compliance on measures including barrier-free building access and fire safety. Personalised specification support helps them to weigh options, meet their legal obligations, and control ongoing property management costs. To also meet the booming demand for green building accreditations, ASSA ABLOY offers in-depth support for developers seeking accreditation in six green building programs: BREEAM, LEED, Green Star, WELL, DGNB, and HQE. Sustainability credentials Another welcome benefit for ownership, returns on investing in greener buildings can boost more than just the environment. According to property experts JLL, “Buildings with better sustainability credentials are achieving markedly higher capital values and rents.” They estimated improvements of 20.6% and 11.6%, respectively, in one analysis of BREEAM-certified premises for the UK office sector. Stakeholder #3: Building Contractors Working smarter with software and specification support ensures customers come back In the construction phase, more than any other, time is money. Hitting every deadline and budget directly impacts the bottom line. Working smarter with software and specification support ensures customers come back in the future, supporting a sustainable, profitable business. The path from design to build is smoother when hardware data and deliveries are accurate, so all project changes must be communicated quickly along the stakeholder chain. Authoritative specification data Openings Studio ensures builders waste less time coordinating clients and suppliers – which means less disruption to their day-to-day work. Site workers access authoritative specification data for every opening quickly via intelligent tags and QR codes embedded within Openings Studio, for example, which saves time and prevents mistakes. Stakeholder #4: Security Hardware Specialists & Consultants The best way to keep customers coming back is by delivering great service. For hardware specialists, this means specifying technical jobs quickly and accurately. Tools and support that help automate tedious manual tasks and enable slicker collaboration to provide an awesome efficiency boost. ASSA ABLOY delivers support through a network of local BIM and specification teams, each with specific knowledge about applicable standards and regulations. Reusable and recyclable materials They supply products that are manufactured to eco-design principles and help reduce ongoing energy use. Detailed, product-specific EPDs highlight the concrete benefits delivered by ASSA ABLOY’s investments in using more reusable and recyclable materials, and in embedding low-energy and eco-design principles across its operations, detailed information that will be essential when the European Performance of Buildings Directive is implemented in 2026. Stakeholder #5: Distributors Effective coordination and accurate quotes are made easier and faster with the help of Openings Studio Satisfying customers means shipping the right products, on budget and time, every time. To achieve this, staying on top of current pricing and specifications is critical, even when these are in flux because a project is evolving. Effective coordination and accurate quotes are made easier and faster with the help of Openings Studio software. Intuitive tool Part of a longstanding collaboration with SWEDOOR in Denmark, a large project for Østre Landsret, the High Court for Denmark’s Eastern region, was streamlined with the help of Openings Studio. This intuitive tool underpinned door meetings, ensuring efficient decision-making and component delivery for every closer, lock, and cylinder. Safe and secure In Denmark and elsewhere, Openings Studio has become the focal point of collaboration between ASSA ABLOY, SWEDOOR, locksmiths, building contractors, and architects. According to Per Løvstad, Sales Manager at SWEDOOR JW Denmark, “Cooperation consists of a total review of the entire door project, door by door so that our mutual customer feels safe and secure that the doors and the entire package fit together. I can only recommend this collaboration to anyone who has to go through larger projects with doors and fittings.” Stakeholder #6: Building Inspectors Entrusted with making sure buildings are safe for users, inspectors need transparency in fire, safety, and accessibility compliance. In the past, this meant manual updates and endless spreadsheets – carried everywhere, even out of the office. “With Openings Studio, you no longer need to rely on paper or spreadsheets to manage doorset data,” explains Marc Ameryckx at ASSA ABLOY Opening Solutions EMEIA. “It’s all digitally managed in one place over the life of the building, which saves everyone’s time.” Openings Studio helps to maximize the effectiveness of inspections by safeguarding a reliable, up-to-date source of specification info and making it available on demand – even on an inspector’s mobile phone. Fire inspections The mobile app equips inspectors with powerful, speedy, and transparent reporting tools Doorview, who conduct fire inspections in the London area, uses Openings Studio to speed up their work. “The Openings Studio app allows us to instantly share fire door inspection reports with our clients,” explains Doorview’s Jody Purcell. The mobile app equips inspectors with powerful, speedy, and transparent reporting tools by leveraging the same information from the design phase through to the maintenance of the completed structure. Remedial action list The app also helps Doorview implement a remedial action list, which reassures the client that their building is compliant and safe. Maintenance staff can upload a photo when any required refits are complete. Working digitally with Openings Studio assures the transparency of this process. “Because specification and BIM teams are based at locations spanning ASSA ABLOY’s global network, they bring experience and expertise on local issues, standards, and certifications,” adds Marc. Digital collaboration “With digital collaboration in Openings Studio – plus dedicated specification support from a global team of local experts – ASSA ABLOY can help you transform the way you work." "You will deliver faster, better projects, hitting budget targets and meeting the needs of building managers and users, now and far into the future.”
Ranger Fire and Security has announced the latest acquisition of Motherwell and Newcastle-based fire, security, and critical services company, Secureshield. one-stop solution The acquisition marks another milestone in Ranger’s continued growth and expansion, with Secureshield building out the Group’s footprint in Scotland and North-Eastern England. With plans for further imminent regional acquisitions in the pipeline, this announcement reiterates Ranger’s mission to become the one-stop solution for fire and security services in the UK and Ireland. fire and security maintenance Secureshields’ team of over 70 employees enables them to commission and deliver maintenance services Secureshield offers national coverage for maintenance and related works in fire and security disciplines. Widely recognized for their high-quality service in the fire, security, and critical services industry, Secureshields’ team of over 70 employees enables them to commission and deliver maintenance services across the UK. Secureshield Secureshield is an independent provider of emergency lighting, CCTV, access control, and Technology Enabled Care Services (TECS), such as social alarms and call systems with a diverse range of SME and larger corporate clients across both public and private sectors, such as the MoD and NHS. The company is led by Managing Director John Hunter, who will also be appointed as Ranger’s Regional Chair in addition to his current role. Alongside Ian Teader (Ranger Group Managing Director), John will lead Ranger’s organic and inorganic expansion in Scotland and the North-East. cross-selling opportunities Secureshield is poised for continued growth within the Ranger Group, expanding the company’s resources The Secureshield management team will be instrumental as Ranger looks to expand through acquisitions and partnerships. Following Ranger’s strategy and criteria to find the right team to back, Billy Hunter (Sales), Lorna Forsyth (Finance), and Rory Walker (Operations) will all stay onboard and will be key to enabling future growth. With this strong leadership, backed by a robust customer and client base, solid maintenance portfolio, and experienced management team, Secureshield is poised for continued growth within the Ranger Group, expanding the company’s resources, and opening up further cross-selling opportunities for all Ranger businesses. fire and security solution Mark Bridges, CEO of Ranger Fire and Security, said, “Secureshield is a highly respected key player in the fire, security, and maintenance space. Their joining of the Ranger Group will expand our geographic reach and industry expertise." “With a strong management team led by John, Billy, Lorna, and Rory, this acquisition provides us with a fantastic opportunity to drive further growth and cross-selling opportunities – helping Ranger to deliver our mission of a high-quality one-stop fire and security solution across the UK and Ireland." customer service John Hunter, Managing Director of Secureshield said, “There was a huge amount of interest in Secureshield, but with a shared focus on growth and delivering the highest quality service for our customers and clients, Ranger was absolutely the right partner for Secureshield’s future." "We looked at several options to take Secureshield to the next level but felt that Ranger was best equipped with their experience and partnership-led approach to deliver on our goals." development and expansion hub Ranger enhances its offering in all key areas of fire and security services, such as fire detection and alarms “I am looking forward to working closely with Mark and the Ranger team to grow Secureshields’ presence, enhancing our existing portfolio, fostering greater collaboration across the group, and by the prospect of us serving as the hub for development and expansion.” The announcement builds on Ranger Fire and Security’s previous acquisitions of AFIL, Ignis Fire Protection Ltd, Syncro Group Ltd, IPH Fire Solutions Ltd, Fire Door Specialists Ltd, and KSS Fire Suppression, which together have helped Ranger to enhance its offering in all key areas of fire and security services, such as fire detection and alarms, extinguisher maintenance, passive fire, and security services. seamless customer experience Since launching earlier in 2024, with backing from the private investment firm Hyperion Equity Partners, Ranger has embarked on a mission to establish itself as the leading one-stop solution provider in the fire and safety sector. It offers a comprehensive range of services through both regional and national operations and provides a seamless customer experience. ThinCats provided funding for the acquisition.


Expert Commentary
The 2022 Building Safety Act, instituted in direct response to the Grenfell Tower tragedy in London, UK, has outlined a raft of new responsibilities that building owners and managers must adhere to, in line with many of the deficiencies identified post-2017. With the UK’s building stock notoriously aging, many of us live and work in buildings that were built under outdated regulations and have not been updated for decades in some cases. As such there is an enormous amount of remedial safety work to be done that covers essential fire protection features such as fire doors, alarms, sprinklers, and cladding materials. High-rise buildings Despite £5bn being allocated by the government to replace dangerous cladding, progress is slow, and it has been estimated that the amount needed to fully address the issue is closer to £50bn. In London, more than £1bn has been spent, and 700 buildings over 18m in height have applied for government support. However, almost half of those buildings currently in that process have not seen any remedial work begin. This means in the capital alone there are more than a thousand high-rise buildings that are currently in need of urgent work. The need for retrofitting is particularly notable in high-rise buildings where fire spread can be rapid, and evacuation can be challenging. Across the country, there are over 11,000 high-risk buildings over 18 meters tall. In total, there could be two decades worth of remediation work. Building regulations Perfectly illustrates the delays people are facing when making their home or place of work safe from fire We had a stark, while thankfully non-tragic, reminder in August, that showed the danger of leaving these buildings in their current state when an apartment block in Dagenham caught fire. In this particular case, an external wall survey, commissioned four years before the fire, found that the block did not fully meet building regulations at the time of construction. Despite permission being granted in May 2023 and work being scheduled for June 2023, it was still ongoing almost 9 months after the target end date of December 2023. This perfectly illustrates the delays people are facing when making their home or place of work safe from fire. Traditional fire stopping The option that is often left to building owners is to completely remove the façade and install traditional fire stopping and, in many cases, requires residents to be relocated, requires large amounts of time, is severely disruptive, and carries a large price tag. This is why I have been vocal in my support of remedial work that doesn’t carry the enormous burden and cost of completely removing a facade to complete the work. By inserting a protective sock filled with an acrylic-based fire-resistant sealant, the fire can be contained within a small section of the cavity for longer, significantly reducing the speed at which fire and smoke can spread, and I’m a huge proponent of it. Fire-resistant performance The system is devised to reinstate the fire-resistant routine of rigid and flexible wall and floor structures The system is designed to reinstate the fire-resistant performance of rigid and flexible wall and floor constructions where a retrospective cavity barrier is required. I think it’s the best solution for a huge number of cases where remedial work is required. It can be installed in residential, commercial, industrial and public buildings and the work can be carried out in-situ. Without the need to remove the whole building façade, projects can take weeks rather than months and cut out significant costs. When we look at why delays are happening, and the number of buildings where action is yet to be taken, it’s obvious that these are key stumbling blocks. Recent fire in Dagenham We’ve gained experience up and down the country, from London to Manchester, working in fire safety and have identified a number of areas which we hope that we can further improve on. Early reports from the recent fire in Dagenham suggest that the fire alarms sounded too late or were not activated at all. The cause of this has not been formerly identified, however, I envisage, and we are actively developing an ‘early warning system’, that could be installed within any wall, floor or ceiling cavity. The system could then be linked to a current fire alarm system, and/or App on your mobile phone. Expertise in sensor technology Fire can spread quickly before penetrating rooms where it would activate conventional fire alarms The benefit of this system, which would leverage our existing expertise in sensor technology, would be the ability to detect fire and smoke where conventional systems wouldn’t be able to. Where a fire is outside of the core of the building, our system would sit within cavities where fire can spread quickly before penetrating rooms where it would activate conventional fire alarms. In the event of a fire, response time is crucial. This would enable occupants to be able to leave the building or call Fire Brigade at an earlier opportunity, giving vital and potentially lifesaving time. Fire safety retrofitting The failure to address these issues could lead to further loss of life, economic costs, and legal liabilities. Fire safety retrofitting is not just about compliance but ensuring the long-term safety of residents and building occupants, particularly in densely populated areas where the risk of fire can have devastating consequences. We can make this happen far more quickly and ensure far more effective action is taken if we begin to think more imaginatively about the, giving people crucial time to act when disaster hits.
Are people too passive when it comes to fire door safety? Research conducted by the British Woodworking Federation (BWF) in 2022 would suggest so, with a third of the British public stating they would not report a problem with a fire door, despite three-quarters of respondents believing a propped open fire door would not perform its role in the event of a fire. From schools and shops to shared areas of employment and accommodation, people are habitually - and sometimes unknowingly - kept safe by passive fire protection systems such as fire doors and their hardware. Yet, in the same breath, occupants and visitors of busy public-facing buildings can be placed in danger by neglected or inappropriately used products. Highlighting these dangers, the Fire Door Inspection Scheme found 75% of inspected fire doors in the UK failed to meet required safety standards in 2021, for example. Importance of fire extinguishers Fast forward to the present day and perceptions are being challenged. Following a period of regulatory updates, greater focus is being placed on the responsibilities associated with both active and passive fire protection, and with a 79% rise in prosecutions related to fire safety violations between April 2023 and March 2024, it certainly pays to pay more attention. Where most recognize the importance of fire extinguishers and smoke detectors, what more can be done to ensure fire doors and their hardware are held in the same regard? Occupants and visitors of busy public-facing buildings can be placed in danger. Regulated and relied upon Passive fire protection is identified as the group of structural measures designed to inhibit the spread of smoke and fire. Frequently hidden in plain sight and sometimes taken for granted, fire doors are a key element of any building’s passive fire safety system and should never fall under neglect. In fact, fire doors are often the first line of defence against fire and smoke, and when closed, will compartmentalize spaces to protect property and provide occupants with an opportunity to escape. Fire doors are a key element of any building’s passive fire safety system. Such is their importance to public safety; fire doors are acknowledged by several professional bodies and are listed as a legal requirement in all non-domestic premises and houses in multiple occupations (HMOs). Under the recently updated Regulatory Reform (Fire Safety) Order 2005, a building’s designated Responsible Person (RP) must perform regular duties to review the condition of fire door systems, while providing residents with access to comprehensive fire safety information in the process. Fire door hardware Functional fire doors and clear exit routes are critical in ensuring appropriate precautions and preventative measures are in place and as such, responsible persons must recognize that a building’s fire doors will not perform as intended unless essential hardware has been correctly specified, installed, and maintained. As correctly acknowledged by most of the British public, an open fire door is rendered useless in the event of a fire and to form an effective barrier against fire and smoke, fire doors must be capable of closing fully from an open position. When performing a closing action, a fire door will call upon its hinges, locks, latches and door-closing devices, and in the event of a fire, not one of these elements can fail. In view of this, fire door hardware is methodically designed and tested to support the integrity of fire doors. To meet necessary standards, a fire doorset must pass one or more of a series of standardized tests, confirming its UKCA and CE certifications and FD ratings. Users can identify a certified fire door by its label, usually found on the top edge of the door. Functional fire doors and clear exit routes are critical in ensuring appropriate precautions. Shared responsibilities and results As part of their research in 2022, the BWF found that almost half of those who neglect to report a problem with fire doors would not take action because they were unsure who to report it to, or cited it was simply not their place or role to report it. Seemingly then, in many cases, improved communication and education towards fire door safety can help mitigate risk and further raise standards across the built environment. In any circumstance, people must continue being urged to keep buildings safe by reporting damaged or propped open fire doors to designated responsible persons. In higher-risk buildings where many rely on the same fire safety systems for example, it’s imperative that people know who they can turn to when a fire door safety issue arises, and often, this will be the landlord, owner, manager, or occupier of the premises. Equally, responsible persons must also adopt a hands-on approach by ensuring fire doors and their hardware are ‘subject to a suitable system of maintenance and are maintained in an efficient state, in efficient working order and in good repair’, as per the Regulatory Reform (Fire Safety) Order 2005. Higher-risk buildings where many rely on the same fire safety systems. True purpose of fire doors Where a fire alarm will inform you when something is wrong, fire doors require more proactive methods. As part of their ongoing maintenance duties, responsible persons should perform quarterly checks on fire doors, assessing the certification, gaps, seals, hinges and closing elements. Even durable door hardware can become worn and tired in high-footfall environments and may need repairing or replacing over time. An incorrectly installed or damaged self-closing device, for example, can limit the closing action of a fire door and prevent it from fully closing into the frame. Upon inspection, if a fire door isn’t operating as intended, it’s imperative to seek out professional advice and ensure maintenance or replacement is carried out quickly and professionally. Whilst many of us use them day to day without thought, the true purpose of fire doors must remain clear at all times. Collectively, we must continue to change the perceptions associated with passive fire protection methods and fire door safety, and only when we improve collaboration and communication will we truly limit the devastation of fire. Simply put, there is a chain of responsible parties, and everyone must recognize what their role is - we all must do better. Fire doors require more proactive methods. How Allegion UK can help Allegion UK has a wealth of resources designed to help responsible persons, duty holders and professionals undertake product selection, installation and maintenance checks on fire doors and hardware. For accessible fire door hardware support, Allegion’s new ‘Fire Door Hardware Fundamentals’ guide is available for download and combines expert guidance with helpful terminology and useful fire door safety checklists.
When fire safety fails, lives are put at risk. In all buildings, reasonable steps must be made to reduce the likelihood and impact of fire, yet, many people remain unsure and indecisive toward fire safety practices and the roles and responsibilities associated with fire door safety. In view of this, in October 2023, new fire safety legislation was introduced to non-domestic properties in England and Wales. Section 156 of the Building Safety Act 2022 (BSA) has made a number of amendments to the Regulatory Reform (Fire Safety) Order 2005 (FSO), with the latest improvements forming a new framework designed to improve fire safety in all regulated buildings, including workplaces, educational, healthcare and leisure premises and the shared areas of Houses in Multiple Occupation (HMOs). Fire safety reform program In short, Phase 3 of the fire safety reform program further strengthens fire safety in all FSO-regulated premises by: improving cooperation and coordination between Responsible Persons (RPs) increasing requirements in relation to the recording and sharing of fire safety information thus creating a continual record throughout a building’s lifespan making it easier for enforcement authorities to take action against non-compliance ensuring residents have access to comprehensive information about fire safety in their building The latest updates are comprehensive and aim to eliminate any ambiguity associated with fire safety compliance. And so, with greater emphasis being placed on accountability and all-around coordination, how should responsible persons approach fire doors and their hardware? Competence and coordination Fire doors are a key element of a building’s passive fire protection system and an area that elected RPs must possess a robust knowledge of, if they are to comply with the latest regulations. Equally, to keep buildings and occupants safe, responsible persons are required to perform various duties under the Regulatory Reform (Fire Safety) Order 2005, which include: Undertaking regular fire risk assessments Implementing appropriate fire safety measures Creating and maintaining a fire safety plan Providing relevant fire safety information Regular testing and maintenance of fire safety equipment and systems Coordination with relevant authorities and other responsible persons Provision of information to a new responsible person when departing the role fire risk assessments Functional fire doors and clear exit routes are critical in ensuring appropriate precautions and preventative measures are in place. Adding to this, responsible persons are required to review the condition of their fire doors when conducting, recording, and keeping written records of fire risk assessments, which consist of: Identifying fire hazards Identifying people at risk Evaluating, removing, or reducing the risks Recording findings, preparing an emergency plan, and providing training Reviewing and updating the fire risk assessment regularly Fire doors are often the first line of defense against fire. When closed, they compartmentalize and delay the spread of fire and smoke while protecting property and providing occupants with an opportunity to escape. In contrast, duty holders must recognize that a building’s fire doors will not perform as intended unless essential hardware has been correctly specified, installed, and maintained. Reducing the gaps Incorrect hardware specification is a common problem associated with fire door safety Incorrect hardware specification is a common problem associated with fire door safety. When selecting fire door hardware, it’s important that any chosen door application meets the required fire ratings, performance ratings, and latest legislative requirements. For example, all doors located on an escape route must have suitable exit hardware installed, which is determined by a number of factors including building size and whether it is public-facing or not. In addition, it is also a legal requirement for all exit devices to comply with the latest revisions of EN 1125 or EN 179 and to possess UKCA and CE markings. Fire door integrity Similarly, one of the most significant gaps in fire safety is the installation of fire door hardware. Fire door integrity can quickly become compromised by hardware alignment issues and improper installation methods. As a result, the door may not be able to latch or close fully from its standing position, leaving gaps large enough for fire and smoke to pass through. While there is currently no legal framework to assess the competency of installers, responsible persons are encouraged to appreciate that installation is a specialized task. During installation, installers must also look to follow manufacturer guidelines and fittings instructions, which should be supplied with all third-party certified fire doors and hardware. Regular fire risk assessment duties A competent assessor must ensure that the entire fire door is in working order and door integrity When it comes to maintenance, it’s vital to recognize that even durable door hardware can become worn and tired in high-footfall environments and may need repairing or replacing over time. A damaged or ineffective self-closing device, for example, can limit the closing action of a fire door and prevent it from fully closing into the frame - rendering it useless in the event of a fire. As part of regular fire risk assessment duties, responsible persons should perform quarterly checks on fire doors - as well as annual checks on flat entrance doors and self-closing devices in HMOs. A competent assessor must ensure that the entire fire door is in working order, reviewing the certification, door integrity, glazing, gaps, seals, hinges, and closing elements. If a fire door isn’t operating as intended, it’s imperative to seek out professional advice and ensure maintenance is carried out both quickly and professionally. Fire door hardware solution In any circumstance, under the latest regulations, responsible persons must cooperate, coordinate and share necessary information with others in order to comply. With that in mind, dependable fire door hardware devices will be supplied with full product information from the manufacturer - including the Declaration of Performance (DoP), third-party certification, and product data sheets. Transparent and accurate construction product information is more readily available than ever before and highlights whether a product complies with the necessary standards - helping duty holders to ensure the most suitable fire door hardware solution is being applied in the correct way. More than that, with it being made easier for enforcement authorities to act against non-compliance, it is necessary to become educated on key fire door safety themes, such as specification, installation, and maintenance. While fire safety practice may be complex by nature, it pays to understand the fundamentals.
Editor's Dispatch
NFPA 1900, a new standard, applies to any fire apparatus purchased beginning in January 2024. The National Fire Protection Association (NFPA) has introduced a new, broader standard that encompasses the content previously contained in separate standards for automotive, wildland fire, aircraft rescue and firefighting vehicles, and automotive ambulances. The new standard is a soft-covered book containing 375 pages and incorporating 34 chapters and 10 indexes. NFPA 1900 Standard Most fire departments will not buy an apparatus that is not NFPA-compliant. Additional changes to the NFPA 1900 standard reflect the trend toward newer technologies such as electric fire vehicles and LED lighting. The previous standard specified the use of equipment such as an alternator or a muffler that is not required with an electric apparatus. New standard specifies such equipment is only required in the case of an internal combustion engine The new standard specifies such equipment is only required in the case of an internal combustion engine (but not for an electric vehicle). On the other hand, unique electric vehicle safety requirements are added. The chapters are written in a way to distinguish between electric propulsion and internal combustion engine propulsion. Specific seating requirements The ability of LED lighting to provide greater intensity is addressed by guidelines allowing for a warning light “night mode” that avoids a distracting contrast between very bright flashing lights in a dark environment. In the daytime, the brighter lights increase visibility, exceeding the minimum requirements previously set by NFPA. More specific seating requirements make a distinction between seats that are intended to be occupied on every response, which is larger, and those provided only for occasional use. The intent of the requirement is to maximize the comfort of personnel who will be riding in the cab most of the time. Clean cab features are not required in the new standard, but guidance is provided in the annex for those wishing to adopt clean cab procedures. NFPA 1910 aerial test Chevron striping on the end of the device can vary in color as long as it is retroreflective and opposite The new standard requires a rear-view camera on all apparatus. Chevron striping on the rear of the apparatus can vary in color as long as it is retroreflective and contrasting. Operator manuals must be available as a hard copy on the apparatus, as an electronic display, or as a QR code to a website download. The operator manual must include all the information the Underwriters Laboratory (UL) would need to perform the annual and five-year NFPA 1910 aerial test. The other hundreds of features listed in the standard range from better weather resistance of door seals to better vehicle control during emergency braking to a harder finish and better UV protection of paint. Current issue of NFPA 1900 NFPA is titled “Standard for Aircraft Rescue and Firefighting Vehicles, Automotive Fire Apparatus, Wildland Fire Apparatus, and Automotive Ambulance.” It replaces previous standards NFPA 414 (covering airport firefighting vehicles), NFPA 1901 (covering automotive fire apparatus), NFPA 1906 (for wildland fire apparatus), and NFPA 1917 (for automotive ambulances). While NFPA 1901 and 1906 officially disappeared in January 2024, there are some references to the previous standards included in the current issue of NFPA 1900. There are some references to the previous standards included in the current issue of NFPA 1900 The standard seeks to limit its requirements to cover the design, performance, acceptance, and testing of apparatus, not focusing on what equipment is carried on the apparatus. Therefore, NFPA 1900 no longer requires a specific hose, ladder, or miscellaneous equipment to be included; rather that information has been moved to the annex as recommendations rather than requirements. Development of any NFPA standard NFPA standards are formulated by technical committees and task groups that consider each change. Anyone can comment on or make suggestions and recommendations for the development of any NFPA standard, and revisions take place over the course of multi-year cycles. A second main standard covering fire apparatus is NFPA 1910 “Standard for the Inspection, Maintenance, Refurbishment, Testing and Retirement of In-Service Emergency Vehicles and Marine Firefighting Vessels.”
Information systems drive greater situational awareness when emergency responders are rushing to the scene, including access to live-911 audio feeds, video of the unfolding emergency, and/or geographic information showing the locations of fire hydrants and the best travel route to ensure the most rapid response. Information tools to manage emergency response include the locations of teams, vehicles, and personnel available in three dimensions, including locations in a multi-story building. Panasonic’s technology “First responders are thinking about getting to the scene and planning their disaster response,” says Aidan Clifford, Panasonic’s National Sales Manager. Vital information on the scene of an emergency includes video feeds, coordination with other services in the city or county, and communication with various responding agencies. Providing hardware to manage information during emergency response, Panasonic works to understand “the voice of the customer.” The company’s TOUGHBOOK ruggedized laptop computers serve the needs of fire and emergency response entities. A new Fire Advisory Council, currently being assembled, will help to guide Panasonic’s technology direction, and increase their understanding of the practical information needs of firefighters and other emergency responders. Panasonic survey Panasonic survey, 55% of respondents said access to real-time data is a top priority for their agency “The goal is to provide more information to end users more quickly,” says Marcus Claycomb, Panasonic’s Business Development Manager for the Public Sector. “Better information can save response time and enable first responders to adjust the type of response in real-time.” For example, streaming video can provide details of an unfolding emergency to firefighters as they are driving to the call. In a Panasonic survey, 55% of respondents said access to real-time information is a top priority for their agency. Useful information includes who is on the scene and where they are in real-time. Smart devices can track locations and vitals. Information goes in two directions. The ongoing deployment of 5G communications and devices will ensure information moves even faster and is more actionable. Live-911 capability Also in the Panasonic survey, 62% of respondents said computer-aided dispatch (CAD) and geographic information system (GIS) data are mission-critical. GIS data can include “layers” of information imposed on a map to show the fastest route to an incident and the locations of fire hydrants and/or accessible video cameras. Some 85% in the survey said the most important pieces of information are the location of teams, vehicles, hydrants, and/or personnel. Location and communication with drone assets are also a requirement. Live-911 capability can enable first responders to hear the dispatcher speaking with a caller in real-time. “A dispatcher can push the 911 call through the TOUGHBOOK laptop to responders on route to a call,” says Clifford. “It is an emerging technology that integrates with computer-aided dispatch (CAD) systems.” privacy of HIPAA data Device encryption and multi-factor authentication to secure the information, even ensuring the privacy of HIPAA data during an emergency medical call. Panasonic understands that fire and emergency departments need real-time information Broadly speaking, Panasonic understands that fire and emergency departments need real-time information provided by rugged devices that can withstand the daily rigors of firefighting. In the survey, 85% of respondents said rugged computer devices are important, as opposed to using consumer devices in the harsh environment of firefighters and EMS personnel. (Conducted in April 2023, the Panasonic Connect survey generated 117 responses from individuals in the fire rescue industry.) Total cost of ownership While first responders understand the importance of using ruggedized devices, purchasing decisions are not always made by those on the front lines. Sometimes it is someone else at the city or county level who decides to buy consumer-grade hardware, especially tablets, in lieu of a ruggedized laptop. Multiple problems can result, such as “battery swelling” and fire hazards if a battery overheats because of the high internal temperatures in a vehicle. Consumer devices are not designed to operate in temperatures above 100°F. Cost is the main reason to opt for less expensive consumer-grade equipment, but the lower cost is an illusion. The math is very different if one considers the total cost of ownership (TCO), including any downtime resulting from a battery charge not lasting the entire shift, for example. Panasonic's TOUGHBOOK laptops First responders should work to ensure their voices are heard as purchasing decisions are made Ruggedized equipment is more resistant to being dropped. Panasonic's TOUGHBOOK laptops meet the MIL-STD-810H specification and ingress protection (IP) standards, IP65 and IP66, which test for ruggedness and resistance to solids and liquids. Additional features include enhanced connectivity and embedded antenna, non-breakable components, and all-day batteries. First responders should work to ensure their voices are heard as purchasing decisions are made. They should have a conversation with command-level employees and throughout the fire service to ensure equipment purchasing reflects the real needs on the front lines, says Claycomb. What's Ahead? What’s ahead for information technology on the front lines of firefighting? “There is an incredible opportunity ahead to integrate the TOUGHBOOK with fire vehicles,” says Marcus. He adds, “And the potential of using 5G will be limited only by our own creativity. Looking ahead, we can expect more artificial intelligence (AI), augmented reality (AR), and an incredible amount of data.”
Two grant programs designed to address staffing, equipment, training, and health and safety needs of firefighters are scheduled to ‘sunset’ in 2024 unless Congress reauthorizes the grant programs, and funding for the programs will run out unless Congress endows them for another year. Legislation to extend the programs has already passed the U.S. Senate. The Staffing for Adequate Fire and Emergency Response (SAFER) grant program provides funding to hire additional personnel to maintain safe staffing levels in fire departments. The Assistance to Firefighters Grant (AFG) program pays for equipment, training and other fire department needs. Together, they ensure the readiness of 30,000 fire departments across the U.S. to respond to more than 30 million emergency calls annually. Introducing bipartisan legislation U.S. Senator Gary Peters, Chairman of the Homeland Security and Governmental Affairs Committee, introduced bipartisan legislation to reauthorize SAFER and AFG programs, and to provide funding for the United States Fire Administration (USFA). Other authors of the bipartisan legislation are Republican Senators Susan Collins of Maine and Lisa Murkowski of Alaska; and Democratic Senator Tom Carper of Delaware in addition to Democrat Peters. The bill was approved by the Senate Homeland Security Committee and then moved to the full Senate Current authorization of funding for all three programs expires in 2023. The bill was approved by the Senate Homeland Security Committee and then moved to the full Senate for consideration. The Senate approved the bill on April 20. Senate Majority Leader Chuck Schumer earlier pledged to pass the Fire Grants and Safety Act of 2023 in the Senate to save the programs. In addition to reauthorizing the programs for another year, the bill extends the sunset from 2024 to 2030. Federal grant programs The bill also extends through 2030 the underlying formula for the authorizations of appropriations for the grant programs; those amounts are calculated by adjusting the amount authorized for 2013 ($750 million) each year to account for inflation. In November 2022, Michigan Congressman Dan Kildee announced legislation in the House to renew the two federal grant programs critical to local departments. The Fire Grant and Safety Act would extend the grants until 2030. The Department of Homeland Security (DHS) Federal Emergency Management Agency (FEMA) is responsible for the implementation and administration of the grant programs through the Grant Programs Directorate. Modern pumper truck Outfitting one firefighter with protective gear and breathing apparatus can cost $12,000 “These federal grant programs have delivered millions of dollars to departments and municipalities to [provide] the equipment and staffing levels [needed] to respond to fires and countless other emergency calls as safely and efficiently as possible,” said Sam Fresina, President of the New York State Professional Firefighters Association. Fire departments often face budget shortfalls and high costs that prevent them from investing in modern equipment to combat emergencies and keep firefighters safe. For example, a modern pumper truck can cost more than $750,000. Outfitting one firefighter with protective gear and breathing apparatus can cost $12,000. Providing recruitment incentives “Volunteer and combination fire and EMS departments struggle to get the funding they need to keep the lights on, fuel the ambulance, and purchase turnout gear,” said National Volunteer Fire Council Chair Steve Hirsch. “The AFG and SAFER programs are critical to these departments because they allow them to purchase needed equipment and provide recruitment incentives to volunteers to serve their community.” Other organizations supporting reauthorization of the grant programs and extension of the ‘sunset’ include the International Association of Fire Chiefs (IAFC), the Congressional Fire Services Institute (CFSI), the National Fallen Firefighters Foundation, the International Society of Fire Service Instructors, the International Association of Fire Fighters (IAFF), and the National Fire Protection Association (NFPA).
Case studies
Contemporary Atrium Hotel has put its trust in Amthal Fire and Security to deliver an enhanced fire safety maintenance service, for the safety of staff and guests. Conveniently situated within a five-minute drive from Heathrow Airport, Atrium Hotel stands as a premier urban retreat, boasting 573 meticulously designed ultra-chic bedrooms. all-in-one cloud platform Ensuring fire safety measures are compliant with the latest legislation, the hotel site team worked closely with Amthal to develop a complete maintenance program. Amthal’s status as an approved Honeywell Gent partner enabled it to utilize Honeywell’s Connected Life Safety Services (CLSS) for Atrium Hotel. Honeywell’s CLSS is an all-in-one cloud platform to maintain the fire systems across the hotel facilities and maximize performance, with minimal disruption to the hotel’s operations. operational efficiency Francisco Quintero, Maintenance Manager at The Atrium Hotel Heathrow, says, “The hotel is built on a commitment to exceptional service, ensuring every aspect of a stay is seamlessly taken care of. While its core objective is to offer the latest and contemporary amenities; the safety and security of our hotel experience is critical." “From an operational efficiency and compliance perspective, we needed to ensure the right approach to maintaining our fire safety systems." real-time visibility Amthal can present CLSS to maintain all fire systems across the site, alongside testing emergency lighting "Amthal offered advice and practical support on how this could be achieved remotely, with Honeywell CLSS. It enables real-time visibility to enhance timely, accurate decision-making by on-premise and remote staff, a great benefit to us all.” As an approved Honeywell Gent partner, Amthal can present CLSS to maintain all fire systems across the site, alongside testing emergency lighting, emergency voice communications, and regular fire door testing. This provides a complete and compliant fire protection service for The Atrium Hotel. push notification Mark Hunter, Honeywell Gent Business Manager added, “Fire safety is one of the biggest challenges presented in any hotel environment. A need to balance an ongoing welcoming and relaxing environment that doesn’t compromise on the safety of guests." “What Amthal demonstrates at The Atrium Hotel is the importance of not just installing the right specification of systems, but also maintaining them to maximize performance. This can be achieved with CLSS remotely to ensure less disruption and time on site from testing, with push notification of events to mobile devices to alert staff of any specific findings. It all comes together to achieve undisputable compliance from the hotel perspective.” seamless and efficient maintenance service David Williamson, Amthal Sales Manager concludes, “We are proud to partner with The Atrium Hotel to ensure their fire safety systems are not only up to date but also maintained to the highest standard." “By leveraging the capabilities of Honeywell CLSS, we can provide a seamless and efficient maintenance service that aligns with the hotel's commitment to safety and excellence. With total protection and guaranteed compliance, staff can be assured of fire safety maintenance measures in place. And they can focus on serving guests, allowing them to enjoy all the facilities and services available.”
Sprinklers, wall hydrants, nitrogen, and deluge extinguishing systems: Nothing is left to chance when it comes to preventative fire protection in the two buildings of DKV (German Health Insurance) in Cologne, Germany. In addition, a Rosenbauer employee is always on site to ensure full functionality and maximum fire safety. The DKV headquarters, built in the 1960s, is part of Cologne’s cityscape and has housed the central administration of the DKV for decades. Due to a need for more space, another office building was built in the immediate vicinity in the early 2000s. Both buildings are equipped with a wide range of preventive fire protection systems, which are looked after and maintained by Rosenbauer. Water tanks over multiple floors Different fire protection systems are used in the different areas of the building Different fire protection systems are used in the different areas of the building. On the one hand, this is a result of legal requirements and, on the other, provides fire protection that is as efficient as possible. The heart of the entire fire protection system is located on the lower floors of the two skyscrapers. The large water tanks extend over several floors. The sprinkler control panels and the associated pumping technology are also housed in these areas. The right system for every purpose Econ-Aqua systems are installed in most fire sections: These wet alarm valve stations are permanently pressurized and the pipes leading to the sprinklers are already filled with water. If the critical temperature is reached, a glass bulb breaks and water escapes from the sprinklers. The corresponding station opens and the pump system is activated by the water flowing in. This type of fire protection system is primarily used in standard offices, underground car parks, and technical rooms. Dry alarm valve station In contrast to the wet alarm valve station, the pipes in the dry alarm valve station are not filled with water, but rather with air. But these are also constantly pressurized. In the event of a loss of pressure - if the glass barrel breaks due to high temperatures - the extinguishing system is also automatically activated and pumps in water. Such dry alarm stations are mainly used in areas where there is a risk of frost, because frost damage cannot occur as there is no water. Special systems for sensitive areas The pre-controlled sprinkler groups are unique because their pipes are also dry The pre-controlled sprinkler groups are unique because their pipes are also dry. In order to further minimize the risk of false alarms and unnecessary water damage, they are only triggered when the fire alarm system in the same area is also triggered. Such pre-controlled systems are used in sensitive areas, such as archives. Nitrogen extinguishing systems were installed in the two DKV buildings to protect the control cabinets in the technical rooms. A pipe intake system allows air to continuously circulate, and this is guided past a smoke detector. As soon as this smoke detector is triggered, nitrogen is blown into the control cabinet and the fire is smothered before it can take hold. Fire protection for ventilation and kitchens Fire dampers have been installed to prevent smoke gases from spreading through the ventilation system in the event of a fire. Smoke and thermal detectors - as well as an extinguishing nozzle - are installed both upstream and downstream of them. In the event of a fire, water can be introduced here to flush the smoke gases out of the air. Special extinguishing systems are also used in the canteens: extinguishing nozzles are installed in extractor hoods, fryers, and other appliances. Running parallel to these is a pre-tensioned cable with melting plumb bobs, which – as the name suggests – will melt if a sufficiently high temperature is reached. This would release the ANSUL extinguishing agent, which is specifically suited to grease fires. The kitchen extinguishing systems can also be activated manually. ‘Zone Checks’ and wall hydrants installed There are also more than 100 wall hydrants distributed throughout both buildings There are also more than 100 wall hydrants distributed throughout both buildings, with a 30-meter hose on every floor. In order to be able to locate a fire quickly in the event of an emergency, almost 100 so-called ‘Zone Checks’ have also been installed. The two fire protection systems in the DKV skyscrapers in Cologne are among the largest systems managed by Rosenbauer in the German-speaking world. In addition, a Rosenbauer employee remains constantly on site to carry out maintenance work and statutory inspections. Rosenbauer Mastercontrol The Rosenbauer Mastercontrol, which is operated from inside one of the buildings, provides significant support in this regard. This system replaces time-consuming manual component checks with automated routines and not only offers the most accurate documentation through electronic measurement recordings, but also saves a lot of time and therefore costs. Thanks to systems that are perfectly tailored to the respective needs of the individual building areas, preventive fire protection can be optimally guaranteed. The sophisticated extinguishing technology ensures that a fire is extinguished before it can develop into a major threat, and thus fully lives up to the name ‘preventive’.
Comelit-PAC has been working with partners - GB Integrated Systems to fit the latest fire safety systems at the Hop House in Deva City Office Park, in order to ensure the safety of all who work and visit the unique work environment. Part of the former Threlfalls Brewery, an iconic feature of the Manchester city skyline, Deva City Office Park presents an eclectic mix of business space presented in a Grade II listed Brewery building or 17 high-spec self-contained office units. Balancing modern design GB Integrated System worked directly with the site management team to upgrade the addressable panels With the need to offer 24 / 7 security and fire safety, GB Integrated System worked directly with the site management team to upgrade the addressable panels, and specified Comelit-PAC’s latest LogiFire solution. Iain Taylor, Director of Asset Management at Northwood Investors International Limited, said: “We knew we had complex requirements for Deva City when it came to security and fire safety, with each individual business on site needing its own risk assessments. This was set against the buildings themselves, where any upgrades had to be sympathetic to the specific interest Grade II classification and balance modern design and use of technology.” Easy fire safety solution Iain Taylor adds, “GB Integrated Systems made it a priority to understand this and work with us right from initial design and specification to implement a bespoke solution that could accommodate our requirements. From a fire safety perspective, Comelit-PAC was recommended, to ensure we could reduce installation time and minimize disruption to business activity for the benefit of our occupiers.” GB Integrated System specified Comelit-PAC’s LogiFire Easy fire safety solution. The office park required a stand-alone 1-loop analog addressable panel. Fire safety solution We recommended Comelit-PAC’s Logifire solution essentially because of its simple design" Mike Gray, Technical Director at GB Integrated Systems, stated: “We recommended Comelit-PAC’s Logifire solution essentially because of its simple design, and ability to easily install using existing cabling, so as not to interfere with the style of the development and its unique character. From the owner’s perspective, its style and flexibility of use means that it is the best fire safety solution to protect the occupiers collectively and blend seamlessly with its surroundings.” Logifire addressable system, has been designed to offer a simple to install, fire safety solution that is compliant with BS and EN standards. It is complemented with a range of detectors, offered with award-winning designs to ensure systems blend with their surroundings. Mind fire safety Mandy Bowden, Comelit-PAC Fire Manager, concluded: “When it comes to fire safety, the market is growing rapidly amid greater awareness of the need for risk assessments, remediation work, building upgrades and ongoing maintenance in the new-build sector as well as at existing sites. What our work with GB Integrated Systems at Deva City Office Park demonstrates is the need to assess each development as early as possible in a works program to ensure solutions meet exact requirements." She adds, "We understood that any upgrade had to be carefully considered with regards to how it will impact on the aesthetics of the overall premises. Together, we identified how LogiFire as a single solution, could be installed quickly and effectively for the benefit of all who work on-site. It allows for total peace of mind fire safety.”
Oshkosh Airport Products, a division of Pierce Manufacturing Inc., a subsidiary of Oshkosh Corporation announces Airservices Australia has issued a purchase order for four Oshkosh Airport Products Striker® Volterra™ 6x6 Aircraft Rescue and Fire Fighting (ARFF) hybrid electric vehicles. These environmentally advanced fire apparatus will be deployed at the new Western Sydney International Airport (WSI), set to open in 2026. Striker Volterra 6x6 The Striker Volterra 6x6 comes equipped with an Oshkosh-patented hybrid-electric drivetrain, featuring an electro-mechanical infinitely variable transmission. This enables zero-emissions operation through the integrated onboard batteries and uninterrupted power supply by coupling with the internal combustion engine for pumping and drive systems. innovative design Airservices Australia is making a significant investment to support the development of an 'airport of the future' WSI is a transformational infrastructure project expected to boost economic activity, provide local employment opportunities, meet Sydney's carbon-neutral sustainability initiatives, and meet the area’s growing aviation needs. Airservices Australia is a government entity making a significant investment to support the development of an 'airport of the future', featuring world-pioneering technology, innovative design, and a sustainability plan incorporating assets like the Striker Volterra ARFF hybrid electric vehicles. sustainability "As the first airport built in Australia in over 50 years, WSI is not just an airport; it's a statement of intent for a more sustainable future,” said Dave Archer, Vice President of Engineering for Oshkosh Vocational. He adds, “The Striker Volterra vehicles, with their hybrid electric technology, align perfectly with Airservices Australia and WSI’s goals. These vehicles are not only an asset to emergency response capabilities but also play a crucial role in larger environmental sustainability initiatives." environmentally conscious choice Dave Archer continues, "They symbolize a dedication to intelligent design, energy optimization, fire crew safety and efficiency, and ultimately, a carbon-neutral future." Striker Volterra ARFF hybrid electric vehicles demonstrate the most advanced acceleration and reduced fuel consumption compared to our standard diesel models, making them an environmentally conscious choice for emergency response services. Striker Volterra features Striker Volterra ARFF demonstrates a 28 percent improved acceleration compared to the standard diesel models WSI’s four new Striker Volterra 6x6 vehicles will feature an industry-pioneering modular cab design, TAK-4® all-wheel independent suspension, and a 50’ Snozzle® High Reach Extendable Turret. They each house an 11,356-liter (3,000-gallon) water tank, a 1,590-liter (420-gallon) foam tank, and a 7,570 lpm (2,000 gpm) water pump, along with a 250 kg (550 lb.) dry chemical powder system. Accelerating from 0 to 80 kph (0 to 50 mph) in under 25 seconds, the Striker Volterra ARFF demonstrates a 28 percent improved acceleration compared to the standard diesel models when fully loaded. training, implementation, and service support Dave Archer said, “The collaboration between Oshkosh Airport Products and Airservices Australia marks a significant step forward in the aviation industry's commitment to sustainability." He adds, "We remain committed to a strong partnership, providing world-class training, seamless implementation, and unwavering service support to ensure these vehicles exceed expectations in the critical missions of ARFF crews.” By leveraging new technologies and innovations like Oshkosh Airport Products’ Striker Volterra ARFF hybrid electric vehicles, WSI will showcase the feasibility of low-carbon operations and set a new standard for airports worldwide.
Industry pioneer - AEI Cables has clinched a contract to supply its low-voltage power, control, and fire performance cables to a major extension of the Hong Kong Sports Institute. Working with its partners, Cornwall Contracting Co.Ltd, AEI Cables supplied the cables to the existing sports complex from 2011 to 2013. Extension features The major extension involves the facilities development building, which is located in front of the indoor swimming pool and rowing boathouse comprising a three-storey building area. This will feature a multi-purpose training hall, scientific conditioning facilities, a sports medicine center, sport psychology, sports biomechanics, sports nutrition, and monitoring center, and a sports residence area. Quality cabling The Hong Kong Sports Institute is a major sports complex located in Sha Tin Stuart Dover, General Manager of AEI Cables, said, “This is a major development of the institute and we’re thrilled to be working on such a prestige project with our partner to ensure the highest quality of cabling is installed.” The consultant engineer will be WSP Hong Kong Ltd and the electrical sub-contractor is Cornwall Contracting Co. Ltd. The Hong Kong Sports Institute is a major sports complex located in Sha Tin, New Territories, Hong Kong, offering training to athletes and academic qualifications in the field of sports training. Fire performance cabling Using the very latest in technology and science, AEI Cables’ specialist Firetec Total Fire Solutions range offers enhanced fire performance cabling, accessories, and technical support from its distribution facility at Washington, Tyne and Wear. Applications for Firetec include residential and commercial buildings, shopping malls, airports, and protected buildings ensuring that fire alarms, sprinkler systems, building monitoring, and security systems can continue to operate in a fire. All AEI Cables’ products are supplied with approvals from independent bodies including BASEC and LPCB. It also holds approvals from organizations including Lloyds, the MoD, Network Rail, and LUL and works to international standards around the world.
Fire protection solutions manufacturer, Advanced, has supplied intelligent fire panels to residential apartment buildings in Roscam, in County Galway, Ireland. The eight residential apartment blocks in Roscam are now protected by Advanced’s Go, its new-generation, single-loop fire alarm control panel. Fire and security service providers, Securecom Claddagh Ltd, carried out the replacement and upgrade of an aging fire alarm system, installing a Go panel in each of the three-storey apartment blocks. Advanced Fire Panels Go panel was installed near the front door of each building, covering their hallways and landlord areas A Go panel was installed near the front door of each building, covering their hallways and landlord areas. The panels were hard-wire integrated with Apollo detectors and with a CSL fire-specific remote monitoring communication device that communicates to an alarm receiving center, allowing the relevant key holders to be informed when triggered. Securecom Claddagh has been using Advanced fire panels for a number of years in its projects due to their ease of programming and standardization across sites, as well as the panels allowing effective technical phone support from Advanced in the event of a fault or unwanted alarm. Author's Quote Jason Small, Director at Securecom Claddagh said: “Advanced supplies fantastic equipment, which is very reliable and offers the same interface whether installing a Go panel on a small site or using an MxPro 5 fire panel for a larger networked site, such as a hotel or factory.” Go was developed so customers can benefit from the performance, reliability, and flexibility Neil Parkin, Advanced Sales Manager for the North, said: “Our Go fire panel features the same interface as our other Advanced fire panels, which means fire and security providers are familiar with how they work, ensuring quick installation. The Go provides sophisticated Advanced configuration but with a single loop making it ideal for small or standalone projects, like the Roscam apartment buildings, that still want robust fire protection to offer real peace of mind. Go was developed so customers can benefit from the performance, reliability, and flexibility they’ve come to expect from our premium MxPro 5 range, but in a cost-effective, single-loop format for simpler sites where networking’s not needed.” Intuitive New Configuration Software Go is the ideal solution for a wide range of single-panel sites – from restaurants, bars, and guesthouses to small offices, shops, salons, and surgeries. On straightforward jobs, Go’s fuss-free installation and configuration save time and money. However, the new panel also makes light work of more complex sites requiring sophisticated cause-and-effect programming options as well as false alarm management and reduction solutions. Go has been developed with the needs of installers, engineers, and end users firmly in mind. A host of features make Go a breeze to set up. An easy-fit chassis with a unique door design enables fast fitting, while familiar controls and menus mean there’s no lengthy learning curve. Intuitive new configuration software makes programming quicker and easier than ever, and a powerful design checker proves the system will work even before visiting the site. In addition, enhanced diagnostics mean fewer faults, faster fixes, and better long-term performance. Site-Specific Installations Cost efficiencies for customers central to Go’s development, delivering maximum functionality Cost efficiencies for customers have also been central to Go’s development, delivering maximum functionality on a small-site budget. The panel has 15 zonal LEDs as standard for clearer visual indication and BS 5839 compliance without the need to buy a separate LED zone card. Compatibility with three pioneering detector protocols provides wired and wireless options, as well as greater freedom over design and maintenance provider costs. Further cost savings as well as greater flexibility for site-specific installations are available thanks to a choice of two performance options with different maximum numbers of configurable addresses. Advanced Product Portfolio As a world pioneer in the development and manufacture of intelligent fire systems, Advanced is committed to creating a safer future. A reputation for performance, quality and ease of use see Advanced products specified in locations around the world, from single-panel installations to large, multi-site networks. The Advanced product portfolio includes complete fire detection systems, multiprotocol fire panels, extinguishing control, false alarm management and reduction solutions as well as emergency lighting. Advanced is owned by FTSE 100 company Halma PLC – a global group of life-saving technology companies with a clear purpose to grow a safer, cleaner, healthier future for everyone, every day.


Round table discussion
Technology has played a role in firefighting since the beginning; in fact, portable water pumps were found among the ruins of ancient Egypt. As bucket brigades gave way to electric pumps and internal combustion motors displaced horse-drawn fire engines, firefighting has benefited in terms of greater efficiency and lives saved at each point along the way. Technologies boosting the efforts of firefighters include drones, robots and other high-tech innovations. We asked our Expert Panel Roundtable: Which technologies will we see in ‘the future of firefighting'?
Thermal imaging is an advantageous tool for firefighters on the frontline. As thermal cameras have become more compact and affordable, their availability has expanded, along with their usefulness. We asked our Expert Panel Roundtable: How does thermal imaging serve the needs of firefighters and how is it changing?
Products


Videos
Passive Fire Protection (PFP): Manufacturers & Suppliers
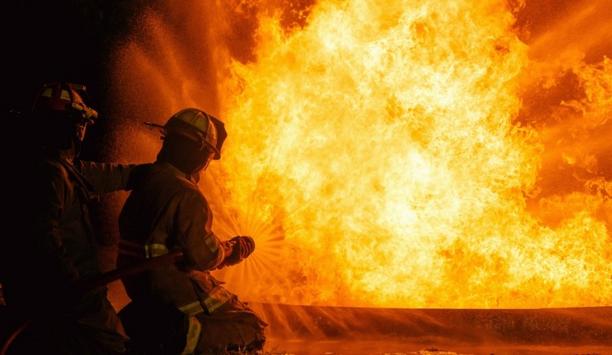
The New Future For Fire Agencies
Download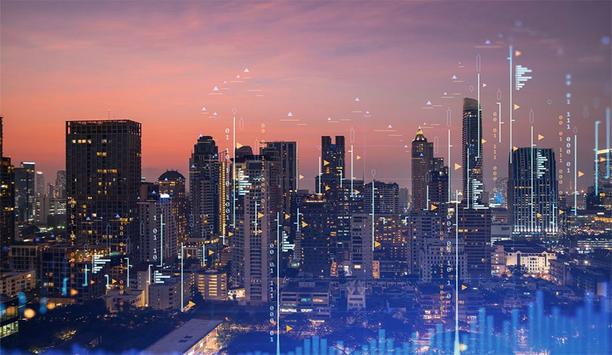
The Eight Key Trends in Fire Detection in 2023
Download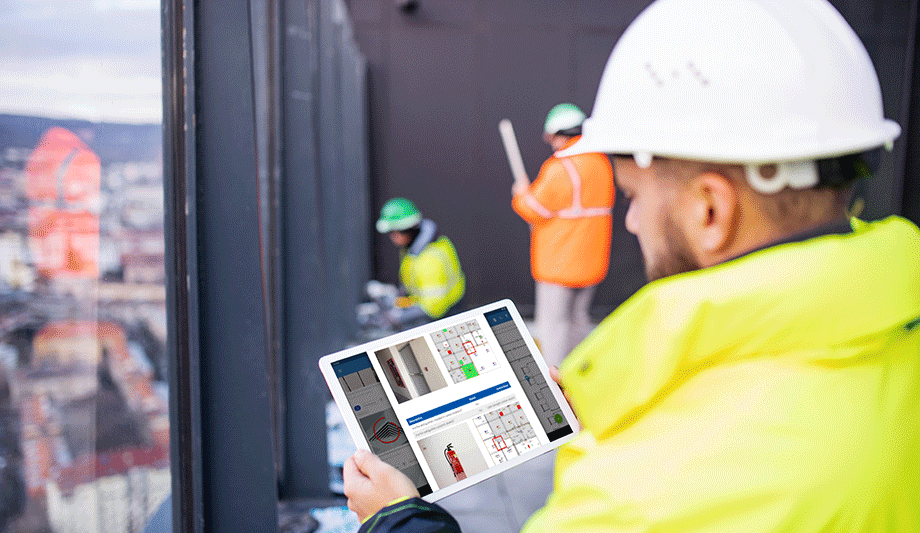
A Digital Platform to Improve Fire Safety Compliance and Inspections
Download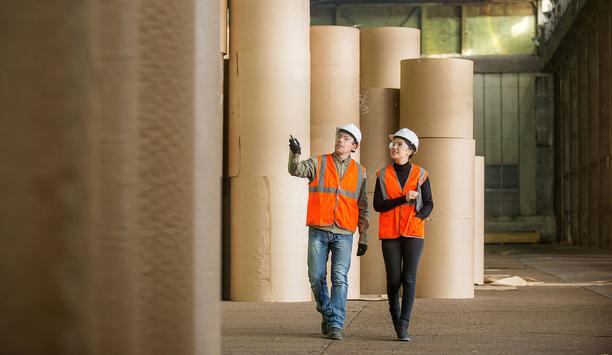
Overcoming the Challenges of Fire Safety in the Paper Industry
Download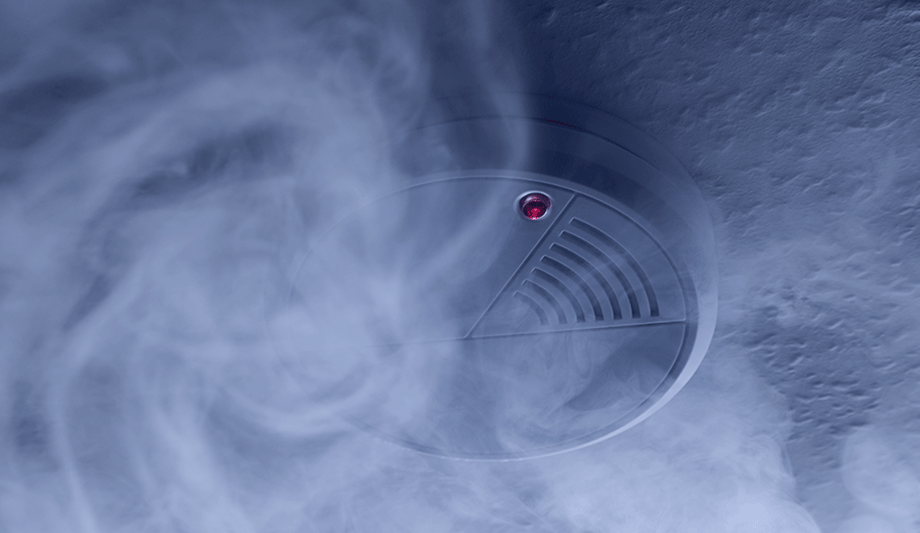
Carbon Monoxide: Creeping Killer Caught In The Act
Download