Flammable Material Control
Renewable hydrogen is set to play a crucial role in the energy transition. European member states are already experimenting with this promising energy carrier, and they are testing how they can repurpose existing natural gas distribution networks to bring hydrogen to the consumer. Hydrogen is a highly flammable gas. That is why technical staff working on these hydrogen distribution networks will need to be trained for safety. They will also need to be equipped with the right tools to detect hy...
The devastating fire damage caused to the cathedral of Notre Dame earlier this week provided a dramatic visual illustration of the effect that a fire may have on a heritage building. Although it is too early to speculate on the cause of the fire at Notre Dame, it can be seen as an appropriate moment for the Fire Sector internationally to reflect on the management of heritage buildings in relation to fire risk management. How vulnerable these buildings can be is crucial Heritage buildings can...
Lithium-ion batteries are at the heart of modern technology, powering everything from mobile devices to electric vehicles. However, they come with a significant fire risk. The newly released Collaborative Reporting for Safer Structures (CROSS) paper delves into the fire safety concerns associated with these batteries, shedding light on the phenomenon known as thermal runaway. This self-sustaining reaction can trigger large-scale fires or even explosions, often set off by overcharging, short cir...
According to the National Fire Incident Reporting System, there were 16,500 workplace fires in 2020, many of which were caused by cooking incidents, overloaded electrical sockets, and unattended heating devices. How could these fires have been prevented? With proper fire safety systems and training in place. If they want to prevent fires in the workplace, safeguarding the lives of the employees and customers, they’re here to help. Follow along as they discuss common fire hazards in the wo...
Immersion suits are a crucial safety tool for survival in cold water, designed to protect the wearer by minimizing body heat loss. These suits are available in two types, offering either one-hour or six-hour insulation, which helps to prevent hypothermia in freezing waters. made using waterproof materials Made from waterproof materials, immersion suits cover the entire body, except for the face Made from waterproof materials, immersion suits cover the entire body, except for the face, ensuri...
The fire safety landscape has experienced significant change in recent years. Some high-profile incidents, including those in Catford and Dagenham, highlight the critical importance of using fire-resistant materials and implementing enhanced safety measures for both residential and commercial structures. These tragic incidents have prompted the construction industry to rethink how it designs and builds safe spaces for people to live and work in. In fact, the latest revision to the Fire Safety S...
News
In the run-up to the festive period, the Local Government Association (LGA) and the National Fire Chiefs Council (NFCC) are reminding people of precautions that can be taken at home to prevent a fire, as government figures show a heightened risk of fire around this time of year. The number of fire hazards in the home can dramatically increase as people celebrate and exchange gifts due to festive lights and decorations, candles and open flames, as well as potentially faulty products such as toys or chargers and devices. Risk of fire in homes The free online tool allows people to get tailored tips and advice to reduce the risk of fire only by replying to a queries Analysis of Home Office figures from the last 10 years by NFCC shows that fire risk in England is higher in December. People are 53 percent more likely to have a fire on Christmas Day than they are on an average day in the year along with a 10 percent uplift in risk of an accidental home fire occurring in December than in any other month of the year. To help reduce the risk of fire in homes NFCC encourages people to complete an Online Home Fire Safety Check (OHFSC) for themselves or their loved ones. The free online tool allows people to get tailored tips and advice to reduce the risk of fire simply by answering a few questions. Festive fire safety advice Festive fire safety advice includes not overloading sockets, making sure any Christmas lights are not damaged, and keeping candles away from flammable materials like decorations and curtains. Festive lights should always be switched off at night or while properties are empty. Statistics show that most fires in the home start in the kitchen while cooking, so it’s important to stay focused. Electrical fires can also pose a higher risk at Christmas. requirement of UK product safety regulations People are reminded to check that any electrical appliances, including toys and devices People are reminded to check that any electrical appliances, including toys and devices, bought as gifts are from reputable sellers and that CE or UKCA marks are visible, which is a requirement of UK product safety regulations. Products bought from third-party sellers on online marketplaces or auction sites may not necessarily have the same level of regulation as trusted high-street retailers. With e-bikes, e-bike conversion kits and e-scooters being one of the latest must-haves, checks should be made that they also meet UK safety regulations. Charging e-bikes and e-scooters People are also being urged to be cautious when charging e-bikes and e-scooters with a reminder that they should never be stored or charged in hallways or other escape routes. NFCC is also advising all homeowners to have at least one smoke alarm on every level of their property and all homes to test that they are all working as a matter of routine. It is also a legal requirement that landlords provide smoke alarms in rental properties, and renters should ensure these are tested regularly. Online Home Fire Safety Check NFCC is also advising all homeowners to have at least one smoke alarm on every level of their property Cllr Frank Biederman, Chair of the LGA’s Fire Services Management Committee, said: “The Christmas period is a time for celebrating and relaxing – which means fire safety advice is especially important to make sure everyone celebrating can enjoy themselves." “We urge people to make sure they are aware of festive fire risks and take the necessary precautions – in particular, testing smoke alarms, checking electronics and purchasing gifts that meet product safety standards, from a reputable retailer. Do remember to think about your neighbors or family members who are elderly or maybe isolated and encourage them to use the Online Home Fire Safety Check. Following fire safety advice helps save lives.” Fire and rescue services Rick Hylton, Chair of NFCC’s Prevention Committee, said: “We’re keen to make sure people keep fire safety on their Christmas list so they remember the celebrations for the right reasons. Christmas can be a busy time for fire and rescue services." "A few minutes completing an Online Home Fire Safety Check and being alert to the risks in your home or the home of your loved ones can help you have a peaceful and safe Christmas.”
Fire incidents are the last thing we want in day care centers, especially knowing that this may cause trauma to the children and consequently affect their education. Henceforth, it is a priority to train staff on Child Care fire safety training to minimize hazards and fire accidents. Owning or managing a day care center means being fully responsible for the safety of everyone occupying the building. It is not only a legal obligation but an ethical duty as well, wherein the health, safety, and welfare of all employees and students under the facility's roof are provided utmost safety. In addressing this matter, fire safety induction program training should be held regularly. Fire extinguisher training This is to ensure that those holding responsibilities know how to manage an evacuation procedure and undergo fire extinguisher training among other safety practices. Taking into account the fire safety legislation along with the child care safety rules, here are the fundamentals of fire training. Teachers or health representatives are expected to know this during the training program The fire safety plan is the basic foundation for establishing rules, which contains every staff's responsibility when practicing fire safety like using fire extinguishers and evacuating. This plan contains the necessary points of determining what to do when a fire alarm sounds off, conducting regular fire drills, knowing how to evacuate the children and where to take them. Teachers or health representatives are expected to know this during the training program. Maximum safety practice Preventing fire revolves around the knowledge of the common causes of fire and disregarding their uses or lowering the risks at the center. By hiring fire and safety specialists, the healthcare facility will undergo assessments on hazards involving electrical wiring, cooking materials and flammable materials present in the area. Once inspected, safety practices will be implemented including the ban of dangerous materials and maximum safety practices in fire-prone places. Fire extinguisher training Knowing where to evacuate is not enough knowledge in the evacuation process Knowing where to evacuate is not enough knowledge in the evacuation process. Behavior and decisiveness are critical qualifiers for whether an employee handling children can successfully manage the situation. These actions are influenced by how the teacher prevents panic during the situation, knows exactly what to tell the children without confusing them, gives brief and clear instructions, and acts upon any given situation with full control. One of the most significant parts in the Child Care Fire Safety Training is the fire extinguisher training courses. Users never know when they have to extinguish flames, so knowing this will definitely be a life-saver. Whether it is suppressing a fire that has just started or doing so while evacuating a building, users will learn best through the acronym P.A.S.S.! P - Pull the locking pin that disables the handles A - Aim the nozzle at the base of the fire to easily extinguish it S - Squeeze the handle to discharge contents towards the fire S - Sweep the nozzle from side to side for a quicker suppression Well-communicated instruction Children are pretty sensitive and curious beings. The two combined can be quite hard to handle knowing it may scare the child or even confuse them more. However, a well-communicated instruction can teach a number of safe behaviors and reflexes to children. By use of a fun and educational activity, kids can learn how to "STOP. DROP AND ROLL" to extinguish fire caught on their clothes or even the basic "GET DOWN LOW, AND GO, GO, GO" for evacuating. While it may seem like an arduous task, implementing fire safety Child Care Fire Safety Training for your workers will always pay off with a maximum safety in the daycare.
Restaurants face particular fire risks that are not present in other environments. With the open flames, paper products, cleaning chemicals, cooking oils, electrical connections, and hot equipment hazards from cooking processes have all of the materials for a fire to blaze out of control. In addition to juggling the daily challenges of operating a profitable restaurant, fire safety management is very likely to be the last thing on the restaurateur's mind. It's important to Implement Fire Safety In the restaurant. Adequate fire protection methods But as every skilled restaurateur understands, using adequate fire protection methods is paramount to the ongoing safety compliance of the restaurant, and might help to prevent injury and serious costs and disruption to their business. Once the restaurant opens for business, all kitchen equipment must be maintained The presence of cooking equipment and the possibility of grease fires can endanger both customers and employees. Planning ahead when designing the place can improve the fire safety of a restaurant. Once the restaurant opens for business, all kitchen equipment must be maintained and fire equipment in the kitchen should be provided to quickly extinguish fire before they spread. Carrying out a fire risk assessment A fire can destroy any business, leading to lost revenues and even permanent closure. But there are actions users can take to avoid fires and reduce the damage. Here are some tips to Implement Fire Safety for restaurant owners: A fire risk assessment differs from a standard risk assessment in that it especially identifies the chances of a fire breaking out on the premises but lots of restaurants don't carry out a separate risk assessment for fires. When carrying out a fire risk assessment, follow this simple five-step process: Step 1 Identify those at risk Step 2 Identify fire hazards Step 3 Evaluate risk Step 4 Keep a record of the findings Step 5 Review monthly, and keep a record of any changes Fire safety rules No matter what the business there are a few fire safety rules which most commercial business premises share. Here are a few of the Reasons users should implement fire safety basics to reduce the risk of fire: Fit an advanced fire alarm to provide early warning of fire Keep fire escape routes free from obstructions Provide a safe exit route Automatic fire-suppression system Activating the system automatically shuts down the fuel or electric supply to nearby cooking equipment Install an automatic fire-suppression system in the kitchen. This is crucial because restaurant fires involve cooking equipment. These systems automatically dispense chemicals to suppress the flames and also have a manual switch. Activating the system automatically shuts down the fuel or electric supply to nearby cooking equipment. Have the fire-suppression system professionally inspected semiannually. Keep portable fire extinguishers as a backup. Restaurants need Class F extinguishers for kitchen fires involving grease, fats, and oils that burn at high temperatures. Class F fire extinguishers are only intended to be used after the activation of a built-in hood suppression system. Keep Class ABE extinguishers elsewhere for all other fires (paper, wood, plastic, electrical, etc.). Implementing fire safety training Implement fire safety training and Schedule regular maintenance on electrical equipment, and watch for hazards like frayed cords or wiring, cracked or broken switch plates and combustible items near power sources. Have the exhaust system inspected for grease buildup. Monthly inspections are required for exhaust systems serving solid-fuel cooking equipment, like wood- or charcoal-burning ovens Train staff to: Use a fire extinguisher appropriately. An acronym users may find helpful is PAST pull out the pin, aim at the base, make a sweeping motion, Ten feet away. Remove all the grease. Cleaning exhaust hoods is especially important since grease buildup can restrict airflow. Be sure to also clean walls and work surfaces; ranges, fryers, broilers, grills, and convection ovens; vents and filters. Never throw water on a grease fire. Water tossed into grease will cause grease to splatter, spread and likely erupt into a larger fire. Remove ashes from wood- and charcoal-burning ovens. Ensure cigarettes are out before dumping them in a trash receptacle. Not to smoke in or near storage areas. Keep flammable liquids properly. Keep them in their original containers or puncture-resistant, tightly sealed containers. Store containers in well-ventilated areas away from supplies, food, food-preparation areas or any source of flames. Clean up to avoid fire hazards. Store paper products, linens, boxes and food away from heat and cooking sources. Properly dispose of soiled rags, trash, cardboard boxes and wooden pallets at least once a day. Use chemical solutions properly. Use chemicals in well-ventilated areas, and never mix chemicals unless directions call for mixing. Immediately clean up chemical spills. Contacting emergency services In case a fire breaks out in the restaurant, the staff members need to take control of the situation and guide customers to safety: Be ready to power down. Train about one individual every shift the best way to turn off electric power as well as gas in case of emergency. Have an evacuation plan. Designate one staff member every shift to be an evacuation supervisor. The individual must be in charge to contact emergency services, determining when an evacuation is actually needed & ensuring that everybody exits the restaurant easily. Ensure your staff knows where the closest exits are, based on the area they are in the restaurant. Conduct Emergency training. Train new workers regarding the evacuation methods and the use of fire safety equipment. Give old staff members a refresher course at least annually. If the Restaurant needs help to implement fire safety regulations the expert team are equipped with the knowledge and experience to provide a comprehensive fire safety service for the Restaurant. They also offer first response fire training online, Hydrant testing, RCD testing, and the new 5-year exit light warranty. Installation of Fire extinguishers, Fire detection systems, Electrical works and many more.
There are many ways for a fire to occur in a childcare center, but there are far more ways to reduce the chances of it. With the help of a fire safety plan, childcare centers can gain a good level of safety without worrying about mishaps and create a Fire-safe Childcare Centre. Corresponding action plan Establishing a Fire-safe Childcare Centre Plan involves these three major steps: Identifying And Assessing The Hazards - While it may not look like childcare centers are prone to danger, it is still a necessity to assess the place. In order to manage these risks, make it a priority to: Look for fire hazards in the facility. By listing down these hazards, it is easier to match them with a corresponding action plan. In the form of a child care fire safety checklist, identify the dangers and correspondingly check the warning systems and emergency procedures used in response to the dangers present. Work with the health and safety representative or anyone responsible for the security of the day care center. Users may also hire a professional fire safety technician in Dalby to help assess the child care center facilities. Gather official data on all hazardous materials present in the facility or nearby. Staying nearby bushfire prone areas also qualifies as hazardous and should be added to the list. File records of previous fire incidents and discuss the fire safety and emergency measures with the concerned safety committee. Firefighting and emergency procedures Controlling And Reducing The Risks - After assessing the risks, reducing them should come after, prioritizing on the following: For a center to be considered fire safe, it has to function under approved Codes of Practice, Regulations, Acts and ultimately, Australian Standards. The building has to be designed to minimize the risk of fire. The same is applicable to allowing firefighting and emergency procedures to take place efficiently. Can flammable materials in child care be replaced with non-flammable ones? If so, supply only the latter. Use fire-resistant furnishings and tools Lessen the use or quantity of flammable materials if possible Installing Of Fire Safe Equipment Supply a sufficient amount of fire safety equipment Install fire systems that are appropriate for the child care center. Consider fire extinguishers, smoke detectors, and fire alarms Identify the different fire extinguisher classes in Queensland matching the type of fire that is likely to occur in the facility Ensure all exit signs are complete and installed in appropriate areas Are there schedules and checklists for the maintenance of fire safety equipment? The materials and the entire daycare should have a regular maintenance check for possible risks Reducing potential injury Planning For Fire And Emergency Evacuation - Ideally, a Fire-safe Childcare Centre evacuation plan should be established to reduce potential injury and illness. It is necessary to involve the employees in building the action plan with emergency procedures outlined and presented to each one. What users need to include in the plan are the following: Discuss among employees the course of action for minimizing hazards. Assign people to raise the alarm to notify emergency personnel such as the fire brigade, ambulance and police. Also, make use of fire detection systems for a quicker way to alert them. Establish an effective communication process allowing quick evacuation and response. Include the significant points on when, how and where to evacuate during an emergency. Make sure the plans are reviewed regularly and updated when necessary. A test run should be conducted to assess each component of the process and identify loopholes that might affect the potency of the plan. The significance of Fire-safe Childcare Centre Plans is equivalent to the security of the occupants' lives, especially the children's. For that reason, it must not be taken for granted. When establishing the safety plan, ensure its accuracy and effectiveness with the help of a fire safety professional.
If someone asks a random staff member if they know all the exit routes in the building or if they know how to determine fire extinguisher types and they say 'no', the medical center might be at risk. The importance of creating a foolproof healthcare fire safety plan is as important as the lives in the health facility. Healthcare fire safety plan Hence, this practical guide: Constituting An Emergency - It is necessary to be able to assess a situation and whether it qualifies as an emergency. In line with fire-related incidents, a situation involving loose wires that can possibly cause electric-induced fire does not necessarily constitute an emergency. However, it requires an immediate checkup. In comparison, a burst of flames in a laboratory certainly calls for immediate evacuation and response. In establishing a healthcare fire safety plan, define an emergency and categorize them into a minor or major disaster for a better assessment of situations. In comparison, a burst of flames in a laboratory certainly calls for immediate evacuation and response Examining The Risks - Risks may be present anywhere in the building. By having regular risk assessments, it is easier to spot danger leading to a fire. Establishing a safety plan is based on a practical assessment of the tasks in the workplace, flammable materials and possible fire that may occur. Aside from this, external risks are well involved in the plan. For instance, a chemical storage facility is situated nearby, consequently requiring backup plans for evacuation. What are the Safety Plans? Practicing Fire Safety - Regulating fire & life safety practices in healthcare involves listing down the right information and practicing fire safety training. While it is better to make preventative plans, following these steps in the healthcare fire safety plan will surely help get it done. Write Down Building Information - The building fact sheet includes the building name, location, owner, occupier, manager, construction and floor area. When making regular assessments and reporting, all these facts should come in handy as reference material. Necessary information also includes the certain capacity of occupants. No building can manage an emergency smoothly with overcrowded rooms. Therefore, managing the number of occupants is necessary by determining the building capacity first and foremost. Determining the building capacity Determine The Inclusions In An Emergency Plan - Detailed information will help constitute an effective emergency plan. This will determine the action plan and assignments when an emergency occurs: List down emergency contact details of the key personnel with specific responsibilities like the fire wardens, first aid officers, and floor wardens. Prepare the contact details of the local emergency services such as the fire brigade, police and poison information center. Describe the mechanisms used to alert people at the facility that an emergency has arisen. It is useful especially with those using different alarms like a siren or bell alarm for different emergencies. Evacuations are to be stated, specifying the procedures used for hearing, vision, and mobility impaired patients. Provide a map of the entire building and the specific locations of each fire suppression or protection equipment, emergency exits and assembly areas. Ensure the evacuation exercises are scheduled regularly for effective results. Instructions should be distributed around the medical center, and evacuation diagrams are installed for frequent reviewing. Include the triggers for informing neighboring businesses and establishments about the fire. Write down the process for a post-incident procedure for trauma effects from the fire and organizing treatments for those affected. All the procedures noted down shall include the frequency of treatment. Basic necessities in healthcare facilities Users will have a thorough list of the installations needed for the facility Install The Required Fire Safety Equipment - Fire regulations in medical centers require the installation of safety equipment needed for utmost safety in the premises. Fire extinguishers, smoke detectors, and alarms are some of the most basic necessities in healthcare facilities. After having the center evaluated by a fire safety officer, users will have a thorough list of the installations needed for the facility. Undergo Maintenance For Fire Equipment - After completing all the necessary requirements for safety equipment, a regular maintenance has to be scheduled for each of them. The testing dates, details of the assessment and other comments are recorded for proof of maintenance and reference for future checkups. How far are users from creating a foolproof healthcare fire safety plan? Let their team guide users through each step and they will help create a customized plan for the health centre.
In spite of having a sufficient fire safety system installed in shopping centers, the occurrence of accidental fires can be more detrimental and the incidence of fire hazard becomes the furthermost and supreme threat to health and safety, as well as property. In order to make sure that the safety of the shopping center, employees and its customers, the fundamental features depends on the fire safety management, fire precaution system and equipment, which should be according to the standard requirements. Nevertheless, fire safety training and fire awareness could necessarily alleviate the damages or rate of fatality during the event of a fire. Strong fire safety systems Fire can take place in a shopping center at any time, coming from many sources Fire can take place in a shopping center at any time, coming from many sources. From the moment of ignition, there is a potential for a major disaster, and it is just a matter of time before it becomes fatal. The best defense against injury or possible loss of life from a fire will always depend on strong fire safety systems and fire safety training. Managing or owning a shopping center usually means being completely accountable for the safety of everyone in the shopping center. It's not just a legal obligation but an ethical duty as well, wherein the health, welfare and safety of all employees and customers are provided utmost safety. In dealing with this particular issue, fire safety training should be held regularly. This is to ensure that those holding responsibilities know how to manage an evacuation procedure and undergo fire extinguisher training among other safety practices. Maximum safety practice Taking into account fire safety regulations, the following are the basic principles of fire safety training: Fire Prevention - Fire Prevention revolves around the knowledge of the common causes of fire and disregarding their uses or lowering the risks. By hiring fire and safety experts, the shopping center will undergo assessments on hazards involving electrical wiring, cooking materials and flammable materials present in the area. Once inspected, safety practices will be implemented which includes the ban of dangerous materials and maximum safety practice in fire-prone places. Fire Safety Plan - The fire safety plan is the fundamental foundation for establishing rules, that contains every staff's responsibility when practicing fire safety like the use of fire-fighting equipment and evacuating. This plan contains the necessary points of determining what to do when a fire alarm sounds off, conducting regular fire drills, knowing how to evacuate the burning building. Methodical and safe evacuation process In the event of a fire, the highest priority is to get everybody out of the burning building as quickly as possible Training Employees - In the event of a fire, the highest priority is to get everybody out of the burning building as quickly, efficiently and carefully as possible. Although regardless of exactly how many times have been informed about the evacuation process and methods of fire protection, reasonable action can be forgotten. The reason behind this is that, in an urgent situation, workers might panic because of the absence of training in the exact process of evacuation. Emergency situation provokes unknown feelings and reactions that require an immediate response, which may not be logical. Fire safety experts believe that training, knowledge and practical experience can cause behavior to be modified. That includes preparing people for how to deal with a fire, this will result in the greatest chance of a methodical and safe evacuation process being conducted. Sufficient fire safety training Under government legislation, all workers have to take sufficient fire safety training. With the shopping centers hours of operation, users will have a hard time looking for the perfect time to conduct the fire safety training. The perfect option for users to train their employees is Online fire safety training, it is a great way to ensure the employees are well-informed and trained without spending a lot of time in the training room. Their employees can have Fire Safety Training from virtually anywhere and anytime as long as they have access to a computer, smartphone or tablet, and they can do it on their own schedules.


Expert Commentary
As a company officer, the day will come where you and your crew are first to arrive at what looks like the beginning of a major incident. Your Battalion Chief (BC) is delayed or diverted to other incidents, so YOU are the Incident Commander (IC). How you set the table for this incident with regard to quickly setting up the Incident Command System (ICS) is critical. And how you use your channels of communication, including the ways you communicate, will be crucial to your success. Before we jump into the ‘how-to’, let’s examine something that looms over everything we do during emergencies, especially fires - ‘The NIOSH 5’. I first became aware of the NIOSH 5, when listening to one of Anthony Kastros’ lectures on incident command and the need for an organization on the fire ground. ‘The NIOSH 5’ Firefighters and emergency workers typically get lost, hurt, or killed at incidents, when any one of five causal factors identified by The National Institute of Occupational Safety and Health (NIOSH) are present: Improper risk assessment Lack of incident command Lack of accountability Inadequate communications Lack of SOPs (or failure to follow established SOPs) Statistically, 50 percent of these line-of-duty deaths (LODDs) and injury events occur in the first 15 minutes of an incident. Half of those occur in the first three minutes! If you’re the initial IC, it’s statistically likely this could happen while you’re in charge. Need for training and practice in handling emergencies Keeping ‘The NIOSH 5’ at the forefront of your mind should trigger the need for training and practice in handling emergencies. Although there are factors you simply can’t control during an emergency, you can control communications, incident command, accountability, repetitive training, and standardization. The following are some things to keep in mind while managing an incident: Arrival on Scene In incident management, setup is everything and oftentimes, determines the outcome of the incident. To use a sports analogy, you definitely want your first pitch to be a strike. So how do you do that? Provide a Solid Size-up Clear and concise on-scene conditions reports set the tone for any incident and establish solid communications The first step is taking a deep breath and giving a good size-up. Clear and concise on-scene conditions reports set the tone for any incident and establish solid communications, and a command tone. Your tone and tempo in your size-up will help focus everyone and create a tactics-driven incident, rather than an emotions-driven one. But, if we’re being honest, being cool takes practice and repetition. Your agency should have a standardized way for how and when this size-up is delivered. In many cases, it’s a fill-in-the-blank script that includes the following four things: What you see (smoke and flames/or nothing showing) The area you see it affecting (the second story, the alpha/bravo corner) What’s happening/what’s on fire or causing the hazard (a two-story home or a sedan next to a building) Establishing command (a must-take command or pass, if you’re going to rescue a citizen) By practicing within your agency’s standards, it enables you to project a cool tone over the radio like you’ve ‘been there before. Order resources early and often Tunnel vision is a death sentence for any IC. In most cases, this is not the time to get sucked into task-level problems. The exceptions to this are structure fires and other emergencies where there is an immediate and known rescue. Otherwise, it’s time to step back, take in the big picture, and make decisions as an IC. Ask yourself: ‘What will this incident do in five minutes? 10? 20? One hour?’ If the answer is ‘get bigger’, then you need more resources. Order them early and often, because they can always be turned around. Don’t try to do too much with too little. Trusted Incident Command System equals early accountability As the initial IC, you’ll be sending crews into the hazard zone. It’s a red flag if, during the initial portion of the incident, you don’t have solid accountability. It’s during this initial ‘fog of war’ that we lose track of crews, and it’s when personnel gets hurt or killed. NFPA 1561, along with other best practices, requires that you know where everyone is and what they’re doing. If you don’t have that knowledge, stop and figure that out, or assign someone to figure it out and report back to you as soon as possible. Benefits of an all-in-one digital platform - Tablet Command Many agencies require the first-arriving officer to implement some form of an ICS to track crew Many agencies require the first-arriving officer to implement some form of an ICS to track crews – a notepad, whiteboard, tactical worksheet, or better yet, a digital command board. The huge advantage of an all-in-one digital platform like Tablet Command is that it’s CAD-integrated and will populate resources for you in real-time. There’s no writing and scribbling while listening to garbled radio traffic, and no trying to ‘catch up’ with resource orders that change on the fly. Accountability integrated into command processes With a platform, such as Tablet Command, all you’re doing is dragging and dropping resources into their assignments, which automatically time-stamps their activities. Maintaining accountability becomes seamlessly integrated into your command processes. These digital platforms also tend to be highly recognizable and easy for others to assume command. It’s paramount that you train extensively on whatever system your agency uses, and that everyone in your region or agency is squared away on how to maintain accountability in a standardized fashion. It’s a problem if you have several chiefs and company officers, and too many (or not enough) ways of maintaining accountability. Many agencies need the first-arriving officer to implement an ICS to track crews Segment and subdivide How do you eat an elephant? One bite at a time. Use your knowledge of your ICS to break up the incident into manageable bites. When the Fire Chief arrives, they’ll have simple questions: Where is everybody? What are they doing? How are they doing? How do I talk to them? Knowing where your people need to deploy and what channel they’re on are critical to accountability. Using the command board is a great way to have all of those questions answered. Using divisions, groups, or sectors can make your life easier in this regard, especially as an incident grows rapidly Using divisions, groups, or sectors can make your life easier in this regard, especially as an incident grows rapidly. This is true because it ensures you’re talking to the supervisors of each segment of the emergency, especially when assessing conditions, actions and needs. Setting up an incident this way should also be an expectation that is agency-wide and practiced in scenario-based training. The terminology should be standardized so that your agency and neighboring agencies aren’t interpreting what you’re trying to accomplish in the heat of battle. Summary A clear communications plan, solid scene size-up, and early establishment of the ICS by company officers are critical to incident success. Combine this with accurate and solid accountability systems, either through analog methods or with a modern digital solution in real-time, and you guarantee safer outcomes for your crews. The best way to be prepared is through long hours of dedicated practice in the command role and, more importantly, an agency-wide understanding of what’s in the play book: Standardization! A standard approach to managing incidents will help you remedy the chaos and enable you to hand over a well-organized incident to the first-arriving Chief.
Electric wiring systems are mostly hidden and embedded in the construction, ceiling spaces, riser shafts, or wall cavities. Cables are installed in buildings by many different trades for different applications and often in polymeric conduit and ducting systems. What is not often realized is that the many miles of cables and many tons of plastic polymers which make up the wiring system can represent a major fixed fire load in a building. Fire Spread & Flame Retardance Most common flexible cables are made from hydrocarbon (oil) based polymers. These base polymers are not usually flame retardant and have high calorific values, so cable manufacturers add chemicals to make them more suited to electrical cable use. Halogen Additives Halogenated polymers have a negative side effect because in the fire they release halogens as toxic halides Halogens like Chlorine are particularly good additives that help retard flame propagation and don’t significantly impact the dielectric properties of the polymer so halogens are used in both cable insulations and cable sheaths. These halogenated polymers (example: PVC) also have a negative side effect because in the fire they will release the halogens as extremely toxic halides and when combined with the moisture in the eyes, mouth, and lungs are very irritant. Often standard PVC cables will also release large amounts of acrid smoke. Non-Halogenated Materials Often, designers realize the dangers of fire spread, halogen, and toxic gasses, plus the smoke released from cables in the fire so they specify cables to have ‘Halogen Free’, ‘Flame Retardant’, and ‘Low Smoke’ properties. For these cases, cable manufacturers need to use other non-halogenated materials, mostly with flame retarding fillers like alumina-trihydrate (ATH). Electric And Mechanical Properties Halogen Free flame-retardant cables most often use an unfilled or less filled polymer like Polyethylene While effective in retarding flame propagation, these fillers often negatively affect the polymer by reducing dielectric performance or affecting mechanical & water resistance. For this reason, additives like ATH are mostly used only in cable jackets. Halogen Free flame-retardant cables most often use an unfilled or less filled polymer like Polyethylene (PE or XLPE) or EPR for the insulation which has good electric and mechanical properties but may not be very flame retardant. Fire Propagation Performance Often the best flame-retardant cables are halogenated because both the insulation and outer jacket are flame retardant but when we need Halogen Free cables, we find it is often only the outer jacket that is flame retardant and the inner insulation is not. Testing Under Overload Conditions This has significance because while cables with a flame-retardant outer jacket may pass flame retardance tests with an external flame source, (BS EN 60332-1, BS EN 60332-3) the same cables when subjected to high overload or prolonged short circuits have proved in university tests to be highly flammable and can even start the fire under uncleared short-circuit or overload conditions. This effect is known and was published by Nexans/Olex Cables Australia at the 8th International Conference on Insulated Power Cables (Jicable’11, 19-23 June 2011, Versailles, France). What this means is your flame-retardant cables may not be flame retardant under uncleared short circuit or overload conditions. Intrinsic Temperature Change BS 7671 and IEC 60364-5-52 have rating tables allowing some cable designs to operate up to 90°C In the UK, EU, and many other countries, BS 7671 and IEC 60364-5-52 have current rating tables allowing some cable designs to operate at conductor temperatures up to 90°C. Whilst technically acceptable for the cables, what has not been fully considered by is the intrinsic change this cable operating temperature may have on the cable’s flammability. Conducting Tests At Operating Temperature Where cables are required to be flame retardant to IEC 60332-3-22/23/24, it is concerning these tests are not conducted on cable samples preconditioned to the rated operating temperature of the cable, but rather commencing at room temperature. It is well known the hotter a material is the more easily it will burn so designers and users of cables that claim to meet these standards may be surprised to learn their cables might not be flame retardant at all when installed and used at their rated operating temperature. The Primary Importance of Fire Load Many countries around the world are moving to greater use of Halogen Free and Flame Retardant (HFFR) cables in the pursuit of increased building safety. Whilst an admirable motive, the reality can be rather different: In asking for both flame retardant and halogen-free properties, cable manufacturers often need to compromise between high flame retardance with halogens or reduced flame retardance without halogens. Polymers Cable makers often choose polyethylene because it is easy to process and cheap, however, it has a high fire load To provide halogen-free cables, cable makers most often choose polymers like polyethylene (PE & XLPE) because it is easy to process and cheap, however, although polyethylene is halogen-free it has a naturally high fire load. The following table compares the fire load in MJ/Kg for common cable insulating materials against some common fuels. The Heat Release Rate and volatility in the air for these materials will differ but the fuel added to a fire per kg and the consequential volume of heat generated and oxygen consumed is relative. Fire Safety When considering fire safety in cable design, we need to understand the most important factors: Fire experts tell us most fire-related deaths in buildings are caused by smoke inhalation, temperature rise, and oxygen depletion or by trauma caused by jumping in trying to escape these effects. Notably, the most common cause of death in building fires is Smoke inhalation with asphyxia due to CO (Carbon Monoxide) although HCN (Hydrogen Cyanide) is becoming more common with the increasing use of man-made and lightweight synthetic building materials. Notably, neither is a Halogen gas. Smoke Highly flame-retardant cables with a high oxygen index will help here because they may limit the fire spread The first and most important aspect of smoke is how much smoke? Typically, the larger the fire the more smoke is generated so anything we can do to reduce the spread of fire will also correspondingly reduce the amount of smoke. Highly flame-retardant cables with a high oxygen index will help here because they may limit the fire spread. Flammable Gasses Smoke will contain particulates of carbon, ash, and other solids, liquids, and gasses, many are toxic and combustible. In particular, fires in confined areas like buildings, tunnels, and underground environments cause oxygen levels to drop near the fire source and this contributes to incomplete burning and smoldering which can produce increased amounts of smoke and toxic by-products including CO (Carbon Monoxide). As we know the presence of halogenated materials will release toxic halides like Hydrogen Chloride together with many other toxic and flammable gasses in the smoke. IEC Smoke Tests For this reason, common British, and IEC smoke tests (BS EN 61034-2) are conducted by burning cable samples in large 3-meter3 chambers with an alcohol fuel and plenty of air. This can provide very misleading smoke figures because complete burning in flame often releases far less smoke than partial incomplete burning or smoldering which is likely in practice. Low Smoke Cables There are no smoke tests done on cables subjected to heating under short circuit or overload conditions There are no smoke tests done on cables subjected to heating under short circuit or overload conditions which for some common “Halogen Free” insulation materials, give off significantly more smoke than in flame. Simply specifying low smoke cables to meet common British, IEC standards and then thinking this will provide a low smoke environment during a real fire may give comfort to the specifiers and authorities but unfortunately in practice be of little help for the people involved. Halogens, Toxicity, Oxygen Depletion, and Temperature Rise It is concerning that the UK, Europe, and many other countries adopt the concept of halogen-free materials without properly addressing the subject of toxicity. Halogens released during combustion are extremely toxic but so too is carbon monoxide and this is not a halogen gas. It is common for specifications to call for halogen-free cables and because of this, encourage the use of Polyethylene because it is halogen-free. Polyethylene And Carbon Monoxide Burning polyethylene will not only generate almost 3 times more heat but also consume almost 3 times more oxygen Burning polyethylene will generate almost 3 times more heat than an equivalent PVC cable. This means that burning polyethylene will not only generate almost 3 times more heat but also consume almost 3 times more oxygen and can produce large amounts of Carbon Monoxide, especially with partial or incomplete burning. Given that it is carbon monoxide that is statistically responsible for most toxicity deaths in fires this situation is at best alarming. (Carbon Monoxide is a colorless and odorless toxic gas that inhibits the blood hemoglobin from absorbing oxygen. Prolonged exposure results in asphyxiation). Heat Of Combustion The fuel elements shown in the table indicate the amount of heat that will be generated by burning 1kg of the common cable insulations tabled. Certainly, this volume of heat will accelerate the burning of other adjacent materials and may help spread the fire in a building but importantly, to generate the heat energy, oxygen needs to be consumed. The higher the heat of combustion (MJ/Kg) the more oxygen is needed, so choosing insulations (even if Halogen Free) with high fuel elements is adding significantly to at least four of the primary dangers of fire to humans: Temperature rise, Oxygen depletion, Toxic gas emission, and Flame spread. Conclusion The popularity of “Halogen Free” properties while ignoring the other toxic elements of fire, and the correlation to smoke, heat, and oxygen depletion is a clear admission we do not understand the subject well, nor can we easily define the dangers of combined toxic elements or human physiological response to them. It is important, however, that we do not continue to design with only half an understanding of the problem. While no perfect solution may exist for organic-based electric cables, we can certainly minimize these critically important effects of fire risk with a more holistic understanding. To this end commercially available non-organic cable systems can provide a more holistic solution to the polymeric HFFR cable paradox.
There’s no doubt the Building Safety Act and Fire Safety Act are driving major improvements in the construction industry’s quality and approval processes. Although the initial focus of the legislation is on high-rise residential buildings, it’s predicted to be rolled out across the entire sector soon, tightening fire safety regulations in hospitals, hotels, and commercial offices and we await the rafts of secondary legislation that will really redefine the regulatory landscape. Many fear that commercial real estate professionals will be unprepared for the higher levels of compliance required, by the incoming regulations. New requirements for competency, collaboration, and digitally presenting joined-up information will inevitably be imposed on architects, building inspectors, owners, and construction product manufacturers. Fire regulations for commercial buildings However, currently, fire regulations for commercial buildings remain lax and there’s ambiguity about what constitutes appropriate fire safety system management, as well as how to prepare for revised building and fire safety requirements, as they become available. It’s all too easy to take a laissez-faire attitude, but adopting an ‘it will never happen to me’ approach is likely to lead to problems down the road, so contractors, asset owners and FMs alike need to get with the legislative program and fast. Understanding of fire safety ratings for things to increase If specifiers are cutting corners and installing inadequately rated products today, there will be very costly consequences later It is certain that office interior specification, coupled with ongoing checks and a robust understanding of fire safety ratings for things, such as interior doors, panels and partitions is likely to be increasingly challenging going forward. Importantly, if specifiers are cutting corners and installing inadequately rated products today, there will be very costly consequences later. As a result, it is advisable to go above and beyond current construction regulations, when specifying materials for commercial office interiors, in order to future-proof and keep occupants safe. The Grenfell turning point Grenfell was a wake-up call for the construction sector, particularly for construction product manufacturers and those involved in fire protection and fire testing. Before the tragedy, many believed their products were safe and their methods were flawless and tested according to official guidelines. However, this terrible event compelled the industry to examine its manufacturing procedures, the efficacy, adequacy and relevance of testing and certification, as well as product performance claims made in marketing collateral. This re-evaluation, which found many parts of the specification process not fit-for-purpose, has, thankfully, culminated in a total cultural overhaul. Asking important questions regarding building fire safety Fundamentally, there was not enough questioning before Grenfell. Now, we’re re-thinking everything, asking ourselves: Are we doing things correctly? What’s the risk? How can we mitigate that risk? Five years on, the interpretation of evidence, whether direct fire test evidence or third-party assessment, has become much more refined, and rightfully so. Designers and contractors are paying more attention to the evidence used to support proposed items and applications, while manufacturers are re-thinking their use of evidence, in line with post-Grenfell thinking. Adequacy of test evidence The adequacy of test evidence for a given application is now being scrutinized much more closely The adequacy of test evidence for a given application is now being scrutinized much more closely, as are the testing methodologies. It now raises the important question: ‘Does this test accurately represent the effect in a real-world scenario?’ Unfortunately, the capacity to deliver on these questions is not matching good intentions. The rising need for test evidence of fire resistance rather than merely accepting an assessment has caused testing facilities to become overloaded, resulting in much longer wait times. Assessments are now heavily connected to appropriate fire test findings, which necessitate the gathering of evidence and a higher level of analysis, in order to provide assessments. The entire process has become necessarily more complicated, but this has affected efficiency, something which will need to be addressed as construction output inevitably increases. R&D cultivates innovation Fortunately, there are solutions within reach, thanks to significant advancements in the development of fire-safe products and materials across the industry. There’s been an increase in project-specific developments, as suppliers collaborate with designers and fire regulatory organizations to share their expertise. As a result, rather than merely installing the best fit, projects are now specified with fully customized fire-rated systems. Meanwhile, continuing R&D has led to many organizations looking ahead and anticipating shifting demands and trends in the built environment. It’s leading to additional testing and product development for applications that aren't already covered by existing technologies, and a commitment to the highest-quality fire solutions, meaning safer and higher-performance products. Expertise and training are key It’s important to note that choosing fire-rated products does not make the area fire-safe by default. Once the facility is in operation, a systems approach is needed to ensure that the installation and risk assessment of fire-rated products are periodically monitored. Extensive training and CPD must be taken into account for specifiers Even the slightest modification to a fire-rated product, such as changing a glass door’s opening system, might compromise its integrity. It’s critical to completely understand the ins and outs of the product being defined, in order to ensure that it's used correctly. As a result, extensive training and CPD must be taken into account for specifiers and office building managers alike. Increased training and CPD Increased training and CPD will keep the industry on track to deal with the level of comprehensive knowledge necessary Increased training and CPD will keep the industry on track to deal with the level of comprehensive knowledge necessary, specifying according to need and meeting the high standards of the near future. Continued development of fire knowledge is crucial, as the latest high-performance glass doors in offices today are specialized pieces of technology and fire-rated systems behave very differently from other glass partitions or doors. The design dilemma Another significant challenge is incorporating fire safe components into a space without losing its aesthetic appeal, but remaining compliant. Designers are increasingly aiming to open up space to bring in natural light and encourage a sense of well-being for the occupants, meaning walls that would previously have been solid are being specified as glazed. This means that large panels of glass, beyond the capacity of fire test facilities, must be handled sensitively and installed within a bespoke system. This necessitates close liaison with certification authorities to identify what can be assessed from the test evidence provided. Of course, workplaces must be fire safe, look good, and feel pleasant to work in. The sheer complexity of the day-to-day office functionality is a difficult issue. Aesthetics are often a requirement that is added to the fire resistance of fire doors. But it’s often the case that suitably certified hardware simply doesn’t exist. Glass office partition systems Can fire safety and great design coexist in the office space? Yes, definitely. Can fire safety and great design coexist in the office space? Yes, definitely. This is because, the latest glazed and sliding doors, adjustable ‘office pods’, and acoustically-optimized walls are all made with fire safety, sustainability, and elegant design in mind. Many glass office partition systems allow natural light and air circulation to flow through the room, which helps to improve employee well-being and boosts performance. Fire safety is of the utmost importance Fire safety and design can harmoniously co-exist in an office space, but it comes down to managing expectations. Fire safety is of the utmost importance, and as the requirements tighten, the commercial office industry will catch up with fire safety standards, testing and reporting regimes, and ongoing compliance. Fortunately, fantastic fire-resistant workplace solutions are entering the market, built for safety, flexibility, and aesthetic appeal.
Editor's Dispatch
Among residential fire hazards, a heating, ventilation, and air conditioning (HVAC) system is probably not at the top of the list. However, there are fire risk factors related to HVAC that can be mitigated through greater awareness and additional precautions. The reality is that an HVAC fire, like any other, can be dangerous and even deadly. flammable refrigerants The use of flammable refrigerants in HVAC systems is a growing trend since newer refrigerants that do not contribute to global warming can also be mildly flammable. However, these materials do not pose a fire threat because they are tightly sealed inside systems during manufacture and using standard regulations. Fire risks Factors Proper installation and maintenance of HVAC systems can significantly reduce the dangers of factors Fire risks related to HVAC include factors such as overheating motors, faulty electrical wiring, and leaky fuel lines. Educating consumers on the fire risks of HVAC systems contributes to fire prevention. Proper installation and maintenance of HVAC systems can significantly reduce the dangers of factors such as gas leaks. Faulty wiring Faulty wiring is the top reason an air conditioner might catch fire. Rusted wires should be replaced, and wiring should be insulated end-to-end. Sparks from faulty electrical connections can land on something flammable and ignite a fire. Faulty wiring can quickly cause an HVAC fire, and frayed, disconnected, or corroded wire should be repaired quickly. Over time, connections can become loose, which can burn the wires and cause a fire. Wiring should match a unit’s amperage, too. clutter crowding HVAC equipment A three-foot buffer area should be maintained between HVAC equipment and any stored materials Also contributing to a fire hazard is clutter crowding HVAC equipment. Things such as boxes, crates, extra clothing, holiday decorations, brooms, cleaning supplies, and other items can increase the risk of fire if they are stored too near HVAC equipment. Especially dangerous are any flammable materials, such as aerosols, oils, or sprays. A three-foot buffer area should be maintained between HVAC equipment and any stored materials. Dirt, debris, and appliances Bushes or other appliances near an outdoor unit can also increase fire risk. Debris, leaves, and paper should also be kept away from the unit. Dirt, dust, and debris can contribute to fire risks related to HVAC equipment. Dirt accumulating inside a system’s motor can cause overheating. The dirt inside vents and/or coils can obstruct airflow, which can lead to a fire hazard. Insufficient lubrication Voltage level, either too high or too low, can also make a motor overheat Insufficient lubrication is another factor, contributing to friction and shortening the life of motor bearings. Voltage level, either too high or too low, can also make a motor overheat. Blown-out parts or components could cause an air conditioner to overheat. An overworked system could catch fire. gas furnaces In addition to fires, gas furnaces also pose other dangers, such as carbon monoxide poisoning. Cracked heat exchangers in HVAC systems can leak carbon monoxide. In addition to smoke detectors, residents should install carbon monoxide detectors throughout the home, and keep them powered by replacing batteries as needed. Measures in HVAC-related fires A qualified HVAC technician can inspect the unit, assess needed repairs, or install a new unit In case of fire related to an HVAC system, the first thing to do is exit the building and surrounding area and call emergency services. After everyone is safe and the fire is contained, a qualified HVAC technician can inspect the unit, assess needed repairs, or install a new unit. scheduled routine maintenance Keeping up with scheduled routine maintenance visits can be an important preventative strategy. Heater and air conditioner systems should be checked at least once yearly. If there are gases or burning plastic smells, a technician should be contacted for an unscheduled inspection. Any foul odor from an HVAC system might signal burning wires, and the unit should be shut off to prevent further damage. Safe installation with professionals Fire risk increases if a system is installed by an inexperienced technician who is not trained Deploying professionals to work on an HVAC system can ensure they are installed safely. Fire risk increases if a system is installed by an inexperienced technician who is not trained to spot a potentially dangerous situation. Using professional services ensures peace of mind. Individual or portable AC units should be plugged directly into a power outlet without using extension cords, which could overheat or cause sparks. impact on indoor air quality An early signal of an HVAC fire might be smoke or burning smells coming from a gas furnace. Poorly fitting gas connections can cause leaks that negatively impact indoor air quality as well as increase fire risk. Leakage of highly flammable fuel, including oil, gas, or other substances, can ignite if it encounters hot elements of an HVAC unit. Fuel is highly flammable, but it is not a hazard if it remains safely within the lines.
As motor vehicle designs evolve, including the addition of lithium-ion batteries, for example, firefighters and first responders must also adapt. They need information about the vehicle’s fuel and energy usage and guidance on extricating occupants following an accident. Emergency Response Guides (ERGs) can help responders by using standardized labels, colors, symbols, and graphics to make emergency information more complete, accurate, and accessible during training and response. ISO 17840 ISO 17840 is an international standard that ensures first and second responders have fast and easy access to the information they need to perform their lifesaving duties in case of an automobile fire or accident. The ISO 17840 standard includes a template layout of ERGs to provide necessary and useful information about a vehicle involved in an accident. in-depth information The goal is to shorten the "golden hour" and quickly identify the energy source and hidden hazards on any vehicle The guide can be communicated in paper or electronic format. The goal is to shorten the "golden hour" and quickly identify the energy source and hidden hazards on any vehicle. The standard supports the team to rescue as many occupants as quickly and safely as possible. ERGs also provide in-depth information about fire, submersion, and leakage of fluids. New vehicle hazards Changing hazards of newer vehicles include propane- and LPG-powered vehicles that can explode more powerfully if tanks are heated, and fuel bottles that can become projectiles. Also, electric and hybrid vehicles have high-voltage batteries and electrical wiring that can electrocute first and second responders and victims if not properly disarmed. Furthermore, hydrogen and other fuel cells produce toxic and flammable gases that behave differently than gasoline or other traditional fuels. ERG template The ERG template follows in principle a flowchart for the main actions of first and second responders arriving at an accident scene. The template provides relevant information for a vehicle involved in a traffic accident (including immobilization, disabling of hazards, access to occupants, shut-off procedures, and handling of stored propulsion energy). Standardized colors and pictograms make it easier for first and second responders and vehicle manufacturers to understand each other. Information on the ERG is linked to the “rescue sheet” (ISO7840 parts 1 and 2) to inform training and development of rescue procedures. The headings/content of the rescue sheet and the ERG are aligned. knowledge and preparation Public safety organizations can download free examples of ISO 17840 templates for creating rescue sheets International Technical Committee for the Prevention and Extinction of Fire (CTIF), the European New Car Assessment Programme (Euro NCAP), and the Swedish Institute for Standards (SIS) created the ISO 17840 standard. With more alternative fuels and propulsion systems entering the market, more knowledge and preparation are necessary in order to approach an accident scene safely. Public safety organizations, educational organizations, and first and second responders can download free examples of ISO 17840 pictograms, templates for creating rescue sheets for any vehicle, and other information to create ERGs for training purposes and as guides for local rescue procedures. recommendations of ISO 17840 Among the vehicle manufacturers who have complied with the recommendations of ISO 17840 are Honda, Hyundai, Mitsubishi, and Volkswagen. In addition, another dozen or so manufacturers are progressing on the road to compliance, including BMW, Ford, General Motors, KIA, Nissan, Subaru, Tesla, and Toyota. The National Fire Protection Association (NFPA) maintains a collection of emergency response guides, and most manufacturers have posted their updated ERGs on their websites.
In Ann Arbor, Michigan, USA, in May 2022, a helmet camera recorded firefighters extinguishing a truck fire along I-94, catching every detail as sparks flew and firefighters hosed down the truck to suppress the blaze. Firefighters also hosed down the grass on the side of the freeway to put out hot spots and prevent a grass fire, MLive.com reported. The helmet-cam was part of a voluntary program that involves Ann Arbor firefighters wearing cameras when responding to active structure fires to capture video that can be used as a training tool, in order to better understand what went right and what went wrong. Video can also be released to the public to showcase how tax dollars are being spent. A focus on structure fires precludes any concerns about privacy. Helmet-cams used by firefighters Helmet-cams used by firefighters can provide a valuable tool for training and post-incident analysis Helmet-cams used by firefighters can provide a valuable tool for training and post-incident analysis. On the other hand, they could impact how a firefighter does his or her job or even violate privacy concerns and/or the public trust. While debate around the use of body-cams by law enforcement officers has mostly been settled, opinions still vary about the use of helmet-cams by firefighters. In one sense, the rules and regulations have not caught up with the technology, including smaller (and inexpensive) video cameras that can easily (and even discreetly) be mounted on a firefighter’s helmet. Some departments have banned use of helmet-cams, while others have sought to restrict and control their use. Still others haven’t given it much thought. Multiple perspectives for post-incident analysis An advantage of helmet-cams is to record video of the actions of officers and firefighters at an incident and to provide multiple perspectives for post-incident analysis. Critiquing performance is a learning tool to encourage continuous improvement. In case of an injury or line-of-duty death (LODD), helmet-cam footage provides an unblinking record of exactly what occurred. If a time element is being assessed, a helmet-cam video can display each activity along with a time display, thus eliminating the need for a stopwatch. Clear and time-marked audio recording In addition to video, helmet-cams can provide a clear and time-marked audio recording, not limited by radio-frequency interference. (Audio recordings are subject to additional privacy concerns in some jurisdictions.) A possible downside of using helmet-cams is to distract a firefighter from his or her duties or to narrow their focus to the detriment of a broad awareness of their surroundings. It is important that a firefighter not miss something that is happening at the periphery of his or her line-of-sight. Helmet-Cams can distract a firefighter’s attention Conscious of how they appear in a video recording, a firefighter might be more guarded in their actions or words; at the other extreme, they might be tempted to “show off” for the camera by taking greater risks to provide more dramatic footage. A firefighter with a helmet-cam might also become preoccupied with operating the camera to optimize video to the detriment of other concerns. Becoming fixated on the technology can distract a firefighter’s attention from the real job at hand. Creating a policy that addresses issues are helmet-cams use Departments should consider carefully the issues surrounding helmet-cams and create a policy Departments should consider carefully the issues surrounding helmet-cams and create a policy that addresses those issues. Fire service leaders may benefit from collaborating with local police leaders who have worked with body-cam video and know the possible evidentiary value of video that can be captured on the devices. Fire departments should be aware that any captured footage may have evidentiary value, if it relates to a crime or police internal affairs investigation. Unlike body-cams used by police, which download video to the department at the end of a shift and are covered by department policy, helmet-cams are less restricted and less well-managed. Firefighters may even own their cameras. Privacy concerns surrounding the use of helmet-cams Some fire departments, such as Houston, San Antonio, and San Francisco, have banned helmet-cams because of privacy concerns and worries about how a video might embarrass a department. Privacy concerns include the use of helmet-cams in medical calls, which make up most a firefighter’s daily responses. There should be rules that ensure that videos do not eventually make their way to Internet sites such as YouTube. In New Jersey, for example, Cathy’s Law (passed in 2012) restricts images and recordings at emergency scenes, such as motor vehicle accidents.
Case studies
As a longtime maintenance provider for Trafalgar Theatres at their Orchard Theatre site in Dartford, Blake Fire & Security and Cygnus’ distributor Illumino Ignis (Kent) Ltd (IIKL) were approached for a solution to a unique problem: Satisfying the stringent fire safety requirements of their new temporary venue to hold 1,091 audience members, while the main Orchard Theatre was closed due to RAAC Works. SmartNet-Pro fire detection With a very short turnaround of a week, Blake Fire & Security and IIKL instantly knew that the Cygnus EN 54 certified, fully wireless SmartNet-Pro fire detection and alarm system would be a perfect fit for the venue. It provides an aesthetically pleasing solution and quick installation, with full EN 54 and BS5839 Part 1 compliance, while also allowing the right cause and effects for the theatre operation. SmartNet-Pro range’s wireless network features SmartNet-Pro range’s wireless network features give a minimum of two communication paths to each wireless device Designed to deliver a reliable and safe solution, the SmartNet-Pro range’s wireless network features patented Cygnus technology and is run by battery-powered radio devices as part of a robust, self-forming, and self-healing mesh network, giving a minimum of two communication paths to each wireless device for maximum reliability. “We have worked with Cygnus and the SmartNet-Pro system previously and knew it would be ideal for this unique project,” comments Rory Foster, Fire Safety Systems Manager at Blake Fire & Security. 100% wireless “SmartNet-Pro is 100% wireless as well as being robust and reliable, it was exactly what we needed for the complexities of this project. We also knew we could rely on the Cygnus team to help deliver the project in a timely and efficient way.” Given the nature of the venue, the fire alarm system needed to have some advanced features to give the theatre control of the system. Factors to consider The Blake Fire & Security and IIKL team were required to consider these factors when creating the system: Smoke Machines being used during the performances. A function of the SmartNet-Pro panel allowed us to program a function on the button on the control panel to isolate the smoke elements of the detectors in the auditorium during performances (Show Mode) while keeping the Heat elements of the detectors functioning as normal. Heating pipes with hot air being blown throughout the site. By utilizing the Cygnus SmartNet-Pro Combi Smoke/Heat A1R detectors, we were able to only have the smoke detection parts active for devices in the stream of the hot air, to avoid A1R false alarms. The costly effect of a false alarm and evacuating the venue during a performance. By having a 30-second initial delay, and a 2.5-minute investigation delay, we satisfied both the Fire Service and the Theatre by allowing the theatre staff to assess the cause of the alarm before evacuating the venue, without leaving too long without the fire alarm activating if no one responded. The combustible nature of the building is mostly dressed in linen throughout. Additional smoke detectors were installed on the edges of the linen-draped ceilings at the request of the local fire authority, with high sensitivity smoke and heat detection to raise the alarm extremely quickly if the linen was likely to become compromised by fire. specification and design The whole process was taken care of without any design surprises at the end of the project After a free site survey and design service, Blake Fire & Security and IIKL provided the specification and design to the theatre who then got the design signed off by the local council and local fire authority. Working closely with the theatre and local council, amendments and additions were made to the design, so the whole process was taken care of without any design surprises at the end of the project. testing and demonstrations The SmartNet-Pro system of 65 devices was installed in a day, with another day allowed for testing and demonstrations; using rods and Unistrut fixings to fix detectors into positions where wired detectors would not feasibly be able to be installed. The fire alarm panel was installed by the stage door so that the stage door staff could hear when an activation has occurred, and then decide on whether to initiate the investigation delay. Zone Plan and As-Fitted Drawing The system was demonstrated to the crew, so they knew what the alarm sounded like, and how to react As with all Blake Fire & Security and IIKL installations, a framed Zone Plan and As Fitted Drawing were fitted by the Control Panel, to give the Theatre Staff and Fire Brigade instant knowledge of the building, and where the Fire Alarm activation has occurred. All members of the Stage Door crew were trained by Blake Fire & Security and IIKL in the operation of the system including all the advanced functions like the delays and “Show Mode”. The system was demonstrated to the crew, so they knew what the alarm sounded like, and how to react when the panel buzzer activates. high-level detection Rods with the detectors mounted onto them were clamped onto the trusses for the lighting, giving high-level detection in the auditorium where it was not possible to fix the black linen ceiling. These detectors were then programmed on the SmartNet-Pro system to be Heat Only when the system is in “Show Mode” to prevent unwanted alarms from special effect smoke used during performances. Manual Call Points Combi detectors were mounted just below the linen ceiling using rods clamped to the metal structure Ensuring all exits including stage exits were covered by Manual Call Points which would instantly evacuate the building without delay was imperative to allow occupants and staff in the venue to feel safe in the knowledge that if a person identifies a real fire, the fire alarm can be raised instantly at any exit from the building. The ceilings in the Front of the House have heating tubes running through them, so combi detectors were mounted to the side of this, just below the linen ceiling using rods clamped to the metal structure above the linen. smoke detection Extra smoke detection was installed along the low-level edges of the linen ceilings, on L Brackets, so that a fire could be detected quickly before the linen ceilings caught alight. These detectors were supplementary to the main detection along the apex of the ceilings. Given the nature of the ceilings, conventional wiring methods would not have been possible without a very unsightly installation, so the wireless nature of the Cygnus SmartNet-Pro system was an obvious choice. ongoing maintenance Blake Fire & Security and IIKL issued the O&M Manual with all certificates and drawings required for Building Control Following the completion of the installation, commissioning, and testing Blake Fire & Security and IIKL issued the O&M Manual with all certificates and drawings required for Building Control to sign off the system and deem the venue safe to open to the public. Blake Fire & Security and IIKL will provide ongoing maintenance of the system to ensure that the system is kept up-to-date and compliant. EN 54 certified, and BS 5839 compliant fire detection SmartNet-Pro is the world’s first 100% wireless, EN 54 certified, and BS 5839 compliant fire detection and alarm system while the new SmartNet-100 is ideal for small to medium-sized projects, where the scalability of SmartNet-Pro is not required. Cygnus was thrilled to support the project by providing a complete SmartNet-Pro system to guarantee the fire safety requirements were met.
Comelit-PAC has been working with partners - GB Integrated Systems to fit the latest fire safety systems at the Hop House in Deva City Office Park, in order to ensure the safety of all who work and visit the unique work environment. Part of the former Threlfalls Brewery, an iconic feature of the Manchester city skyline, Deva City Office Park presents an eclectic mix of business space presented in a Grade II listed Brewery building or 17 high-spec self-contained office units. Balancing modern design GB Integrated System worked directly with the site management team to upgrade the addressable panels With the need to offer 24 / 7 security and fire safety, GB Integrated System worked directly with the site management team to upgrade the addressable panels, and specified Comelit-PAC’s latest LogiFire solution. Iain Taylor, Director of Asset Management at Northwood Investors International Limited, said: “We knew we had complex requirements for Deva City when it came to security and fire safety, with each individual business on site needing its own risk assessments. This was set against the buildings themselves, where any upgrades had to be sympathetic to the specific interest Grade II classification and balance modern design and use of technology.” Easy fire safety solution Iain Taylor adds, “GB Integrated Systems made it a priority to understand this and work with us right from initial design and specification to implement a bespoke solution that could accommodate our requirements. From a fire safety perspective, Comelit-PAC was recommended, to ensure we could reduce installation time and minimize disruption to business activity for the benefit of our occupiers.” GB Integrated System specified Comelit-PAC’s LogiFire Easy fire safety solution. The office park required a stand-alone 1-loop analog addressable panel. Fire safety solution We recommended Comelit-PAC’s Logifire solution essentially because of its simple design" Mike Gray, Technical Director at GB Integrated Systems, stated: “We recommended Comelit-PAC’s Logifire solution essentially because of its simple design, and ability to easily install using existing cabling, so as not to interfere with the style of the development and its unique character. From the owner’s perspective, its style and flexibility of use means that it is the best fire safety solution to protect the occupiers collectively and blend seamlessly with its surroundings.” Logifire addressable system, has been designed to offer a simple to install, fire safety solution that is compliant with BS and EN standards. It is complemented with a range of detectors, offered with award-winning designs to ensure systems blend with their surroundings. Mind fire safety Mandy Bowden, Comelit-PAC Fire Manager, concluded: “When it comes to fire safety, the market is growing rapidly amid greater awareness of the need for risk assessments, remediation work, building upgrades and ongoing maintenance in the new-build sector as well as at existing sites. What our work with GB Integrated Systems at Deva City Office Park demonstrates is the need to assess each development as early as possible in a works program to ensure solutions meet exact requirements." She adds, "We understood that any upgrade had to be carefully considered with regards to how it will impact on the aesthetics of the overall premises. Together, we identified how LogiFire as a single solution, could be installed quickly and effectively for the benefit of all who work on-site. It allows for total peace of mind fire safety.”
Oshkosh Airport Products, a division of Pierce Manufacturing Inc., a subsidiary of Oshkosh Corporation announces Airservices Australia has issued a purchase order for four Oshkosh Airport Products Striker® Volterra™ 6x6 Aircraft Rescue and Fire Fighting (ARFF) hybrid electric vehicles. These environmentally advanced fire apparatus will be deployed at the new Western Sydney International Airport (WSI), set to open in 2026. Striker Volterra 6x6 The Striker Volterra 6x6 comes equipped with an Oshkosh-patented hybrid-electric drivetrain, featuring an electro-mechanical infinitely variable transmission. This enables zero-emissions operation through the integrated onboard batteries and uninterrupted power supply by coupling with the internal combustion engine for pumping and drive systems. innovative design Airservices Australia is making a significant investment to support the development of an 'airport of the future' WSI is a transformational infrastructure project expected to boost economic activity, provide local employment opportunities, meet Sydney's carbon-neutral sustainability initiatives, and meet the area’s growing aviation needs. Airservices Australia is a government entity making a significant investment to support the development of an 'airport of the future', featuring world-pioneering technology, innovative design, and a sustainability plan incorporating assets like the Striker Volterra ARFF hybrid electric vehicles. sustainability "As the first airport built in Australia in over 50 years, WSI is not just an airport; it's a statement of intent for a more sustainable future,” said Dave Archer, Vice President of Engineering for Oshkosh Vocational. He adds, “The Striker Volterra vehicles, with their hybrid electric technology, align perfectly with Airservices Australia and WSI’s goals. These vehicles are not only an asset to emergency response capabilities but also play a crucial role in larger environmental sustainability initiatives." environmentally conscious choice Dave Archer continues, "They symbolize a dedication to intelligent design, energy optimization, fire crew safety and efficiency, and ultimately, a carbon-neutral future." Striker Volterra ARFF hybrid electric vehicles demonstrate the most advanced acceleration and reduced fuel consumption compared to our standard diesel models, making them an environmentally conscious choice for emergency response services. Striker Volterra features Striker Volterra ARFF demonstrates a 28 percent improved acceleration compared to the standard diesel models WSI’s four new Striker Volterra 6x6 vehicles will feature an industry-pioneering modular cab design, TAK-4® all-wheel independent suspension, and a 50’ Snozzle® High Reach Extendable Turret. They each house an 11,356-liter (3,000-gallon) water tank, a 1,590-liter (420-gallon) foam tank, and a 7,570 lpm (2,000 gpm) water pump, along with a 250 kg (550 lb.) dry chemical powder system. Accelerating from 0 to 80 kph (0 to 50 mph) in under 25 seconds, the Striker Volterra ARFF demonstrates a 28 percent improved acceleration compared to the standard diesel models when fully loaded. training, implementation, and service support Dave Archer said, “The collaboration between Oshkosh Airport Products and Airservices Australia marks a significant step forward in the aviation industry's commitment to sustainability." He adds, "We remain committed to a strong partnership, providing world-class training, seamless implementation, and unwavering service support to ensure these vehicles exceed expectations in the critical missions of ARFF crews.” By leveraging new technologies and innovations like Oshkosh Airport Products’ Striker Volterra ARFF hybrid electric vehicles, WSI will showcase the feasibility of low-carbon operations and set a new standard for airports worldwide.
Industry pioneer - AEI Cables has clinched a contract to supply its low-voltage power, control, and fire performance cables to a major extension of the Hong Kong Sports Institute. Working with its partners, Cornwall Contracting Co.Ltd, AEI Cables supplied the cables to the existing sports complex from 2011 to 2013. Extension features The major extension involves the facilities development building, which is located in front of the indoor swimming pool and rowing boathouse comprising a three-storey building area. This will feature a multi-purpose training hall, scientific conditioning facilities, a sports medicine center, sport psychology, sports biomechanics, sports nutrition, and monitoring center, and a sports residence area. Quality cabling The Hong Kong Sports Institute is a major sports complex located in Sha Tin Stuart Dover, General Manager of AEI Cables, said, “This is a major development of the institute and we’re thrilled to be working on such a prestige project with our partner to ensure the highest quality of cabling is installed.” The consultant engineer will be WSP Hong Kong Ltd and the electrical sub-contractor is Cornwall Contracting Co. Ltd. The Hong Kong Sports Institute is a major sports complex located in Sha Tin, New Territories, Hong Kong, offering training to athletes and academic qualifications in the field of sports training. Fire performance cabling Using the very latest in technology and science, AEI Cables’ specialist Firetec Total Fire Solutions range offers enhanced fire performance cabling, accessories, and technical support from its distribution facility at Washington, Tyne and Wear. Applications for Firetec include residential and commercial buildings, shopping malls, airports, and protected buildings ensuring that fire alarms, sprinkler systems, building monitoring, and security systems can continue to operate in a fire. All AEI Cables’ products are supplied with approvals from independent bodies including BASEC and LPCB. It also holds approvals from organizations including Lloyds, the MoD, Network Rail, and LUL and works to international standards around the world.
Firefighting is an extremely dangerous and demanding profession, both physically and mentally. However, help is at hand: Teledyne FLIR designed its K-series of professional yet affordable thermal imaging cameras to take the strain, assisting firefighters in navigating through smoky conditions while searching for hot spots and measuring temperature from a distance. The team at Solna Fire Station in Stockholm, Sweden, is a case in point, where the use of a FLIR K-series camera recently helped one of the team’s smoke divers save four lives in a city center fire. Greater Stockholm’s Fire Service Storstockholms brandförsvar (Greater Stockholm’s fire service), covers 10 municipalities in the city, including Solna, located just north of the center. When a recent large fire began downtown, Solna’s fire crew responded to the call. “We sent in two smoke divers, both with FLIR K-series cameras,” explains Tomas Bellander, a Firefighter and Instructor at Solna Fire Station with 22 years of experience. FLIR Thermal Camera Upon approach, his FLIR thermal camera showed what looked like an arm in the doorway" Tomas Bellander continues, “One smoke diver spotted an elevator with its doors slightly open. His instinct drew him towards the elevator and, upon approach, his FLIR thermal camera showed what looked like an arm in the doorway." He adds, "It turned out there were four people in that elevator, all of whom were saved by our smoke diver and his FLIR camera.” Smoke Diving Like any fire station, Solna has a range of conventional firefighting tools at its disposal but relies on FLIR thermal imaging cameras to locate fires and pinpoint anyone trapped or in need of assistance. However, while the main application for FLIR cameras at Solna Fire Station is smoke diving, the crew also uses its cameras as part of other rescue activities, such as locating people on train tracks or next to the water. FLIR K55 High-Performance “It’s a lot easier than using our own eyes and a flashlight,” says Firefighter - Simon Zettergren, adding “We can quickly see if there are any temperature shifts to detect human presence.” Zettergren says Solna Fire Station takes advantage of FLIR K55 high-performance thermal cameras, retaining two in each vehicle. Charging takes place inside the truck. “We typically deploy teams of two smoke divers: one with a hose and the other with a FLIR K55,” he explains. Easy Smoke Detection They display crisp thermal images on a bright LCD, helping Solna’s fire crew to navigate better FLIR K55 cameras allow Solna Fire Station to attack fires with a better strategy, maneuver through smoke more easily and save lives. They display crisp thermal images on a bright LCD, helping Solna’s fire crew to navigate better and expedite critical decisions. “A lot of thoughts go through your head when there’s a real fire,” says Tomas Bellander. Situational Awareness With Limited Visibility He adds, “You have to execute your strategy while simultaneously receiving commands from the lieutenant and making real-time judgments about situational awareness with limited visibility." Tomas Bellander concludes, "The stress factor is high, so you must call upon your equipment and training. If you can do that, the outcome will likely be positive.”
West Yorkshire Fire & Rescue Service (WYFRS) has selected edge control room solutions from Frequentis to enhance service delivery for the communities it safeguards through better resource allocation and coordination between emergency services when responding to emergencies. WYFRS WYFRS is the fourth largest fire and rescue service in the country, responsible for the safety of over 2.2 million residents and the protection of 800 square miles of land, covering five major metropolitan districts. The diverse landscape, which encompasses everything from vast rural countryside to towns and major cities, presents unique challenges: Frequentis' expertise in providing comprehensive control room solutions and dedication to delivering innovative technology to emergency service organizations has played a vital role in this successful collaboration. Efficiency, Communication And Resource Allocation We are aiming to enhance the efficiency of our emergency response even further, and improve communication" “By implementing the Frequentis systems, we are aiming to enhance the efficiency of our emergency response even further, improve communication and coordination among emergency responders, and optimize our resource allocation,” says WYFRS Area Manager, Scott Donegan. He adds, "Ultimately, this will enable us to be even better at protecting the millions of residents, the communities, and businesses we serve here in West Yorkshire." Cloud-Based Mobilizing Solution The contract marks a significant milestone in West Yorkshire Fire & Rescue Service's journey toward modernizing its control room capabilities. “By adopting the Frequentis Microsoft Azure cloud-based mobilizing solution, West Yorkshire Fire & Rescue Service will benefit from a comprehensive communication and incident management platform, LifeX, and unique-mobilization solution provided by our recent acquisition, Regola," says Andy Madge, Managing Director of Frequentis UK & Ireland. A System-As-A-Service Approach We continue to provide modern control room solutions for safety-critical customers" Andy Madge adds, "The 'System as a Service' approach aligns with the managed service requirements, eliminating conventional concerns and costs associated with ongoing IT management and security." He continues, “This partnering approach represents a significant step forward for Frequentis as we continue to provide modern control room solutions for safety-critical customers.” Computer-Aided Dispatch (CAD) system The new systems include a replacement Computer Aided Dispatch (CAD) system that is Emergency Services Network (ESN) ready, an Integrated Communication and Control System (ICCS) for seamless telecommunications, radio communications, and data communications, as well as a mobilizing system for efficient resource allocation to incidents. The implementation of these cutting-edge systems will enable WYFRS to respond even more effectively to emergency calls, whether the resources are mobile or stationed at various premises, and the mobilizing system will streamline the assignment of resources and personnel.


Round table discussion
Thermal imaging is an advantageous tool for firefighters on the frontline. As thermal cameras have become more compact and affordable, their availability has expanded, along with their usefulness. We asked our Expert Panel Roundtable: How does thermal imaging serve the needs of firefighters and how is it changing?
New tools and technologies are emerging that augment the efforts of the fire market to prevent and fight fires. Modern firefighting is benefiting from an ongoing sea change in technological capabilities, spanning equipment, electronic components, greater connectivity and firefighter monitoring, to name just a few. We asked our Expert Panel Roundtable: What technologies will have the greatest impact on the fire industry in 2021?
Products


Videos
Flammable Material Control: Manufacturers & Suppliers
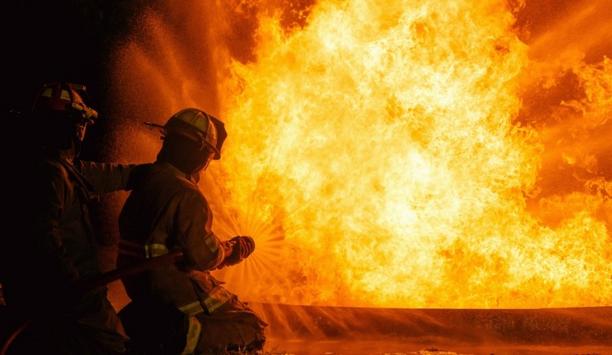
The New Future For Fire Agencies
Download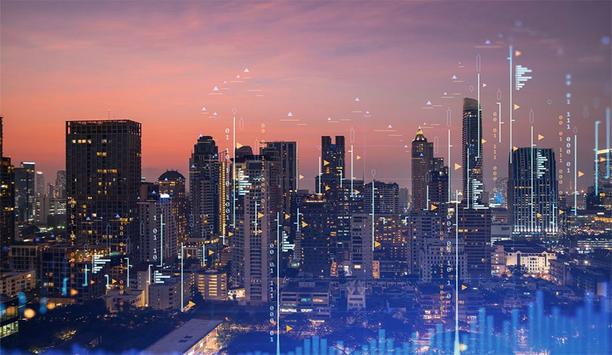
The Eight Key Trends in Fire Detection in 2023
Download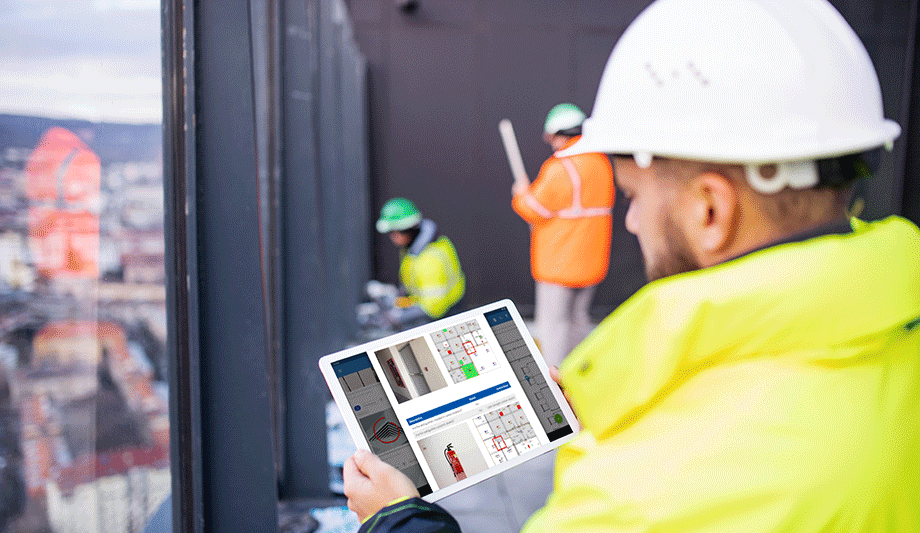
A Digital Platform to Improve Fire Safety Compliance and Inspections
Download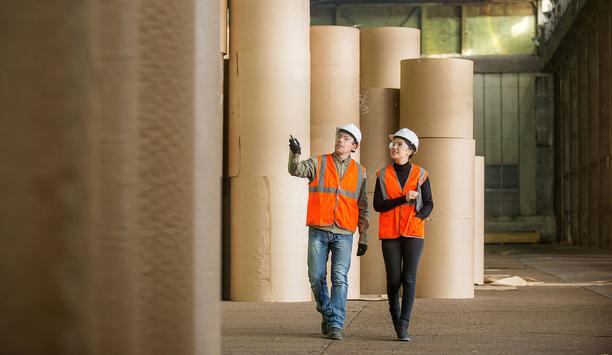
Overcoming the Challenges of Fire Safety in the Paper Industry
Download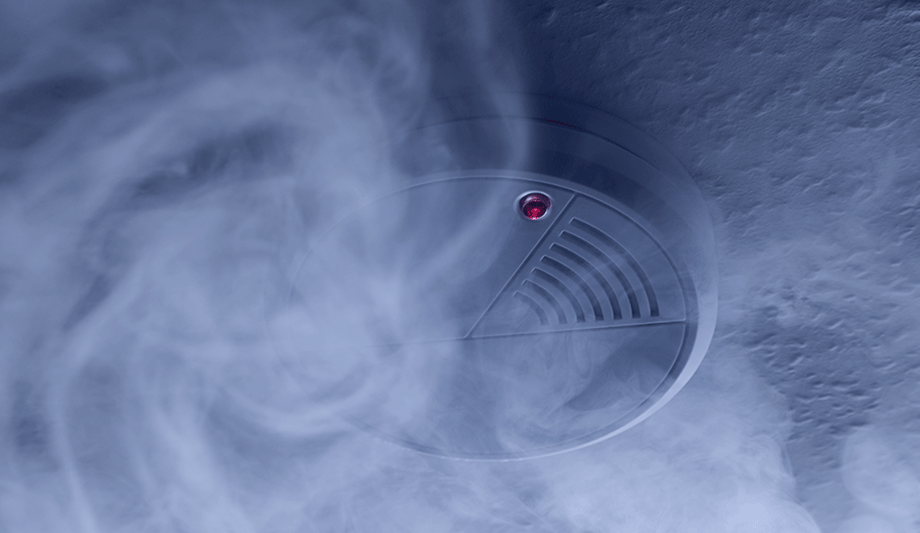
Carbon Monoxide: Creeping Killer Caught In The Act
Download