Personal Protective Equipment (PPE)
At FireRite they have always offered a range of fire safety training in different formats. They’ve offered a range of standard training packages as well as bespoke and tailored training to meet their specific needs. The way that they approach training delivery needs to adapt and change as the world moves into ‘the new normal’. The requirements and legislation relating to fire safety for businesses have not gone away or been relaxed during the lockdown. Fire safety training is...
The largest UK fire and rescue service convoy is set to deliver more than 15,000 pieces of life-saving firefighting equipment to Ukrainian firefighters. Donated by UK fire and rescue services, working with FIRE AID, the eighth convoy - including 26 donated fire engines - will make its way across Europe next month (April). This eighth convoy adds to the 119 vehicles that have been donated, alongside 200,000 pieces of equipment since the invasion began. Full-scale invasion in 2022 The war...
As the potential last line of defense in critical situations at sea, personal protective equipment must be maintained to the highest of standards, with any damage recorded and flagged for repair. RFID track-and-trace technology is a game-changing PPE condition and service solution. Before leaving the manufacturing plant, all VIKING PPE is fitted with a durable radio-frequency identification (RFID) device that allows for monitoring of its servicing st...
The new VIKING YouSafe™ Vanguard is specially designed for the Offshore industry where ergonomics, comfort and freedom of movement are alpha omega for working conditions offshore personnel face. Keeping offshore crew safe is more than basic compliance. Working for long periods with complicated tasks that require full attention means that equipment must be as comfortable as possible and provide max. mobility. And it doesn't hurt to look good! Single point indicators The SOLAS/MED-approve...
Whether users are in the cockpit, kneeling at the winch, or hanging on the end of the cable, they’ve got users covered with protection that provides comfort and allows the best maneuverability so users can focus on the task at hand. All passengers and crew travelling by helicopter in hostile offshore areas as defined in JAR-OPS-3 must wear personal protective equipment with ETSO approvals, including immersion suits. Aviation safety requirements With an EASA (European Aviation Safety Aut...
VIKING Life-Saving Equipment has signed a strategic agreement with HeliService USA, ensuring that the helicopter service provider has a single and continuous source of fully certified personal protective equipment to uphold offshore wind industry safety standards along the U.S. East Coast. Building on enduring relations between the companies, the agreement includes personal protective equipment (PPE) for the aircrews and service technicians who support turbine installation and maintenance. VIK...
News
Shipowners and operators of EU vessels must take steps to ensure that all new firefighting suits on board comply with changes to European regulations which enter into force from June 2025, according to urgent advice from VIKING Life-Saving Equipment. The leading life-saving equipment solutions provider is recommending fleet managers undertake a full risk assessment of their firefighting suits to verify compliance with requirements applying under MED regulations (EU) 2024/1975. New firefighting suits New firefighting suits bought for EU vessels must feature all 3 of the enhanced protection capabilities These are in addition to provisions in effect since August 2024 - that all new firefighting suits must be tested to EN469:2020 standards. From June, all new firefighting suits bought for EU vessels must feature all three of the enhanced protection capabilities included in ‘Level 2’ classifications within MED regulations. While ‘Level 1’ fire suits in-service will remain compliant until they wear out, they must be replaced by Level 2 PPE once they are no longer fit for purpose or worn out. Risks of electrical fires on ships Developed in response to high-risk firefighting, Level 2 notation covers radiant and convective heat resistance (X2), enhanced water penetration protection (Y2), and breathability (Z2). The inclusion of Y2 responds to growing risks of electrical fires on ships and greater seafarer exposure to close-quarters firefighting in enclosed spaces where water is used in high volumes. Y2 suits feature an extra moisture barrier to protect firefighters against steam burns and chemicals. Electric vehicle and battery fires Y2 suits feature an extra moisture barrier to protect firefighters against steam burns “There has been widespread acknowledgement that seafarers need more protection, including from electric vehicle and battery fires, and in enclosed spaces,” explained Charlotte Nielsen, Product Manager PPE, Viking Life-Saving Equipment. “Owners recognize these needs but the most extensive fire suit rule changes for two decades are entering into force with unusual speed, so they also want to fully understand what is being asked of them.” firefighting gear compliance To avoid potential challenges from Port State Control, owners should verify their firefighting gear compliance by the date of purchase. “We recommend customers conduct risk assessments on the condition and certification of suits and update each vessel’s Safety Management System (SMS).” Level 2 marine fire suits The safety solutions provider expects a significant number of non-EU countries to follow VIKING has sold Level 2 marine fire suits since 2016 - all meeting X2 and Z2 protection levels. As new MED regulations enter into force, the safety solutions provider expects a significant number of non-EU countries to follow. UK legislation has already been amended to reflect Y2 requirements. Charlotte Nielsen reported strong uptake for the VIKING YouSafe™ Torch – VIKING’s latest Level 2, EN469:2020 certified fire suit. Superior heat and water protection Made for comfort, durability, and superior heat and water protection, the YouSafe™ Torch has already seen live use fighting fires at sea. “As a one stop shop for marine life-saving equipment, we respond well ahead of the regulators, with a strong lead provided by the products we develop for land-based firefighting professionals,” she said.
Ship fires are on the rise, posing serious risks to crews, vessels, and operations. Ensuring firefighting equipment meets the latest safety standards is not just essential — it’s lifesaving. The latest update to the Marine Equipment Directive (MED), (EU) 2024/1975, mandates significant changes to the approval and use of firefighting suits onboard European vessels. Here's what users need to know to stay compliant and protect the crew. Enhanced crew safety What does this mean for shipowners? To comply with the updated MED directive, shipowners must evaluate and future-proof their firefighting equipment. Existing suits in good condition can remain in use, but they advise planning for a timely upgrade. Supplementing or replacing suits with level 2 models ensures both compliance and enhanced crew safety. The VIKING YouSafe™ Torch firefighting suit meets the latest EN469:2020 standard The VIKING YouSafe™ Torch firefighting suit meets the latest EN469:2020 standard and is classified as level 2 for maximum protection. This suit is specifically designed for marine environments, combining superior heat resistance and waterproofing with crew comfort and durability. High-temperature environments What is a level 2 classified firefighting suit? Level 2 suits are designed to handle the challenges of firefighting in enclosed spaces. They offer: Superior heat resistance for high-temperature environments Enhanced water penetration protection which is critical when dealing with steam or water exposure Good breathability, ensuring crew comfort and performance during extended operations To identify a level 2 suit users must look for the X2,Y2,Z2 mark. Note: Level 1 suits remain compliant until worn out but do not offer the same advanced protection. Water penetration resistance VIKING understands the unique safety requirements for electric vehicles and AFVs, and can provide users with the equipment and expertise needed to ensure the appropriate fire protection. The VIKING YouSafe Torch firesuit is EN469:2020 certified, meeting the updated regulations. The EMSA recommends fire suits with level 2 water penetration resistance when fighting fires in electric vehicles and AFVs.
Each year, MSA Safety and DuPont Personal Protection partner with the National Volunteer Fire Council (NVFC) to provide Globe turnout gear and MSA fire helmets to volunteer fire departments in need. In 2024, 13 volunteer fire departments across the U.S. and Canada each received four new sets of turnout jackets, turnout pants, and helmets to help increase the safety of their responders. MSA also provided the first 500 applicants with an NVFC membership. Compliant with safety standards The donations have made a notable impact in enabling units to better protect their responders Since the program began in 2012, a total of 767 sets of gear and 312 helmets have been donated to 173 departments, totaling more than 2 million dollars in life-saving gear. Receiving departments faced limited budgets and resources, which prevented them from securing the sufficient quantity of gear they needed and/or left them using gear that was out of date and not compliant with safety standards. The donations have made a significant impact in enabling departments to better protect their responders. Enhance the safety of ground firefighters “Volunteer firefighters are the backbone of their communities, answering the call whenever their neighbors have an emergency,” said NVFC Chair, Steve Hirsch. He adds, “And yet many departments lack the funding to be able to provide state-of-the-art, up-to-date personal protective equipment for their responders. We are proud to partner with MSA and DuPont each year to help meet this need and enhance the safety of our boots on the ground firefighters.” Improve safety for firefighters “DuPont is honored to continue supporting the Globe Gear Giveaway program, which plays a crucial role in providing essential safety equipment to volunteer firefighters across the United States and Canada. We strongly believe that those who protect their communities deserve the very best protection,” said Stephanie Vrakas, NA Marketing Manager, DuPont Personal Protection. “At MSA, our mission is helping to keep people safe at work, including firefighters who are helping to keep their communities safe,” said Ben Mauti, Director of Americas Segment Marketing at MSA Safety, adding “We’re proud to be supporting this program and helping to improve safety for firefighters at fire departments that are most in need, so these firefighters have the protective equipment they need when their community calls on them for help.” Recipients of the 2024 MSA The recipients of the 2024 MSA and DuPont’s Globe Gear Giveaway are as follows: Cornettsville (KY) Fire Department Hessmer (LA) Fire Department East Galesburg (IL) Volunteer Fire Department East Glacier Park (MT) Volunteer Fire Department Elmore Fire Department (Lake Elmore, VT) Gander Bay Fire Department (Wing’s Point, NL, Canada) Hasbrouck Heights (NJ) Fire Department Keating Rural Fire Protection District (Baker City, OR) Prater Fire and Rescue (Grundy, VA) Samburg-Reelfoot Volunteer Fire Department (Hornbeak, TN) Tanner Volunteer Fire Department (Athens, AL) Taylorstown (PA) Volunteer Fire Department Terre Du Lac Fire Department (Bonne Terre, MO). DuPont’s Globe Gear Giveaway To be eligible to apply for the giveaway, departments must be over 50 percent volunteer, serve a population of 25,000 or less, be located in the U.S. or Canada and legally organized under state/province law, demonstrate a significant need for new gear, and the person applying or the department chief must be a member of the NVFC. MSA provides NVFC memberships to the first 500 applicants to help departments meet the membership requirement. The application period for 2025 MSA and DuPont’s Globe Gear Giveaway will open in February 2025. A total of 52 sets of turnout gear and helmets will be awarded to increase firefighter safety. Stay tuned to the NVFC web site, Dispatch newsletter, and Facebook, X, LinkedIn, and Instagram pages, as well as the Globe Facebook page, for details.
Immersion suits are a crucial safety tool for survival in cold water, designed to protect the wearer by minimizing body heat loss. These suits are available in two types, offering either one-hour or six-hour insulation, which helps to prevent hypothermia in freezing waters. made using waterproof materials Made from waterproof materials, immersion suits cover the entire body, except for the face Made from waterproof materials, immersion suits cover the entire body, except for the face, ensuring full protection. They are also crafted from non-flammable fabrics to withstand a brief two-second fire flash and are typically bright in color for high visibility, making it easier for rescuers to spot the wearer. In emergency situations, speed is essential, which is why immersion suits are designed to be easily put on without assistance, allowing the wearer to unpack and don the suit within two minutes. This combination of features makes immersion suits an essential part of cold-water survival gear. Neoprene immersion suits Neoprene immersion suits are designed for maximum comfort and protection in cold-water survival situations. Made from a single-layer neoprene fabric, these suits integrate insulation directly into the material, offering excellent thermal protection, while ensuring flexibility and ease of movement. The snug fit, available in universal and oversize options, helps reduce water ingress, while an extended zip to the cheek ensures minimal exposure to cold water. The suit features easy-don zippers, wide anti-slip soles for better grip, and loose gloves for quick donning. Neoprene immersion suits feature airtight packaging For added convenience, neoprene immersion suits come with airtight packaging For added convenience, neoprene immersion suits come with airtight packaging and an exchange program. They are approved by SOLAS/MED, MESMER, and TC, ensuring compliance with international safety standards. These suits typically offer a service life of 3 years, with more frequent checks recommended after 10 years. PU coated nylon immersion suits, a durable upgrade PU-coated nylon immersion suits offer an advanced solution for cold-water survival, combining durability, versatility, and thermal protection. These suits are constructed with a multi-layer system, featuring a durable outer PU-coated nylon fabric and a separate insulating liner system. This two-layer design not only ensures superior insulation and long-lasting performance while allowing the liner to be replaced or upgraded to suit different needs. This customizable lining option, combined with the robust outer fabric, makes PU-coated nylon suits a more resilient and versatile choice compared to neoprene. Suits available in universal and oversize sizes These suits are available in universal and oversize sizes, with the ‘oversized’ design providing easy donning and a comfortable fit. PU-coated nylon immersion suits are supported by an exchange program for added convenience Key design features include an extended zip to the cheek to minimize water ingress, integrated suspender adjustment systems for a secure fit, and wide anti-slip soles for better traction. The loose gloves make it easier to put on the suit, while the airtight packing ensures long-term storage safety. The suits are approved by SOLAS/MED, MESMER, and TC, ensuring compliance with key safety standards. With a typical service life of 3 years, more frequent checks are recommended after 10 years to maintain optimal performance. Additionally, PU-coated nylon immersion suits are supported by an exchange program for added convenience. Neoprene vs PU coated nylon immersion suits Neoprene immersion suits Single layer system Compact fit Compliance driven Few additional features Fabrics are glued 10+ years of VIKING experience PU coated nylon immersion suits Multi-layer systems Loose fit Performance Several added and optional features Stitched and seam sealed 25+ years of VIKING experience
Dräger, an international major in the fields of medical and safety technology, is providing Tyne and Wear Fire and Rescue Service (TWFRS) with 220 self-contained breathing apparatus (SCBA) PSS Airboss® sets supported by Dräger’s FireGround accountability system to protect firefighters from the inhalation of dangerous gases during live incidents and training events. The contract was awarded following a competitive tender process, involving extensive market research, and supplier demonstrations. TWFRS’ incident response New kit depicts a step ahead in ensuring the safety and efficacy of TWFRS firefighters The SCBA sets form an essential part of TWFRS’ incident response armory and replace existing breathing apparatus systems that have come to the end of their operational life. This new equipment represents a major step forward in ensuring the safety and effectiveness of TWFRS firefighters. The new system will provide the advanced functionality and ergonomics the Service needs to meet the challenges of modern firefighting while also supporting a diverse workforce. Dräger's PSS® AirBoss Connect SCBA Dräger's PSS® AirBoss Connect SCBA was selected because of its advanced functionality, lightweight, and future-proofed, ergonomic design. Through shifting the center of gravity between the user and the set, the weight of the PSS® AirBoss is carried by the legs and pelvis, rather than the shoulders and back. This reduces the risk of strain-related injuries and fatigue when wearing the set operationally, as well as extending the time a firefighter can spend in the field because of reduced physical exertion. Dräger’s FireGround Accountability system PSS® AirBoss is adjustable to suit the physiological contrasts of men and women of age groups PSS® AirBoss is also adjustable to suit the physiological differences of men and women of varied age groups. This is paramount to being safe in operation and more comfortable to wear, as well as meeting the needs of an increasingly diverse workforce. Dräger’s FireGround Accountability system provides emergency teams with the ability to monitor, communicate and report incidents involving active users of SCBA. It provides a real-time view of all firefighters deployed at an incident, linking firefighters to its system, and relaying vital information back to the Entry Control Board. Information is also sent to FireGround’s web portal, where the user-friendly interface can be used for both live remote monitoring and post-incident analysis. Fire Service’s SCBA equipment Councillor Phil Tye, Chair of the Tyne and Wear Fire and Rescue Authority, says: "By modernizing the Fire Service’s SCBA equipment, we are reinforcing our commitment to providing first-class emergency response, in turn, protecting our communities, and safeguarding the welfare of our firefighters." He adds, "This investment provides a range of important aspects including prioritizing equality, safety, and operational effectiveness, alongside empowering all staff to perform safely and confidently. The purchase of state-of-the-art breathing apparatus sets is another example of TWFRS and the Fire Authority’s dedication to reinforce firefighter safety, operational excellence, and delivering value for money for our communities." Improvement of breathing apparatus sets Peter Heath, Chief Fire Officer for Tyne and Wear Fire and Rescue Service, says: "We are proud to be continually investing in our workforce and in particular within the area of firefighter safety." He adds, "The new breathing apparatus sets will ensure inclusivity for all our crews, and the investment reflects our strategic goals of effectiveness, efficiency, and people. The equipment is paramount for life-saving rescues when firefighters need to enter fires or other hazardous environments. As a former firefighter myself it is encouraging to see continual development and improvement of breathing apparatus sets." Benefits from the latest technology Peter Heath continues: "Dräger is one of the pioneers in its field and can deliver significant benefits to our firefighters including weight reduction that helps to ease firefighter fatigue, enhances flexibility, and supports a diverse range of body types. This will ensure that all our operational personnel can perform effectively during high-pressure incidents." Matthew Bedford, Managing Director UK & Ireland Commercial at Draeger Safety UK, said: "Dräger is delighted to be working alongside the operational teams at TWFRS. It means firefighters in Tyne and Wear will benefit from the latest technology alongside the proven track record of Dräger’s world-pioneering breathing protection equipment."
Teledyne FLIR, part of Teledyne Technologies Incorporated, announced it has been selected by Red Cat Holdings, Inc., to provide thermal imaging and Artificial Intelligence (AI) embedded software for its Black Widow™ small unmanned aircraft system (sUAS). SRR Program Red Cat was selected as the winner of the U.S. Army’s Short Range Reconnaissance (SRR) Program of Record after an evaluation process completed by the Army Project Management Office for Uncrewed Aircraft Systems, Army Maneuver Battle Lab, Army Test and Evaluation Command, and Army Operational Test Center. The U.S. Army’s current acquisition objective is for 5,880 systems, with each system consisting of two aircraft. Hadron™ 640R+ visible camera module Black Widow’s fully modular architecture enables swift adaptation to diverse mission requirements Red Cat incorporated Teledyne FLIR’s NDAA-compliant Hadron™ 640R+ longwave infrared and mega-pixel visible camera module and its Prism™ AI embedded perception software into Black Widow, a highly capable, rucksack-portable sUAS designed for operation in Electronic Warfare (EW) environments. Black Widow’s fully modular architecture enables swift adaptation to diverse mission requirements, including SSR and secondary payload operation. Dual thermal-visible imaging “We are proud to be selected by Red Cat to support the Black Widow with unparalleled tactical capabilities for the U.S. Army’s SSR Program,” said Paul Clayton, Vice President, Teledyne FLIR. Paul Clayton adds, “This collaboration provides the Black Widow with superior yet compact dual thermal-visible imaging along with AI software libraries that enable classification, object detection, and object tracking to complete the mission day or night.” Thermal imaging technology “The Hadron 640R+, with its best-in-class thermal vision, will play a key role in helping the warfighter Dominate the Night™ with the Black Widow,” said George Matus, CTO of Red Cat. George Matus adds, “We are thrilled to continue our longstanding relationship with the world pioneer in thermal imaging technology, enabling Red Cat to accelerate deployment to the U.S. DoD and its allies across the globe.” 640x512-resolution thermal camera The International Traffic in Arms Regulations (ITAR)-free Hadron 640R+ provides a 640x512-resolution thermal camera with industry-renowned thermal sensitivity and a 64-MP resolution visible camera in a size, weight, and power (SWaP) optimized package. Paired with Prism AI embedded software, the combination can enable high-precision object detection within application-specific classes, multiple object tracking, motion target indication, and more. Military+Aerospace Electronics magazine recently recognized Teledyne FLIR’s Prism digital ecosystem as a Platinum Honoree, its highest award for innovation in defense and aerospace.


Expert Commentary
Working fire doors are a prerequisite for fire safety, but what differentiates them from regular doors Kirk Smith of Allegion UK outlines the technical features that form fire-rated doors as we know them. Research indicates there may be around 42 billion doors found throughout the world’s built environment. Every day, each of those doors plays a purposeful role toward the accessibility, safety and security of buildings and their occupants-but how many people truly recognize what they are using? Building’s fire protection system Doorsets are assembled in a variety of configurations and sizes, but more often than not, they are used without a second thought. Yet, there are stark differences between regular door and fire door classifications, and where fire safety is concerned, it’s critical for users and responsible persons alike to be able to differentiate between the two. Fire doors and their hardware components are often the first line of defense against fire Despite their similar appearance, regular doors serve as interior and exterior access points only and are usually thinner at 35 mm, while fire doors aim to protect buildings and their occupants in the event of a fire and are either 44 mm or 54 mm thick depending on its fire rating. As a key element in a building’s passive fire protection system, fire doors and their hardware components are often the first line of defense against fire, and as such, require detailed engineering and testing. Author's quote Kirk Smith of Allegion UK explains: “From components and construction to features and function, there are several clear distinctions between regular doors and fire doors. Whereas regular doors are often placed throughout a building on accessibility or esthetic merit, fire doors are strategically positioned to compartmentalize areas of the structure - such as hallways and stairwells - and are designed to help direct occupants through safe escape routes while also providing them with valuable time to make their way out of the building. “When opened, fire doors provide a means of escape. And when closed, they form a barrier to stop the spread of fire and smoke. To be able to do this, the main panel of the door (also known as the door leaf) is constructed from fire-resistant materials that help to prevent the door from warping or collapsing when exposed to high temperatures." Regular doors Conversely, regular doors without these materials are highly vulnerable. Nonetheless, for a fire door to become effective, it must comprise of more than just the leaf and will include: The frame Intumescent fire - and if required for certification - smoke seals Glazing (although this is not necessary) Signage Door hardware, such as hinges, door closers, locks and latches Intumescent fire and smoke seals Fire doors must work in tandem with each of these components, so as to not compromise the integrity" “Fire doors must work in tandem with each of these components, so as to not compromise the integrity of the doorset. Intumescent fire and smoke seals, for example, frame the edges of the fire door and are chemically designed to expand into the frame when exposed to temperatures beyond 200°C." "In doing so, the seals close the gaps between the frame and the door itself, eliminating any possibility of fire - and if required, smoke - from passing through. Intumescent seals, along with clear ‘Fire Door Keep Shut’ signage - usually found toward the top edge of the door leaf - are some of the most unmistakable visual marks found on a fire door." Spring-loaded hydraulics “From an operational viewpoint, fire doors work differently than regular doors too. Fire door hardware is indispensable to fully operational door sets, where during a fire incident, an open door is rendered useless. To be able to form an effective barrier against fire, a door must close to completion from its open position, and as part of this process, it will call upon its hinges, locks, latches, and door-closing devices." "Door closers, whether concealed or surface-mounted, use spring-loaded hydraulics to effectively close and engage the door into its latch, where it is held firmly in place by the frame, whereas regular doors rely on manual control." Building’s escape routes For buildings with high footfall, an electromagnetic hold-open device may be present on a doorset “For buildings with high footfall, an electromagnetic hold-open device may be present on a doorset. These systems are permitted to keep certain fire doors open until a fire alarm is activated, aiding ease of movement until the first sign of a fire incident, in which the system will automatically release and close the doors to completion." "Equally, panic and emergency exit devices can be found on some fire doors that are positioned throughout a building’s escape routes. All exit devices are meant to be operated with minimum effort to help users successfully escape through the doorway, meaning reliability is key every step of the way.” Testing and standards To certify fire performance, the complete fire doorset is put through periods of standardized destructive testing in accredited laboratories and workshops. The standard fire performance test method complies to BS EN 1634-1, and in conjunction with product standard BS EN 16034, it provides the supply chain with manufacturing guidelines, and as a result, gives responsible persons and end users peace of mind that their doorset will function in a fire scenario. Fire doors are a legal requirement in all non-domestic properties and houses of multiple occupancy" Kirk Smith continues: “Fire doors are a legal requirement in all non-domestic properties and houses of multiple occupancy and with updated fire safety regulations now in effect, third-party testing and product traceability is as crucial as ever. Upon testing, certified fire doors are given a fire-resistance rating which details the length of time the door and its hardware components can withstand fire and smoke, with the most common FD ratings being FD30 and FD60, which declare the doorset can withstand fire for 30 or 60 minutes respectively, and FD30S and FD60S if the doors have been tested with smoke control. A regular door with no fire-resistance characteristics would not be able to withstand these tests and as such, would fail in a real-life event." UKCA and CE certifications Kirk Smith concluded: “What’s more, fire resistance tests are conducted on representative samples, and as such, components should not be substituted post-specification and installation. Fire door hardware for example, in addition to rigorous fire safety testing, must go through stages of performance testing to ensure they function properly and are able to sustain a level of durability that makes them fit for purpose. Mechanical door closers must be tested to the appropriate British Standard EN 1154, which classifies hardware over its category of use, number of test cycles, power size, fire behavior, safety and corrosion resistance. Equally, emergency exit devices and panic exit devices are tested to BS EN 179 and BS EN 1125 respectively and electromagnetic hold-open devices to BS EN 1155. A fire door’s hinges must also be tested to BS EN 1935." “For traceability purposes, end-users can review the UKCA and CE marks on a fire door and its hardware to find its fire rating, certificate numbers and the manufacturer’s details. Furthermore, for those looking to find additional information on a doorsets’ components, the Code for Construction Product Information (CCPI) can be referred to for clear, accurate and up-to-date product information - helping people to review and select trusted hardware that conforms to UKCA and CE certifications.”
With new fire safety regulations around the corner and a renewed focus on responsible persons and coordination, Karen Trigg of Allegion UK discusses the significance of fire door hardware and why regular inspections and maintenance periods must remain high on the agenda. Fire doors and their hardware are often the first line of defense in the event of a fire. Working in tandem, they coexist as a core element of a building’s passive fire protection system, providing valuable protection and time for occupants to escape by compartmentalizing the spread of smoke and fire in an emergency. Fire door’s lifecycle In the UK alone, approximately three million fire doors are purchased and installed each year. Such is their significance to fire safety, each component requires detailed engineering, third-party testing and critically, periods of ongoing inspection and maintenance. While each stage of a fire door’s lifecycle is strictly regulated, fire door checks and maintenance falls under the remit of a building’s designated responsible person and is widely understood to be an area that has fallen under neglect. Fire Safety Regulations 2022 Fire doors and their hardware play an invaluable role in the safety of our built environment As such, in January 2023, The Fire Safety (England) Regulations 2022, under Regulation 10, made it a legal requirement for all responsible persons of multi-occupied residential buildings to conduct regular fire door checks within their premises. And while it’s said that overall inspection levels are rising, with 68% of responsible persons now conducting fire door checks (or having them inspected by professionals) every month or every quarter, there’s still work to be done says Karen Trigg of Allegion UK: “In the 12-month period ending March 2023, fire and rescue services attended 178,737 fire incidents in England, a 17% increase compared with the previous 12 months. And when you consider the portion of fire door sets that remain overlooked, the numbers don’t make for good reading. Fire doors and their hardware play an invaluable role in the safety of our built environment, but there are considerable differences between a fire door that’s operating as intended and one that hasn’t been correctly specified, installed, and maintained." Regulatory Reform Order 2005 Even durable fire door hardware can become worn and tired in a high-footfall environment" Karen Trigg added: “When it comes to maintenance specifically, Article 17 of the Regulatory Reform (Fire Safety) Order 2005, states that responsible persons must ensure fire doors and their hardware are ‘subject to a suitable system of maintenance and are maintained in an efficient state, in efficient working order and in good repair’." "Even durable fire door hardware can become worn and tired in a high-footfall environment and may need repairing or replacing over time. A damaged or ineffective self-closing device, for example, can limit the closing action of a fire door and prevent it from fully closing into the frame - rendering it useless in the event of a fire." risk assessment duties Karen Trigg added: “Although we’ve seen real development towards fire safety education in recent years, we must continue to drive forward the number of responsible persons conducting organized fire door checks and maintenance periods as part of their risk assessment duties." "The introduction of updated guidance on 1st October 2023 aims to do this further, by improving the cooperation and coordination between responsible persons and rising the requirements associated with recording and sharing fire safety information during fire risk assessments. The update will also make it easier for enforcement authorities to act against non-compliance.” A stitch in time saves lives As fire safety processes tighten, building owners and facility managers shouldn’t feel discouraged in their actions. In fact, responsible persons are reminded that there’s no need to overcomplicate fire door inspections. A simple visual assessment, conducted and recorded by a competent individual, could make the difference between compliance and a fire safety disaster. Responsible persons are reminded that there’s no need to overcomplicate fire door inspections Karen Trigg continues: “For responsible persons conducting checks, the first step of fire door safety is recognizing each component of a fire door and the potential faults to look for when evaluating its condition. The British Woodworking Federation Group - in support of Fire Door Safety Week - shares regular and reliable advice on fire door safety; including a practical five-step checklist that has been designed to support responsible persons during fire door assessments. The checklist works as a visual guide and covers the five key areas of a fire door - informing users on what to look out for, including: Certification: “A label or similar marking can often be found towards the top or side of the door and will confirm the fire door is genuine and certified. All ironmongery components, including locks, latches, closers and hinges must also be UKCA/CE marked and compatible with the door leaf’s certification.” Apertures: “More often than not, fire doors are tested as solid doors and without any glazing panels or air transfer grilles. It’s important to ensure there are no apertures, holes or breaks in the surface of the door or frame. Decision makers are also reminded that altering the door will make certification void.” Gaps and seals: “Gaps around the fire door should be no greater than 3 mm, and this must remain consistent around the whole frame. Intumescent strips must also be fitted at the top and sides of the door and show no signs of wear as this may negate the door’s ability to compartmentalize smoke and fire. Additionally, check for CE or BS EN 1935 marked hinges, which must be firmly fixed and without missing screws.” Door closers: “When it comes to door closers, it’s vital to check that your door hardware is fully functioning and will close the door onto the latch from any standing position. The door must fully engage with the frame from any opening angle, and it’s recommended that users check this by letting go of the door from 75 mm through to the closed position. It’s also important to review any hold-open devices to ensure they aren’t working against the door’s self-closing devices, as fire doors must not be wedged open in any scenario.” Operation: “Testing the operation of the full door assembly is essential - from handles and closers to hinges and seals. If the door is not operating effectively, is closing incorrectly on any of its sides, or there is any doubt about hardware certification and reliability, responsible persons must identify the problem before arranging and managing professional maintenance as soon as possible. Because when it comes to fire safety, there’s simply no time to stand still.” How Allegion UK can Help Allegion UK has a wealth of resources to help professionals undertake product selection, installation, and maintenance checks on fire doors and hardware. For post-installation and maintenance support, Allegion’s simple toolkit provides information and tips on detecting potential faulty doors and poor installation, a guide to the EN classification system and a safety checklist. There’s also an option to order a free door gap tester or download Allegion’s general guide to service and maintenance for free.
As a company officer, the day will come where you and your crew are first to arrive at what looks like the beginning of a major incident. Your Battalion Chief (BC) is delayed or diverted to other incidents, so YOU are the Incident Commander (IC). How you set the table for this incident with regard to quickly setting up the Incident Command System (ICS) is critical. And how you use your channels of communication, including the ways you communicate, will be crucial to your success. Before we jump into the ‘how-to’, let’s examine something that looms over everything we do during emergencies, especially fires - ‘The NIOSH 5’. I first became aware of the NIOSH 5, when listening to one of Anthony Kastros’ lectures on incident command and the need for an organization on the fire ground. ‘The NIOSH 5’ Firefighters and emergency workers typically get lost, hurt, or killed at incidents, when any one of five causal factors identified by The National Institute of Occupational Safety and Health (NIOSH) are present: Improper risk assessment Lack of incident command Lack of accountability Inadequate communications Lack of SOPs (or failure to follow established SOPs) Statistically, 50 percent of these line-of-duty deaths (LODDs) and injury events occur in the first 15 minutes of an incident. Half of those occur in the first three minutes! If you’re the initial IC, it’s statistically likely this could happen while you’re in charge. Need for training and practice in handling emergencies Keeping ‘The NIOSH 5’ at the forefront of your mind should trigger the need for training and practice in handling emergencies. Although there are factors you simply can’t control during an emergency, you can control communications, incident command, accountability, repetitive training, and standardization. The following are some things to keep in mind while managing an incident: Arrival on Scene In incident management, setup is everything and oftentimes, determines the outcome of the incident. To use a sports analogy, you definitely want your first pitch to be a strike. So how do you do that? Provide a Solid Size-up Clear and concise on-scene conditions reports set the tone for any incident and establish solid communications The first step is taking a deep breath and giving a good size-up. Clear and concise on-scene conditions reports set the tone for any incident and establish solid communications, and a command tone. Your tone and tempo in your size-up will help focus everyone and create a tactics-driven incident, rather than an emotions-driven one. But, if we’re being honest, being cool takes practice and repetition. Your agency should have a standardized way for how and when this size-up is delivered. In many cases, it’s a fill-in-the-blank script that includes the following four things: What you see (smoke and flames/or nothing showing) The area you see it affecting (the second story, the alpha/bravo corner) What’s happening/what’s on fire or causing the hazard (a two-story home or a sedan next to a building) Establishing command (a must-take command or pass, if you’re going to rescue a citizen) By practicing within your agency’s standards, it enables you to project a cool tone over the radio like you’ve ‘been there before. Order resources early and often Tunnel vision is a death sentence for any IC. In most cases, this is not the time to get sucked into task-level problems. The exceptions to this are structure fires and other emergencies where there is an immediate and known rescue. Otherwise, it’s time to step back, take in the big picture, and make decisions as an IC. Ask yourself: ‘What will this incident do in five minutes? 10? 20? One hour?’ If the answer is ‘get bigger’, then you need more resources. Order them early and often, because they can always be turned around. Don’t try to do too much with too little. Trusted Incident Command System equals early accountability As the initial IC, you’ll be sending crews into the hazard zone. It’s a red flag if, during the initial portion of the incident, you don’t have solid accountability. It’s during this initial ‘fog of war’ that we lose track of crews, and it’s when personnel gets hurt or killed. NFPA 1561, along with other best practices, requires that you know where everyone is and what they’re doing. If you don’t have that knowledge, stop and figure that out, or assign someone to figure it out and report back to you as soon as possible. Benefits of an all-in-one digital platform - Tablet Command Many agencies require the first-arriving officer to implement some form of an ICS to track crew Many agencies require the first-arriving officer to implement some form of an ICS to track crews – a notepad, whiteboard, tactical worksheet, or better yet, a digital command board. The huge advantage of an all-in-one digital platform like Tablet Command is that it’s CAD-integrated and will populate resources for you in real-time. There’s no writing and scribbling while listening to garbled radio traffic, and no trying to ‘catch up’ with resource orders that change on the fly. Accountability integrated into command processes With a platform, such as Tablet Command, all you’re doing is dragging and dropping resources into their assignments, which automatically time-stamps their activities. Maintaining accountability becomes seamlessly integrated into your command processes. These digital platforms also tend to be highly recognizable and easy for others to assume command. It’s paramount that you train extensively on whatever system your agency uses, and that everyone in your region or agency is squared away on how to maintain accountability in a standardized fashion. It’s a problem if you have several chiefs and company officers, and too many (or not enough) ways of maintaining accountability. Many agencies need the first-arriving officer to implement an ICS to track crews Segment and subdivide How do you eat an elephant? One bite at a time. Use your knowledge of your ICS to break up the incident into manageable bites. When the Fire Chief arrives, they’ll have simple questions: Where is everybody? What are they doing? How are they doing? How do I talk to them? Knowing where your people need to deploy and what channel they’re on are critical to accountability. Using the command board is a great way to have all of those questions answered. Using divisions, groups, or sectors can make your life easier in this regard, especially as an incident grows rapidly Using divisions, groups, or sectors can make your life easier in this regard, especially as an incident grows rapidly. This is true because it ensures you’re talking to the supervisors of each segment of the emergency, especially when assessing conditions, actions and needs. Setting up an incident this way should also be an expectation that is agency-wide and practiced in scenario-based training. The terminology should be standardized so that your agency and neighboring agencies aren’t interpreting what you’re trying to accomplish in the heat of battle. Summary A clear communications plan, solid scene size-up, and early establishment of the ICS by company officers are critical to incident success. Combine this with accurate and solid accountability systems, either through analog methods or with a modern digital solution in real-time, and you guarantee safer outcomes for your crews. The best way to be prepared is through long hours of dedicated practice in the command role and, more importantly, an agency-wide understanding of what’s in the play book: Standardization! A standard approach to managing incidents will help you remedy the chaos and enable you to hand over a well-organized incident to the first-arriving Chief.
Editor's Dispatch
Information systems drive greater situational awareness when emergency responders are rushing to the scene, including access to live-911 audio feeds, video of the unfolding emergency, and/or geographic information showing the locations of fire hydrants and the best travel route to ensure the most rapid response. Information tools to manage emergency response include the locations of teams, vehicles, and personnel available in three dimensions, including locations in a multi-story building. Panasonic’s technology “First responders are thinking about getting to the scene and planning their disaster response,” says Aidan Clifford, Panasonic’s National Sales Manager. Vital information on the scene of an emergency includes video feeds, coordination with other services in the city or county, and communication with various responding agencies. Providing hardware to manage information during emergency response, Panasonic works to understand “the voice of the customer.” The company’s TOUGHBOOK ruggedized laptop computers serve the needs of fire and emergency response entities. A new Fire Advisory Council, currently being assembled, will help to guide Panasonic’s technology direction, and increase their understanding of the practical information needs of firefighters and other emergency responders. Panasonic survey Panasonic survey, 55% of respondents said access to real-time data is a top priority for their agency “The goal is to provide more information to end users more quickly,” says Marcus Claycomb, Panasonic’s Business Development Manager for the Public Sector. “Better information can save response time and enable first responders to adjust the type of response in real-time.” For example, streaming video can provide details of an unfolding emergency to firefighters as they are driving to the call. In a Panasonic survey, 55% of respondents said access to real-time information is a top priority for their agency. Useful information includes who is on the scene and where they are in real-time. Smart devices can track locations and vitals. Information goes in two directions. The ongoing deployment of 5G communications and devices will ensure information moves even faster and is more actionable. Live-911 capability Also in the Panasonic survey, 62% of respondents said computer-aided dispatch (CAD) and geographic information system (GIS) data are mission-critical. GIS data can include “layers” of information imposed on a map to show the fastest route to an incident and the locations of fire hydrants and/or accessible video cameras. Some 85% in the survey said the most important pieces of information are the location of teams, vehicles, hydrants, and/or personnel. Location and communication with drone assets are also a requirement. Live-911 capability can enable first responders to hear the dispatcher speaking with a caller in real-time. “A dispatcher can push the 911 call through the TOUGHBOOK laptop to responders on route to a call,” says Clifford. “It is an emerging technology that integrates with computer-aided dispatch (CAD) systems.” privacy of HIPAA data Device encryption and multi-factor authentication to secure the information, even ensuring the privacy of HIPAA data during an emergency medical call. Panasonic understands that fire and emergency departments need real-time information Broadly speaking, Panasonic understands that fire and emergency departments need real-time information provided by rugged devices that can withstand the daily rigors of firefighting. In the survey, 85% of respondents said rugged computer devices are important, as opposed to using consumer devices in the harsh environment of firefighters and EMS personnel. (Conducted in April 2023, the Panasonic Connect survey generated 117 responses from individuals in the fire rescue industry.) Total cost of ownership While first responders understand the importance of using ruggedized devices, purchasing decisions are not always made by those on the front lines. Sometimes it is someone else at the city or county level who decides to buy consumer-grade hardware, especially tablets, in lieu of a ruggedized laptop. Multiple problems can result, such as “battery swelling” and fire hazards if a battery overheats because of the high internal temperatures in a vehicle. Consumer devices are not designed to operate in temperatures above 100°F. Cost is the main reason to opt for less expensive consumer-grade equipment, but the lower cost is an illusion. The math is very different if one considers the total cost of ownership (TCO), including any downtime resulting from a battery charge not lasting the entire shift, for example. Panasonic's TOUGHBOOK laptops First responders should work to ensure their voices are heard as purchasing decisions are made Ruggedized equipment is more resistant to being dropped. Panasonic's TOUGHBOOK laptops meet the MIL-STD-810H specification and ingress protection (IP) standards, IP65 and IP66, which test for ruggedness and resistance to solids and liquids. Additional features include enhanced connectivity and embedded antenna, non-breakable components, and all-day batteries. First responders should work to ensure their voices are heard as purchasing decisions are made. They should have a conversation with command-level employees and throughout the fire service to ensure equipment purchasing reflects the real needs on the front lines, says Claycomb. What's Ahead? What’s ahead for information technology on the front lines of firefighting? “There is an incredible opportunity ahead to integrate the TOUGHBOOK with fire vehicles,” says Marcus. He adds, “And the potential of using 5G will be limited only by our own creativity. Looking ahead, we can expect more artificial intelligence (AI), augmented reality (AR), and an incredible amount of data.”
Chemicals broadly labeled as PFAs provide important properties to turnout gear used by firefighters, including better resistance to heat, water, and other hazards. Unfortunately, human exposure to per- and poly-fluoroalkyl substances (PFAs) has also been linked to heightened cancer risk. Research on the concentration of PFAs The U.S. National Defense Authorization Act of 2021 directed the National Institute of Standards and Technology (NIST) to identify the prevalence and concentration of PFAs in the personal protective equipment worn by firefighters. The resulting research has identified the presence of PFAs in 20 textiles used to make the various layers of a firefighter’s turnout gear. PFAs The water- and oil-resistant properties of PFAs have made them ubiquitous components in products The water- and oil-resistant properties of PFAs have made them ubiquitous components in manufactured products, including textiles used in firefighter apparel. PFAs have found their way into the bodies of most Americans, and research has shown higher PFA concentrations in the blood among firefighters. However, there are numerous potential pathways to exposure, including fire scenes, aqueous film-forming foams, food grown at fire stations, ambient dust, as well as firefighter turnout gear. Health effects The health effects of PFA exposure are the subject of extensive ongoing research. For example, cancer incidence data are available for only a subset of known PFAs. PFAs do not break down easily and persist in the human body and the environment, thus earning the name “forever chemicals.” Further research continues what kinds and levels of PFAs are dangerous and how the chemicals find their way into the body. Presence in turnout gears PSAs potentially could be present in any one of the three layers of turnout gear, the outer shell, the moisture barrier, and the thermal liner. All three layers must conform to National Fire Protection Association (NFPA) requirements to resist heat, water, and other hazards. Research findings NIST researchers targeted 53 PFAs used to fabricate 20 textiles used in various layers of turnout gear NIST researchers targeted 53 PFAs used to fabricate 20 textiles used in various layers of turnout gear. They identified and quantified concentrations of 26 different PFAs. Researchers found the least amount of PFAs in the fabric layer closest to a firefighter’s skin, the thermal lining; water repellency is a lower priority for this layer than the other two. In contrast, the moisture barrier and the outer shell contained PFA concentrations up to 400 times higher, although the numbers varied from fabric to fabric. update turnout equipment standards Changing to a non-PFA water-repellant coating on the outer layer could essentially eliminate PFAs from that layer. Since the thermal liner already has low PFA content, that leaves only the moisture barrier layer to address. However, researchers caution about the possibility of swapping one risk for another. Information gleaned from NIST research could be used to update turnout equipment standards and give firefighters more confidence in the safety of the equipment. wear and tear Another factor to consider is the impact of wear and tear on how many PFAs escape from turnout gear. Factors include UV exposure, heat, and laundering, which have a measurable impact on PFAs in turnout gear. NIST efforts currently underway will use high-resolution mass spectrometry to identify a broader swath of PFAs than the 53 compounds already quantified, including screening for previously identified compounds as well as searching for novel PFAs. PFA exposure Future research will study fire scenes, fire stations, and other occupational environments where firefighters work in Future work will also evaluate the type and amount of PFAs released from firefighter gear textiles upon exposure to simulated sweat. Other routes to PFA exposure among firefighters are also being targeted by NIST research, including hoods, gloves, and wildland gear. Additionally, future research will study fire scenes, fire stations, and other occupational environments that firefighters' work in. Risk of cancer Firefighting is a dangerous profession, and firefighters are at higher risk of a variety of cancers compared to the general population. According to the National Institute for Occupational Safety and Health (NIOSH), cancer is a leading cause of death among firefighters. Firefighters face a 9 percent increase in cancer diagnoses, and a 14 percent increase in cancer-related deaths, compared to the general population in the U.S. Exposure to toxic combustion products How the exposure of PFAs ranks among those risks is debatable. Firefighters can be exposed to many known and suspected carcinogens through their work Firefighters can be exposed to many known and suspected carcinogens through their work. All types of fires create a mixture of toxic combustion products including liquids, gases, and particulate matter. Firefighter protective equipment containing suspected carcinogens is just part of the bigger picture. adverse health risks In August 2022, the International Association of Fire Fighters and the Metropolitan Fire Chiefs Association joined forces to alert members to the adverse health risks posed by PFAs in turnout gear, to draw attention to the need for PFAs-free turnout gear, and to recommend precautionary steps for members and departments until next-generation gear can be developed and put in use. In January 2023, the IAFF announced it had retained three nationally recognized tort law firms to assist the union in its effort to end firefighter cancer and remove PFAs from use in the fire service.
Not so long ago, there was a time when a dirty helmet symbolized firefighter bravado. A dirty helmet was seen as a testament to how hard a firefighter worked and the horrible conditions he or she withstood when completing their duties. Sometimes, there was even concern that washing and cleaning a helmet would somehow reduce the likelihood of catching another fire in the near future. A dirty helmet no longer necessarily shows anything about a firefighter's competency or dedication to their job. While a dirty helmet may be a sign that a firefighter has been on many calls and has experience, it is also a potential health hazard due to the accumulation of harmful bacteria and carcinogenic substances on the interior of the helmet. Therefore, a clean helmet is considered a sign of professionalism and attention to detail in the firefighting community. Polycyclic aromatic hydrocarbons Dirty helmets can increase the risk of cancer for firefighters due to the accumulation of carcinogenic substances and chemicals on the interior of the helmet. Firefighters are exposed to a range of toxic and carcinogenic substances when they respond to fires, including benzene, formaldehyde, and polycyclic aromatic hydrocarbons (PAHs). Choosing safety and health over displaying an ego-driven trophy is not always easy These substances can adhere to the helmet's interior, making it a potential source of exposure even after the fire has been extinguished. Prolonged exposure to these substances increases the risk of cancer, particularly for firefighters who have been on the job for many years. Choosing safety and health over displaying an ego-driven trophy is not always easy. The origins of dirty helmet syndrome can be traced back to the early days of helmet usage. As people began to recognize the importance of wearing helmets for safety, concerns about the hygiene of helmets also arose. Specialized cleaning solutions Efforts are made to combat dirty helmet syndrome through the use of antimicrobial materials, regular cleaning, and education about the risks associated with wearing dirty helmets. Firefighters take their safety and health seriously and understand the importance of keeping their equipment clean and well-maintained. Regular cleaning of helmets and other firefighting equipment can help reduce the risk of exposure to carcinogens. Firefighters are also encouraged to follow proper safety procedures and wear personal protective equipment (PPE) to minimize their exposure to hazardous substances. Fire departments now use specialized cleaning solutions and equipment to decontaminate gear and reduce the risk of cancer for firefighters. Dangers of dirty helmets There are several ways to educate firefighters about the dangers of dirty helmets: Training: Include information about the risks of dirty helmets and how to properly clean and maintain them in firefighter training programs. Workshops and Seminars: Conduct workshops and seminars on the hazards of exposure to carcinogens and the importance of keeping firefighting equipment clean, including helmets. Resources: Provide firefighters with access to resources such as articles, videos, and brochures that highlight the risks of dirty helmets and how to clean them. Role Models: Highlight the practices of experienced firefighters who keep their helmets clean and well-maintained as role models. Policies: Develop and enforce policies and procedures for cleaning and maintaining firefighting equipment, including helmets. Policies ensure best practices are employed dependably rather than merely suggested. Complaints and discipline are needed to ensure clean gear. Equipment: Provide firefighters with access to specialized cleaning solutions and equipment to decontaminate gear and reduce the risk of cancer. Some departments provide personnel with two helmets so that there is always one available if the second one is being cleaned properly. Wearing firefighting gear Overall, a combination of training, resources, policies, and equipment can help educate firefighters about the dangers of dirty helmets and promote the importance of keeping their equipment clean and well-maintained. The culture a department promotes is a driving force of how firefighters act. Accountability ensures compliance. In summary, wearing firefighting gear thickly layered with carcinogens and dangerous toxins is uncool. Organized methods for safety, from firefighting techniques to gear decontamination, are essential and are now valued and expected.
Case studies
Dräger, an international pioneer in the fields of medical and safety technology, has supported the City of Derry Airport in modernizing its suite of personal protection equipment (PPE) and protocols to safeguard its specialist Fire and Rescue Service (FRS) from incident-based safety risk and the risks posed by carcinogens to which they are often exposed. The City of Derry Airport is northwest Ireland’s largest airport which, at its pre-pandemic peak, provided over 200,000 passenger flights to the UK and southern Europe. The airport’s fire service provides aircraft safeguarding and an emergency response service for terminal buildings and low-traffic collisions on-site. Fire services across the UK Modern plastics and polymers found in buildings and airplanes as they burn release carcinogens The modern plastics and polymers found in buildings and airplanes as they burn release carcinogens and expose firefighters to a risk of cancer that is some two to four times higher than the general population, and could potentially shorten their life span by up to 20 years. Accordingly, as safety regulations tighten, fire services across the UK, including the City of Derry Airport, are upgrading their equipment and procedures to protect their crews and reduce cancer mortality rates. Dräger’s HPS® Safeguard helmet The Derry management team assessed many different products to protect their employees. They chose Dräger’s HPS® Safeguard helmet, for example, because it was extremely fast and easy to use compared to the existing equipment, especially when firefighters also needed respiratory protection equipment. The padded 3-point harness with versatile chin and neck straps, coupled with an adjustment wheel placed on the back of the helmet allowed for a safe and easy fit to any head shape or size and can accommodate users who observed cultural or religious practices. Dräger’s PSS® AirBoss The helmet’s innovative design is such that various external devices can be affixed to it with ease The helmet’s innovative design is such that various external devices can be affixed to it with ease and enables the hands-free operation of thermal imaging cameras, action cams, and lamps if required. The team will also be introducing Dräger’s PSS® AirBoss self-contained breathing apparatus to its fire crews in the near future to prevent inhalation of carcinogenic particulates. With its lightweight and best-in-class ergonomics, it will also significantly reduce the physical strain on individuals during a shout. HPS® Safeguard helmet Both the HPS® Safeguard helmet and the PSS® AirBoss are suitable for manual and machine washing. They are made with low-absorbent and liquid-repellent materials which take on fewer contaminants. The AirBoss also has a streamlined design to minimize dirt traps. All of this makes regular cleaning and decontamination of PPE required by current regulations extremely easy. Special holders and bags must be used to carry them to designated ‘dirty’ or decontamination areas Best practices in firefighting are rapidly evolving in response to the latest understanding of cancer mortality and its causes. It is now understood that cancer-causing particles remain in the fibers of PPE and can contaminate other surfaces or people long after an incident takes place. All PPE must be transported back to the workshop on the outside of an appliance to avoid contaminating the interior cab. Special holders and bags must be used to carry them to designated ‘dirty’ or decontamination areas to prevent transferring carcinogens to ‘clean’ kitchens, sleeping areas, or other parts of the station. Dräger’s TotalCare Agreement The products will be covered by Dräger’s TotalCare Agreement, which means the crew and its equipment will benefit from maintenance, inspection, and preventive care. Gerard McCloskey, Safety and Fire Officer at Derry Airport, says that providing routinely changeable service parts and kits is a significant advantage: “The spares facility will guarantee equipment uptime, and fill short-term gaps should the need arise,” he explains. The TotalCare service includes engineer callouts, routine checks and calibrations, and advice on equipment best practice. Health and safety service standards Elizabeth Millward, Marketing Manager at Draeger Safety UK, says protecting from harm in the unique environment posed by the airport is no easy task: “Firefighters must be protected and the progressive approach that the City of Derry Airport is taking towards meeting the new health and safety service standards is particularly impressive." “Alongside our new equipment and Total Care service, many crews are also implementing mechanical cleaning solutions, which can provide further protection from carcinogenic risk. As always, we are committed to providing ‘technology for life’ and helping forward-thinking services combat the dangers that fire and rescue operations may pose.”
Blackline GPS is a Calgary-based wireless technology company that provides products for worker safety monitoring, covert surveillance, and business applications such as vehicle and logistics tracking. Blackline’s proprietary location-aware hardware, coupled with easy-to-use web and mobile interfaces, allows organizations to keep workers safe and track important assets. Blackline’s main product is the Loner® safety monitoring device, worn by employees working out of sight and sound of others or in dangerous environments. Loner automatically detects if an employee has fallen or is motionless for a period of time, indicating they may have suffered an injury, health incident, or physical threat. Loner devices pinpoint the person’s exact location on an interactive, clickable map so emergency personnel can respond quickly. Challenges The Lone Safety device allows employees to call for help by pulling an emergency latch during emergency situations Blackline’s main goal is 100% employee safety. The company’s Loner safety monitoring device is worn by thousands of workers across diverse industries, including oil & gas, utilities, manufacturing, construction, and natural resources. Loner automatically detects if a person has fallen, is motionless, or has not responded to a regular ‘check-in’, but it also allows employees to call for help by pulling an emergency latch during emergency situations. For example, if a field service technician is accidentally blasted by pressurized gas and becomes unconscious, the employee’s Loner device would detect the fall and lack of movement, and notify safety monitoring personnel automatically, in seconds. Real-time application All alerts are automatically communicated in real time via a cellular or satellite connection to Blackline’s main safety monitoring infrastructure. Monitoring personnel, either in-house at an employer or through Blackline’s Loner 24/7 central monitoring service, see the safety alerts on an interactive, clickable Google Maps and then attempt to reach the employee to validate the situation. Because monitoring personnel can visualize exactly where an alert has originated, they can direct nearby coworkers or emergency responders to the employee’s precise location when required. Because every minute counts in emergency situations, interactive, highly visual maps are a core component of Blackline’s Loner platform. Blackline not only wanted to pinpoint each employee’s location on a map but also to provide rich visual details about the location, such as zoomable street and satellite views. Solution Blackline chose to work with Google Maps Engine to integrate the most accurate, real-time maps for into its platform. Google Maps Engine interfaces directly with BlackLine’s web and mobile app, allowing customers to interact with the maps via any device. Blackline's location beacons on installation provide precise positioning of employees where GPS does not reach “Since all the data is stored in the cloud with Google Maps, our customers can click on and zoom in on maps in real-time from desktop or mobile devices,” said Brendon Cook, CTO of Blackline. "With Google Street View and Satellite View, Blackline customers get a clear view of the terrain where each worker is located, spotting buildings, roads, and other landmarks that might help responders find an employee more quickly in an emergency,” said Cook. Blackline app Full integration of Google Maps Engine with the Blackline app allows customers to easily layer their own data on top of the maps, adding employee names, locations, roles, territories, and tasks. That way, when customers monitor employees on the map, they get a quick visual snapshot of what each employee is doing, where, and why. Blackline also layers other critical data onto the maps, including information on the battery power and signal strength of each device, as well as the location of nearby employees. Inside buildings, Blackline provides ‘location beacons’ that can be installed to provide precise positioning of employees where GPS does not reach. Soon, customers will be able to upload their interior building floorplans into the Loner safety monitoring app so they appear on the Google Maps interface, achieving full situational awareness to keep employees safe even when working indoors. Results As part of the Loner safety monitoring platform, Google Maps can quite literally help save lives. AltaGas Utilities Inc. issues Blackline Loner devices to field operations workers. Every worker who works ‘alone’, from meter readers to technicians, carries a Loner device. AltaGas Utilities Inc. deployedthe devices three years ago, and currently has 146 in use. Dave Koopman, Manager, Environment, Occupational Health and Safety at AltaGas Utilities Inc., says the visibility provided by Google Maps within the Loner safety monitoring application is critical when it comes to keeping workers safe. Authority comments One can even visualize where the closest fire and police departments are located for the worker in potential distress “If the Loner device sends out an alert for any reason, our team is immediately notified via text message and email, and those messages contain a clickable Google Map and URL,” says Koopman. “Wherever I am, whatever device I’m using, I can just click the link to see a map with a green dot on the exact longitude and latitude of the individual’s location.” Though AltaGas Utilities has, thankfully, yet to receive an alert for a life-threatening emergency, Koopman says they are fully prepared to respond if they do. “With Blackline and Google Maps, we can not only see with precision where a person is located but can zoom in on Google Maps street view to get visibility into surrounding landmarks and buildings, so we can tell emergency responders where to go and what they might encounter when they arrive,” says Koopman. “We can even visualize where the closest fire and police departments are located in relation to the worker in potential distress.”
Comelit-PAC has been working with partners - GB Integrated Systems to fit the latest fire safety systems at the Hop House in Deva City Office Park, in order to ensure the safety of all who work and visit the unique work environment. Part of the former Threlfalls Brewery, an iconic feature of the Manchester city skyline, Deva City Office Park presents an eclectic mix of business space presented in a Grade II listed Brewery building or 17 high-spec self-contained office units. Balancing modern design GB Integrated System worked directly with the site management team to upgrade the addressable panels With the need to offer 24 / 7 security and fire safety, GB Integrated System worked directly with the site management team to upgrade the addressable panels, and specified Comelit-PAC’s latest LogiFire solution. Iain Taylor, Director of Asset Management at Northwood Investors International Limited, said: “We knew we had complex requirements for Deva City when it came to security and fire safety, with each individual business on site needing its own risk assessments. This was set against the buildings themselves, where any upgrades had to be sympathetic to the specific interest Grade II classification and balance modern design and use of technology.” Easy fire safety solution Iain Taylor adds, “GB Integrated Systems made it a priority to understand this and work with us right from initial design and specification to implement a bespoke solution that could accommodate our requirements. From a fire safety perspective, Comelit-PAC was recommended, to ensure we could reduce installation time and minimize disruption to business activity for the benefit of our occupiers.” GB Integrated System specified Comelit-PAC’s LogiFire Easy fire safety solution. The office park required a stand-alone 1-loop analog addressable panel. Fire safety solution We recommended Comelit-PAC’s Logifire solution essentially because of its simple design" Mike Gray, Technical Director at GB Integrated Systems, stated: “We recommended Comelit-PAC’s Logifire solution essentially because of its simple design, and ability to easily install using existing cabling, so as not to interfere with the style of the development and its unique character. From the owner’s perspective, its style and flexibility of use means that it is the best fire safety solution to protect the occupiers collectively and blend seamlessly with its surroundings.” Logifire addressable system, has been designed to offer a simple to install, fire safety solution that is compliant with BS and EN standards. It is complemented with a range of detectors, offered with award-winning designs to ensure systems blend with their surroundings. Mind fire safety Mandy Bowden, Comelit-PAC Fire Manager, concluded: “When it comes to fire safety, the market is growing rapidly amid greater awareness of the need for risk assessments, remediation work, building upgrades and ongoing maintenance in the new-build sector as well as at existing sites. What our work with GB Integrated Systems at Deva City Office Park demonstrates is the need to assess each development as early as possible in a works program to ensure solutions meet exact requirements." She adds, "We understood that any upgrade had to be carefully considered with regards to how it will impact on the aesthetics of the overall premises. Together, we identified how LogiFire as a single solution, could be installed quickly and effectively for the benefit of all who work on-site. It allows for total peace of mind fire safety.”
Oshkosh Airport Products, a division of Pierce Manufacturing Inc., a subsidiary of Oshkosh Corporation announces Airservices Australia has issued a purchase order for four Oshkosh Airport Products Striker® Volterra™ 6x6 Aircraft Rescue and Fire Fighting (ARFF) hybrid electric vehicles. These environmentally advanced fire apparatus will be deployed at the new Western Sydney International Airport (WSI), set to open in 2026. Striker Volterra 6x6 The Striker Volterra 6x6 comes equipped with an Oshkosh-patented hybrid-electric drivetrain, featuring an electro-mechanical infinitely variable transmission. This enables zero-emissions operation through the integrated onboard batteries and uninterrupted power supply by coupling with the internal combustion engine for pumping and drive systems. innovative design Airservices Australia is making a significant investment to support the development of an 'airport of the future' WSI is a transformational infrastructure project expected to boost economic activity, provide local employment opportunities, meet Sydney's carbon-neutral sustainability initiatives, and meet the area’s growing aviation needs. Airservices Australia is a government entity making a significant investment to support the development of an 'airport of the future', featuring world-pioneering technology, innovative design, and a sustainability plan incorporating assets like the Striker Volterra ARFF hybrid electric vehicles. sustainability "As the first airport built in Australia in over 50 years, WSI is not just an airport; it's a statement of intent for a more sustainable future,” said Dave Archer, Vice President of Engineering for Oshkosh Vocational. He adds, “The Striker Volterra vehicles, with their hybrid electric technology, align perfectly with Airservices Australia and WSI’s goals. These vehicles are not only an asset to emergency response capabilities but also play a crucial role in larger environmental sustainability initiatives." environmentally conscious choice Dave Archer continues, "They symbolize a dedication to intelligent design, energy optimization, fire crew safety and efficiency, and ultimately, a carbon-neutral future." Striker Volterra ARFF hybrid electric vehicles demonstrate the most advanced acceleration and reduced fuel consumption compared to our standard diesel models, making them an environmentally conscious choice for emergency response services. Striker Volterra features Striker Volterra ARFF demonstrates a 28 percent improved acceleration compared to the standard diesel models WSI’s four new Striker Volterra 6x6 vehicles will feature an industry-pioneering modular cab design, TAK-4® all-wheel independent suspension, and a 50’ Snozzle® High Reach Extendable Turret. They each house an 11,356-liter (3,000-gallon) water tank, a 1,590-liter (420-gallon) foam tank, and a 7,570 lpm (2,000 gpm) water pump, along with a 250 kg (550 lb.) dry chemical powder system. Accelerating from 0 to 80 kph (0 to 50 mph) in under 25 seconds, the Striker Volterra ARFF demonstrates a 28 percent improved acceleration compared to the standard diesel models when fully loaded. training, implementation, and service support Dave Archer said, “The collaboration between Oshkosh Airport Products and Airservices Australia marks a significant step forward in the aviation industry's commitment to sustainability." He adds, "We remain committed to a strong partnership, providing world-class training, seamless implementation, and unwavering service support to ensure these vehicles exceed expectations in the critical missions of ARFF crews.” By leveraging new technologies and innovations like Oshkosh Airport Products’ Striker Volterra ARFF hybrid electric vehicles, WSI will showcase the feasibility of low-carbon operations and set a new standard for airports worldwide.
Firefighting is an extremely dangerous and demanding profession, both physically and mentally. However, help is at hand: Teledyne FLIR designed its K-series of professional yet affordable thermal imaging cameras to take the strain, assisting firefighters in navigating through smoky conditions while searching for hot spots and measuring temperature from a distance. The team at Solna Fire Station in Stockholm, Sweden, is a case in point, where the use of a FLIR K-series camera recently helped one of the team’s smoke divers save four lives in a city center fire. Greater Stockholm’s Fire Service Storstockholms brandförsvar (Greater Stockholm’s fire service), covers 10 municipalities in the city, including Solna, located just north of the center. When a recent large fire began downtown, Solna’s fire crew responded to the call. “We sent in two smoke divers, both with FLIR K-series cameras,” explains Tomas Bellander, a Firefighter and Instructor at Solna Fire Station with 22 years of experience. FLIR Thermal Camera Upon approach, his FLIR thermal camera showed what looked like an arm in the doorway" Tomas Bellander continues, “One smoke diver spotted an elevator with its doors slightly open. His instinct drew him towards the elevator and, upon approach, his FLIR thermal camera showed what looked like an arm in the doorway." He adds, "It turned out there were four people in that elevator, all of whom were saved by our smoke diver and his FLIR camera.” Smoke Diving Like any fire station, Solna has a range of conventional firefighting tools at its disposal but relies on FLIR thermal imaging cameras to locate fires and pinpoint anyone trapped or in need of assistance. However, while the main application for FLIR cameras at Solna Fire Station is smoke diving, the crew also uses its cameras as part of other rescue activities, such as locating people on train tracks or next to the water. FLIR K55 High-Performance “It’s a lot easier than using our own eyes and a flashlight,” says Firefighter - Simon Zettergren, adding “We can quickly see if there are any temperature shifts to detect human presence.” Zettergren says Solna Fire Station takes advantage of FLIR K55 high-performance thermal cameras, retaining two in each vehicle. Charging takes place inside the truck. “We typically deploy teams of two smoke divers: one with a hose and the other with a FLIR K55,” he explains. Easy Smoke Detection They display crisp thermal images on a bright LCD, helping Solna’s fire crew to navigate better FLIR K55 cameras allow Solna Fire Station to attack fires with a better strategy, maneuver through smoke more easily and save lives. They display crisp thermal images on a bright LCD, helping Solna’s fire crew to navigate better and expedite critical decisions. “A lot of thoughts go through your head when there’s a real fire,” says Tomas Bellander. Situational Awareness With Limited Visibility He adds, “You have to execute your strategy while simultaneously receiving commands from the lieutenant and making real-time judgments about situational awareness with limited visibility." Tomas Bellander concludes, "The stress factor is high, so you must call upon your equipment and training. If you can do that, the outcome will likely be positive.”
West Yorkshire Fire & Rescue Service (WYFRS) has selected edge control room solutions from Frequentis to enhance service delivery for the communities it safeguards through better resource allocation and coordination between emergency services when responding to emergencies. WYFRS WYFRS is the fourth largest fire and rescue service in the country, responsible for the safety of over 2.2 million residents and the protection of 800 square miles of land, covering five major metropolitan districts. The diverse landscape, which encompasses everything from vast rural countryside to towns and major cities, presents unique challenges: Frequentis' expertise in providing comprehensive control room solutions and dedication to delivering innovative technology to emergency service organizations has played a vital role in this successful collaboration. Efficiency, Communication And Resource Allocation We are aiming to enhance the efficiency of our emergency response even further, and improve communication" “By implementing the Frequentis systems, we are aiming to enhance the efficiency of our emergency response even further, improve communication and coordination among emergency responders, and optimize our resource allocation,” says WYFRS Area Manager, Scott Donegan. He adds, "Ultimately, this will enable us to be even better at protecting the millions of residents, the communities, and businesses we serve here in West Yorkshire." Cloud-Based Mobilizing Solution The contract marks a significant milestone in West Yorkshire Fire & Rescue Service's journey toward modernizing its control room capabilities. “By adopting the Frequentis Microsoft Azure cloud-based mobilizing solution, West Yorkshire Fire & Rescue Service will benefit from a comprehensive communication and incident management platform, LifeX, and unique-mobilization solution provided by our recent acquisition, Regola," says Andy Madge, Managing Director of Frequentis UK & Ireland. A System-As-A-Service Approach We continue to provide modern control room solutions for safety-critical customers" Andy Madge adds, "The 'System as a Service' approach aligns with the managed service requirements, eliminating conventional concerns and costs associated with ongoing IT management and security." He continues, “This partnering approach represents a significant step forward for Frequentis as we continue to provide modern control room solutions for safety-critical customers.” Computer-Aided Dispatch (CAD) system The new systems include a replacement Computer Aided Dispatch (CAD) system that is Emergency Services Network (ESN) ready, an Integrated Communication and Control System (ICCS) for seamless telecommunications, radio communications, and data communications, as well as a mobilizing system for efficient resource allocation to incidents. The implementation of these cutting-edge systems will enable WYFRS to respond even more effectively to emergency calls, whether the resources are mobile or stationed at various premises, and the mobilizing system will streamline the assignment of resources and personnel.


Round table discussion
Technology has played a role in firefighting since the beginning; in fact, portable water pumps were found among the ruins of ancient Egypt. As bucket brigades gave way to electric pumps and internal combustion motors displaced horse-drawn fire engines, firefighting has benefited in terms of greater efficiency and lives saved at each point along the way. Technologies boosting the efforts of firefighters include drones, robots and other high-tech innovations. We asked our Expert Panel Roundtable: Which technologies will we see in ‘the future of firefighting'?
Thermal imaging is an advantageous tool for firefighters on the frontline. As thermal cameras have become more compact and affordable, their availability has expanded, along with their usefulness. We asked our Expert Panel Roundtable: How does thermal imaging serve the needs of firefighters and how is it changing?
Ensuring the health and wellness of firefighters is a burden shared among equipment manufacturers as well as the fire departments and individual firefighters. Thoughtful design of equipment and other products used in the fire service can be a positive factor as firefighters and other first responders face dangerous situations every day. We asked our Expert Panel Roundtable: What steps can we take to better ensure firefighter health and wellness?
Products


Videos
Personal Protective Equipment (PPE): Manufacturers & Suppliers
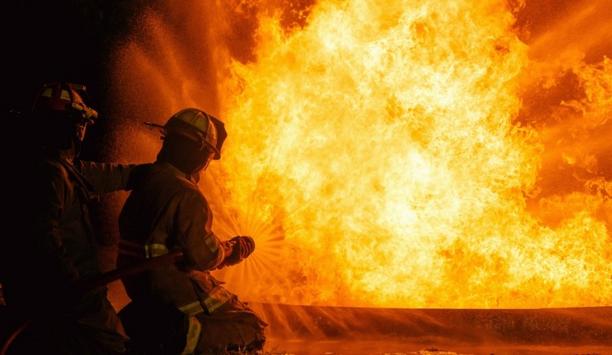
The New Future For Fire Agencies
Download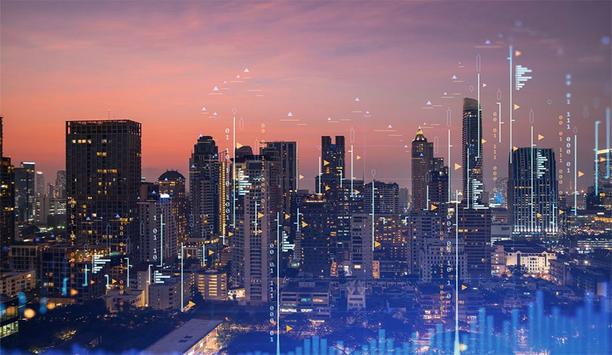
The Eight Key Trends in Fire Detection in 2023
Download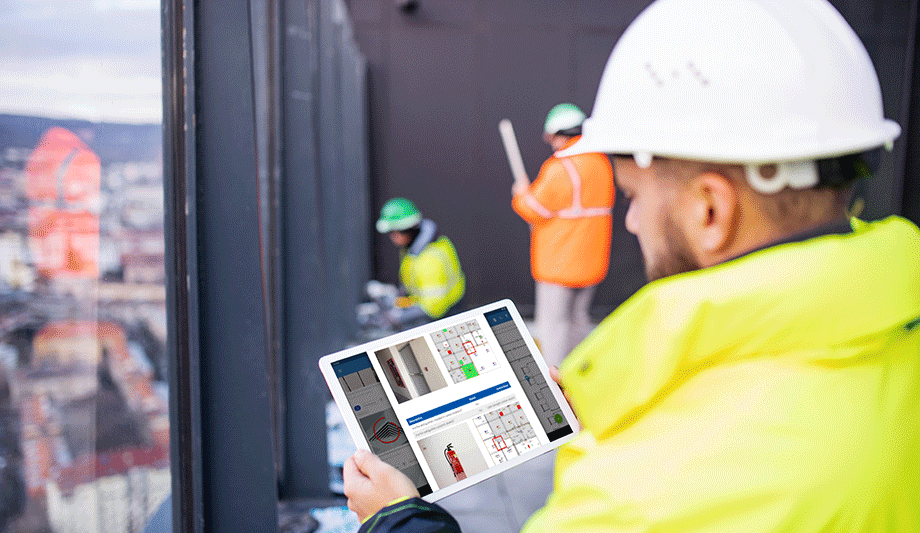
A Digital Platform to Improve Fire Safety Compliance and Inspections
Download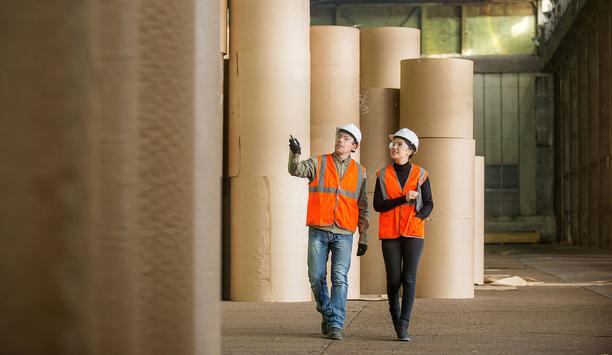
Overcoming the Challenges of Fire Safety in the Paper Industry
Download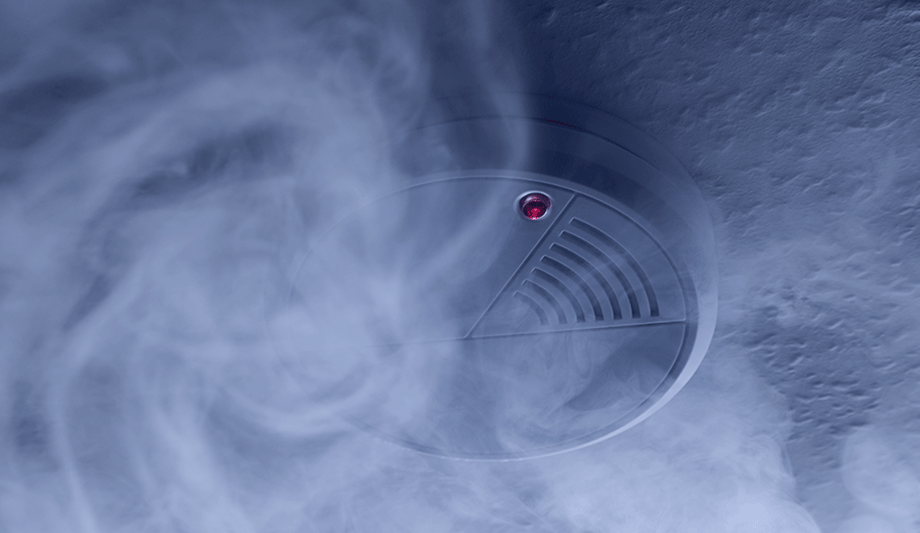
Carbon Monoxide: Creeping Killer Caught In The Act
Download