Explosion Protection
Lithium-ion batteries are at the heart of modern technology, powering everything from mobile devices to electric vehicles. However, they come with a significant fire risk. The newly released Collaborative Reporting for Safer Structures (CROSS) paper delves into the fire safety concerns associated with these batteries, shedding light on the phenomenon known as thermal runaway. This self-sustaining reaction can trigger large-scale fires or even explosions, often set off by overcharging, short cir...
Winds picked up on Tuesday in Southern California and at least a couple of new wildfires broke out as firefighters remained on alert in extreme fire weather two weeks after two major blazes started that are still burning in the Los Angeles area. Gusts could peak at 70 mph (113 kph) along the coast and 100 mph (160 kph) in the mountains and foothills during extreme fire weather that is expected to last through Tuesday morning. Ripe for explosive fire growth Wind speeds ra...
Baker Engineering and Risk Consultants (BakerRisk®), an employee-owned risk management consulting firm that specializes in process safety, structural and blast effects engineering, and research and development, is pleased to announce the acquisition of Haines Fire and Risk Consulting (Haines). Haines specializes in fire protection engineering, water supply analysis, emergency response planning, and fire/explosion investigations. BakerRisk’s commitment “This acquisition undersc...
Firefighters from several jurisdictions responded Wednesday evening to a massive blaze at an electric utility substation in north Fort Worth that apparently resulted from an explosion at the site, authorities said. According to a post on X, officials from the Fort Worth Fire Department said they were being joined by firefighters from the Saginaw and Roanoke fire departments to battle the blaze at the station, located at Seventeen Lakes Boulevard and Henrietta Creek Road. Work...
Industrial fires and explosions can have devastating consequences, affecting both people and property. While safety measures have improved over the years, understanding the root causes of these incidents remains critical for preventing them. They will highlight the primary causes of industrial fires and explosions and how proper fire safety measures can mitigate risks. Flammable Liquids and Gases One of the causes of industrial fires is the improper handling or storage of flammable liquids a...
The Q1 from Q-Fog is a new type of easily installed, enhanced fire protection system developed for existing living environments with a heightened need for fire protection. For example: for the elderly, vulnerable, people with dementia or handicapped in care institutions or in their own home. The product is specifically designed to offer a fire protection system that is reliable, simple and cost effective. The basic version of the Q-Fog Q1 offers active fire protection in a room of approx. 25 sq...
News
EU Regulation # 517/2014 sets out to control the use of HFC’s in the Fire Suppression Sector, and with FM200 / HFC-227ea being included in the Montreal Protocol (2016 Kigali amendment coming into effect in January ‘19), the long-term use of this Gas is not viable from either a financial, or ethical perspective. The phase-down of HFCs will culminate in 2030 at a 79% reduction from 2015 levels, impacting most HFC markets and applications, including fire suppression. Fire Suppression System The Solution - Switch to a non-HFC Fire Suppression System, such as Novec In addition, since 1st January 2021, Great Britain is a third country in respect of imports and export, meaning importers of FM200 from GB must now hold sufficient EU HFC quota for both New Systems and Service Exchange Cylinders. This makes maintenance and refilling existing FM200 Systems restrictive and costly. The Solution - Switch to a non-HFC Fire Suppression System, such as Novec. The Reason - FM200 has a global warming potential of 3,220 over 100 years, whereas Novec has Zero Ozone Depletion Potential and a Global warming potential of just 1. The cost to recover FM200 Gas will only ever increase. The ability to refill a system in the event of a discharge will be greatly hindered, and if possible – up to 6 times more expensive. Corporate Responsibility Environmental Sustainability. Authorized waste facility The Offering - Reduce the risk & carbon footprint in One Easy Transaction - KSS can provide a turnkey, cradle to grave Novec upgrade to their existing FM200 systems. KSS can provide an undertaking to transport recovered FM200 gas from the generator site to an authorized waste facility by way of a valid Prior Annual Notification (PAN). KSS can provide FM200 recovery to a facility authorized under the Waste Management Act 1996 (as amended). The facility holds a Waste Certificate of Registration for the recovered FM200 so users can rest assured knowing they are complying with all EPA & European F-Gas Protocols & Regulations.
The principle of all Trace Tube Fire Suppression Systems is a simple self-activating system that offers the widest versatility, which results in an excellent cost/performance balance. Trace Tube Systems can be used in a range of applications, with the principals remaining the same; Stop The Fire Where It Starts. Electrical Panel & Switchgear Fire Suppression Electrical Panels & Switchgear Fire Suppression Tumble Dryers Plant & Machinery fire suppression Fume Cabinet fire suppression CNC & EDM Machinery Wind Turbines Agricultural Machinery Cars/Vans/Trucks–including Motor Sport Rail & Dockside Detect Fire Quickly & Accurately These systems use linear detection tubing, which is installed throughout the asset it’s covering & can not only quickly and accurately detect a fire, but also suppress it before it can damage adjacent components. Simple Solution To A Complex Fire Problem These systems do not need complicated electronic detectors or panels and operate simply pneumatically. This alleviates the need for separate power supplies or battery backups and also makes the entire system fail-safe with minimal moving parts. We offer a choice of extinguishant agents, such as Novec, CO2, Powder, and FM200, some of which can be used safely in the knowledge that they will not damage the electrical components or leave a residue.
Euralarm has published a new guidance document on the impact of high airflow and hot/cold aisle containment on the performance of gaseous fire extinguishing systems in data centers. The new guideline is aimed at fire system designers, IT managers, and operators of data centers. Euralarm’s guidance document Recent industry research explored whether contemporary cooling methods and the continued movement of air, common to modern data centers, had any impact on the performance of gaseous fire extinguishing systems, and whether this effect was good or bad. Euralarm’s guidance document aids the interpretation of the research, will help the European market foster a practical application of its findings, and complement the conclusions at the back of the report. Protecting Information Technology Equipment (ITE) Protecting ITE from fire while also safeguarding its continued operation is paramount to businesses Protecting ITE from fire while also safeguarding its continued operation is paramount to most businesses nowadays. Gaseous fire extinguishing systems, using clean agents, are principally used to protect critical ITE. With a need for 'high availability', this now includes throughout the full fire scenario and for as long as the ITE is expected to operate. The exponential growth of data The exponential growth of data and the need for more processing power brings challenges of heat generation and demands improved and more efficient cooling. With data centers commonly having complex and targeted airflow that cannot be shut down even during a fire incident, it is important to know how to better engineer a fire protection system. New guidance document The Euralarm guidance document explains the research and signposts the reader to salient parts of the full report while discussing practical applications of its findings. Copies of the new guidance document on the impact of high airflow and hot/cold aisle containment on gaseous fire extinguishing system performance in data centers are available in English, Spanish, and French on Euralarm’s website. The German version is expected shortly.
E2S Warning Signals has introduced the new H1 range of heat detectors. Globally approved to UL, cUL, IECEx, and ATEX standards with explosion-proof, flameproof, increased safety, and intrinsically safe protection, the H1 range is available as part of the D1x and D2x families with marine grade, copper-free LM6 aluminum termination enclosures, in the STEx family with 316L stainless steel enclosures and the GNEx with GRP enclosures. UL521 and CAN/ULC-S530 approved The H1 range contains Ex db flameproof, Ex db eb increased safety, and Ex ia intrinsically safe variants approved for use in Zone 0, 1, 2, 21, 22 and Class I/II Division 1 and Division 2. They are UL521 and CAN/ULC-S530 approved and SIL2 compliant to IEC61508 (2010). heat detection in hazardous areas The highly reliable and robust H1 range provides initial heat sensing in automatic fire and gas detection The robust E2S termination enclosures are combined with heat detector elements as a completely approved assembly to create a fully certified solution for heat detection in hazardous areas. Primarily used for signaling overheating or fire conditions, the highly reliable and robust H1 range provides initial heat sensing in automatic fire and gas detection and suppression systems. D-A-F rate-compensated heat detector Incorporating industry-standard Detect-A-Fire® (D-A-F) rate-compensated heat detector elements that feature stainless steel housings and hermetically sealed contacts the H1 range is available in a wide range of operating temperatures. All versions feature IP66/67, Type 4/4X/13/3R sealing for the harshest of environments, and an optional protective guard for the element. availability and advantages Selected variants can be specified with an LED to indicate an alarm condition and a wide range of addressable modules can be factory-installed. Full details of the advantages of the E2S H1 rate-compensated detectors can be found on the E2S website and the advantages over traditional fixed or rate-of-rise detectors can be found in the associated Technical Bulletin.
Why is this required - Under IS EN 1968 2002: Annex B, the Pressure Testing Interval for Fire Extinguishing media, used for Emergency Purposes is 10 years. Who is responsible - The Owner or End User of the Fire Suppression System is responsible and should ensure that their Fire Suppression Cylinders are pressure tested prior to the 10th anniversary of the cylinder's original test date. This means that fire suppression cylinders should be pressure tested every 10 Years. What is Service Exchange - Service Exchange eliminates downtime for fire suppression systems, ensuring unbroken protection for your valuable assets. KSS will bring pressure-tested full cylinders to the chosen site and swap for the out-of-date or empty cylinders. Contact them with the specific cylinder type and they can advise if they can service exchange them.
KSS Fire Suppression is delighted to announce the exciting Partnership with Grenke. Since 1978, GRENKE has been helping businesses grow through offering smart finance solutions, allowing the freeing up of capital & improvement of cash flow. This synergy means that KSS Fire Suppression Solutions can now be leased, offering a level of flexibility that allows them to focus on what's important - Growth. Flexible solutions can be tailored to the company's needs, meaning: No large capital outlay, they can afford the system their business requires. Repayments are fixed, so they can keep cash reserves in the business. Three to five-year leases to suit them. Service and maintenance can be incorporated within agreements. Easy to upgrade or expand the system throughout the lease.


Expert Commentary
As a company officer, the day will come where you and your crew are first to arrive at what looks like the beginning of a major incident. Your Battalion Chief (BC) is delayed or diverted to other incidents, so YOU are the Incident Commander (IC). How you set the table for this incident with regard to quickly setting up the Incident Command System (ICS) is critical. And how you use your channels of communication, including the ways you communicate, will be crucial to your success. Before we jump into the ‘how-to’, let’s examine something that looms over everything we do during emergencies, especially fires - ‘The NIOSH 5’. I first became aware of the NIOSH 5, when listening to one of Anthony Kastros’ lectures on incident command and the need for an organization on the fire ground. ‘The NIOSH 5’ Firefighters and emergency workers typically get lost, hurt, or killed at incidents, when any one of five causal factors identified by The National Institute of Occupational Safety and Health (NIOSH) are present: Improper risk assessment Lack of incident command Lack of accountability Inadequate communications Lack of SOPs (or failure to follow established SOPs) Statistically, 50 percent of these line-of-duty deaths (LODDs) and injury events occur in the first 15 minutes of an incident. Half of those occur in the first three minutes! If you’re the initial IC, it’s statistically likely this could happen while you’re in charge. Need for training and practice in handling emergencies Keeping ‘The NIOSH 5’ at the forefront of your mind should trigger the need for training and practice in handling emergencies. Although there are factors you simply can’t control during an emergency, you can control communications, incident command, accountability, repetitive training, and standardization. The following are some things to keep in mind while managing an incident: Arrival on Scene In incident management, setup is everything and oftentimes, determines the outcome of the incident. To use a sports analogy, you definitely want your first pitch to be a strike. So how do you do that? Provide a Solid Size-up Clear and concise on-scene conditions reports set the tone for any incident and establish solid communications The first step is taking a deep breath and giving a good size-up. Clear and concise on-scene conditions reports set the tone for any incident and establish solid communications, and a command tone. Your tone and tempo in your size-up will help focus everyone and create a tactics-driven incident, rather than an emotions-driven one. But, if we’re being honest, being cool takes practice and repetition. Your agency should have a standardized way for how and when this size-up is delivered. In many cases, it’s a fill-in-the-blank script that includes the following four things: What you see (smoke and flames/or nothing showing) The area you see it affecting (the second story, the alpha/bravo corner) What’s happening/what’s on fire or causing the hazard (a two-story home or a sedan next to a building) Establishing command (a must-take command or pass, if you’re going to rescue a citizen) By practicing within your agency’s standards, it enables you to project a cool tone over the radio like you’ve ‘been there before. Order resources early and often Tunnel vision is a death sentence for any IC. In most cases, this is not the time to get sucked into task-level problems. The exceptions to this are structure fires and other emergencies where there is an immediate and known rescue. Otherwise, it’s time to step back, take in the big picture, and make decisions as an IC. Ask yourself: ‘What will this incident do in five minutes? 10? 20? One hour?’ If the answer is ‘get bigger’, then you need more resources. Order them early and often, because they can always be turned around. Don’t try to do too much with too little. Trusted Incident Command System equals early accountability As the initial IC, you’ll be sending crews into the hazard zone. It’s a red flag if, during the initial portion of the incident, you don’t have solid accountability. It’s during this initial ‘fog of war’ that we lose track of crews, and it’s when personnel gets hurt or killed. NFPA 1561, along with other best practices, requires that you know where everyone is and what they’re doing. If you don’t have that knowledge, stop and figure that out, or assign someone to figure it out and report back to you as soon as possible. Benefits of an all-in-one digital platform - Tablet Command Many agencies require the first-arriving officer to implement some form of an ICS to track crew Many agencies require the first-arriving officer to implement some form of an ICS to track crews – a notepad, whiteboard, tactical worksheet, or better yet, a digital command board. The huge advantage of an all-in-one digital platform like Tablet Command is that it’s CAD-integrated and will populate resources for you in real-time. There’s no writing and scribbling while listening to garbled radio traffic, and no trying to ‘catch up’ with resource orders that change on the fly. Accountability integrated into command processes With a platform, such as Tablet Command, all you’re doing is dragging and dropping resources into their assignments, which automatically time-stamps their activities. Maintaining accountability becomes seamlessly integrated into your command processes. These digital platforms also tend to be highly recognizable and easy for others to assume command. It’s paramount that you train extensively on whatever system your agency uses, and that everyone in your region or agency is squared away on how to maintain accountability in a standardized fashion. It’s a problem if you have several chiefs and company officers, and too many (or not enough) ways of maintaining accountability. Many agencies need the first-arriving officer to implement an ICS to track crews Segment and subdivide How do you eat an elephant? One bite at a time. Use your knowledge of your ICS to break up the incident into manageable bites. When the Fire Chief arrives, they’ll have simple questions: Where is everybody? What are they doing? How are they doing? How do I talk to them? Knowing where your people need to deploy and what channel they’re on are critical to accountability. Using the command board is a great way to have all of those questions answered. Using divisions, groups, or sectors can make your life easier in this regard, especially as an incident grows rapidly Using divisions, groups, or sectors can make your life easier in this regard, especially as an incident grows rapidly. This is true because it ensures you’re talking to the supervisors of each segment of the emergency, especially when assessing conditions, actions and needs. Setting up an incident this way should also be an expectation that is agency-wide and practiced in scenario-based training. The terminology should be standardized so that your agency and neighboring agencies aren’t interpreting what you’re trying to accomplish in the heat of battle. Summary A clear communications plan, solid scene size-up, and early establishment of the ICS by company officers are critical to incident success. Combine this with accurate and solid accountability systems, either through analog methods or with a modern digital solution in real-time, and you guarantee safer outcomes for your crews. The best way to be prepared is through long hours of dedicated practice in the command role and, more importantly, an agency-wide understanding of what’s in the play book: Standardization! A standard approach to managing incidents will help you remedy the chaos and enable you to hand over a well-organized incident to the first-arriving Chief.
There’s no doubt the Building Safety Act and Fire Safety Act are driving major improvements in the construction industry’s quality and approval processes. Although the initial focus of the legislation is on high-rise residential buildings, it’s predicted to be rolled out across the entire sector soon, tightening fire safety regulations in hospitals, hotels, and commercial offices and we await the rafts of secondary legislation that will really redefine the regulatory landscape. Many fear that commercial real estate professionals will be unprepared for the higher levels of compliance required, by the incoming regulations. New requirements for competency, collaboration, and digitally presenting joined-up information will inevitably be imposed on architects, building inspectors, owners, and construction product manufacturers. Fire regulations for commercial buildings However, currently, fire regulations for commercial buildings remain lax and there’s ambiguity about what constitutes appropriate fire safety system management, as well as how to prepare for revised building and fire safety requirements, as they become available. It’s all too easy to take a laissez-faire attitude, but adopting an ‘it will never happen to me’ approach is likely to lead to problems down the road, so contractors, asset owners and FMs alike need to get with the legislative program and fast. Understanding of fire safety ratings for things to increase If specifiers are cutting corners and installing inadequately rated products today, there will be very costly consequences later It is certain that office interior specification, coupled with ongoing checks and a robust understanding of fire safety ratings for things, such as interior doors, panels and partitions is likely to be increasingly challenging going forward. Importantly, if specifiers are cutting corners and installing inadequately rated products today, there will be very costly consequences later. As a result, it is advisable to go above and beyond current construction regulations, when specifying materials for commercial office interiors, in order to future-proof and keep occupants safe. The Grenfell turning point Grenfell was a wake-up call for the construction sector, particularly for construction product manufacturers and those involved in fire protection and fire testing. Before the tragedy, many believed their products were safe and their methods were flawless and tested according to official guidelines. However, this terrible event compelled the industry to examine its manufacturing procedures, the efficacy, adequacy and relevance of testing and certification, as well as product performance claims made in marketing collateral. This re-evaluation, which found many parts of the specification process not fit-for-purpose, has, thankfully, culminated in a total cultural overhaul. Asking important questions regarding building fire safety Fundamentally, there was not enough questioning before Grenfell. Now, we’re re-thinking everything, asking ourselves: Are we doing things correctly? What’s the risk? How can we mitigate that risk? Five years on, the interpretation of evidence, whether direct fire test evidence or third-party assessment, has become much more refined, and rightfully so. Designers and contractors are paying more attention to the evidence used to support proposed items and applications, while manufacturers are re-thinking their use of evidence, in line with post-Grenfell thinking. Adequacy of test evidence The adequacy of test evidence for a given application is now being scrutinized much more closely The adequacy of test evidence for a given application is now being scrutinized much more closely, as are the testing methodologies. It now raises the important question: ‘Does this test accurately represent the effect in a real-world scenario?’ Unfortunately, the capacity to deliver on these questions is not matching good intentions. The rising need for test evidence of fire resistance rather than merely accepting an assessment has caused testing facilities to become overloaded, resulting in much longer wait times. Assessments are now heavily connected to appropriate fire test findings, which necessitate the gathering of evidence and a higher level of analysis, in order to provide assessments. The entire process has become necessarily more complicated, but this has affected efficiency, something which will need to be addressed as construction output inevitably increases. R&D cultivates innovation Fortunately, there are solutions within reach, thanks to significant advancements in the development of fire-safe products and materials across the industry. There’s been an increase in project-specific developments, as suppliers collaborate with designers and fire regulatory organizations to share their expertise. As a result, rather than merely installing the best fit, projects are now specified with fully customized fire-rated systems. Meanwhile, continuing R&D has led to many organizations looking ahead and anticipating shifting demands and trends in the built environment. It’s leading to additional testing and product development for applications that aren't already covered by existing technologies, and a commitment to the highest-quality fire solutions, meaning safer and higher-performance products. Expertise and training are key It’s important to note that choosing fire-rated products does not make the area fire-safe by default. Once the facility is in operation, a systems approach is needed to ensure that the installation and risk assessment of fire-rated products are periodically monitored. Extensive training and CPD must be taken into account for specifiers Even the slightest modification to a fire-rated product, such as changing a glass door’s opening system, might compromise its integrity. It’s critical to completely understand the ins and outs of the product being defined, in order to ensure that it's used correctly. As a result, extensive training and CPD must be taken into account for specifiers and office building managers alike. Increased training and CPD Increased training and CPD will keep the industry on track to deal with the level of comprehensive knowledge necessary Increased training and CPD will keep the industry on track to deal with the level of comprehensive knowledge necessary, specifying according to need and meeting the high standards of the near future. Continued development of fire knowledge is crucial, as the latest high-performance glass doors in offices today are specialized pieces of technology and fire-rated systems behave very differently from other glass partitions or doors. The design dilemma Another significant challenge is incorporating fire safe components into a space without losing its aesthetic appeal, but remaining compliant. Designers are increasingly aiming to open up space to bring in natural light and encourage a sense of well-being for the occupants, meaning walls that would previously have been solid are being specified as glazed. This means that large panels of glass, beyond the capacity of fire test facilities, must be handled sensitively and installed within a bespoke system. This necessitates close liaison with certification authorities to identify what can be assessed from the test evidence provided. Of course, workplaces must be fire safe, look good, and feel pleasant to work in. The sheer complexity of the day-to-day office functionality is a difficult issue. Aesthetics are often a requirement that is added to the fire resistance of fire doors. But it’s often the case that suitably certified hardware simply doesn’t exist. Glass office partition systems Can fire safety and great design coexist in the office space? Yes, definitely. Can fire safety and great design coexist in the office space? Yes, definitely. This is because, the latest glazed and sliding doors, adjustable ‘office pods’, and acoustically-optimized walls are all made with fire safety, sustainability, and elegant design in mind. Many glass office partition systems allow natural light and air circulation to flow through the room, which helps to improve employee well-being and boosts performance. Fire safety is of the utmost importance Fire safety and design can harmoniously co-exist in an office space, but it comes down to managing expectations. Fire safety is of the utmost importance, and as the requirements tighten, the commercial office industry will catch up with fire safety standards, testing and reporting regimes, and ongoing compliance. Fortunately, fantastic fire-resistant workplace solutions are entering the market, built for safety, flexibility, and aesthetic appeal.
Last year was the largest wildfire season recorded in California in modern history, with six of the top 20 largest wildfires in the state, according to the California Department of Forestry & Fire Protection (CAL FIRE). In 2020, firefighters faced a total of 9,917 wildfires that consumed a record 6,653 square miles. These fires took the lives of 33 people and damaged or destroyed 10,488 structures. Ahead of the 2022 wildland fire season, climatologists are predicting another record-shattering year of frequent and intense wildfires across the United States. This reflects a continuing trend of more wildfires and more acres burned, with seasons that are more severe and last longer. Growing concern for WUI firefighters DuPont believes these dedicated men and women deserve the best protection Concern is growing for wildland urban interface (WUI) firefighters as fires today frequently intersect with residential areas, in and around wildland fields. WUI firefighters are fighting both wildfires and urban fires. This comes with combined hazards and the clear need for their gear to work harder than ever before. DuPont believes these dedicated men and women deserve the best protection and the best gear to match their unwavering commitment to keeping everyone safe. At DuPont, we look at singular and multiple threats simultaneously. Our decades of experience, wide portfolio of solutions and unique partnerships with firehouses around the world, allow us to continue to innovate our next-generation gear to face emerging threats. Uncompromised Protection The DuPont Nomex brand has been trusted for over 50 years. WUI firefighters can depend on apparel made with Nomex and Nomex Nano to offer higher fire resistance along with over 99% particulate protection in lighter weight options. Nomex Nano was developed to address the growing problem of heat stress. It is engineered to be thinner than other advanced flame-resistant (FR) materials used for thermal liners and features a higher limiting oxygen index (LOI) than traditional Nomex and DuPont Kevlar. Nomex Nano We have seen Nomex Nano provide up to 40% reduction in thermal liner thickness, when compared to other advanced liners available in the market, while providing similar thermal protection performance. By reducing the weight and bulk of current turnout gear (TOG) systems, liners made with Nomex Nano can help give firefighters increased mobility and a better range of motion, thereby helping to reduce fatigue, disorientation and heat exhaustion. Reduced heat stress and enhanced moisture management Nomex Nano also helps reduce heat stress due to its enhanced moisture management Nomex Nano also helps reduce heat stress due to its enhanced moisture management, which includes a high absorption rate to remove sweat quickly and a high evaporation rate to drive water out of a firefighter’s skin and the thermal liner system. Kelly Whitt, Business Development Manager at DuPont said, “Our existing products have been proven with years in the structural firefighting arena. Today, we’re looking at ways to bridge the gap and give WUI firefighters the same level of protection from harmful smoke particulates that can be found in structural fire turnout gear.” Field test of new laminated composite fabric technology Kelly Whitt adds, “We are field testing a new laminated composite fabric technology – utilizing Nomex® Nano – that will provide superior particulate protection for both wildland-urban interface and brush fire firefighting.” DuPont understands that collaborating with a variety of stakeholders is the key to taking the technology to the next level and providing WUI firefighters with a better level of protection, than what they have previously experienced with traditional wildland gear. Game-changing barrier protection Scientists are just starting to learn more about what firefighters are exposed to, when they are battling a wildland blaze. They know that a variety of airborne pathogens get kicked up in a fire. They have tracked countless living microbes and airborne pathogens that could seep into the skin, enter lungs and cling to clothing. But the long-term effects of wildfire smoke aren’t really known, as fires haven’t burned for this long until recent years. At this point, experts don’t have a good understanding of the many trillions of microbes that survive and proliferate in wildfires. “The diversity of microbes that we've found are really mind-bending,” said Leda Kobziar, the University of Idaho’s Wildland Fire Science Director. The addition of Nomex Nano Flex to a firefighter hood composite structure Enhanced protection against particulates As we look to the next generation of gear, we want to focus on increasing protection against particulates. We know that when added to a firefighter hood composite structure, hoods made with Nomex Nano Flex provide higher than 99% particulate, bacterial and viral filtration efficiency, without compromising on comfort. The addition of Nomex Nano Flex to a firefighter hood composite structure provides improved particle barrier protection in the neckline and upper jaw. These are areas that are known to be the most vulnerable and least protected. In fact, it results in up to a 4x increase in particle barrier efficiency. And comfort doesn’t take a back seat. Better situational awareness and high breathability “I speak with firefighters daily, and they tell me hoods with Nomex Nano Flex have exceptional durability,” said Chris Nowacki, Regional Sales Manager – Emergency Response and Utility/Arc at DuPont, adding “In addition, fire departments specify Nomex Nano Flex over other particulate-blocking materials for enhanced safety, better situational awareness, high breathability, low shrinkage and enhanced performance, when soaked with perspiration.” Protection That Lasts Tests show that hoods and composites made with Nomex Nano Flex offer 99% particulate-blocking efficiency Tests show that hoods and composites made with Nomex Nano Flex offer 99% particulate-blocking efficiency, which is four times better than conventional hoods, even after 150 washes. To further validate the durability of the hoods, a test was performed at two local fire stations using hoods from three different manufacturers with different designs, including quilted and non-quilted options. Nomex Nano particulate-blocking gear Each trial consisted of 250 cycles of donning and doffing, followed by one NFPA 1851 recommended washing and drying for 10 cycles. Despite these aggressive trials, the hoods maintained their protective performance. Nomex Nano particulate-blocking gear helps prevent crews from being exposed to particulates and aerosolized microbes. At DuPont, we are committed to continuing our work with our industry partners to leverage our proven technologies and push the boundaries of science so that the next generation of WUI firefighting gear offers the highest level of protection possible. We are the innovation partner and ingredient. We stay with partners throughout the entire process of adoption and make sure the end user also has what they need to be safe and successful in their jobs. Our heroes deserve it.
Editor's Dispatch
As motor vehicle designs evolve, including the addition of lithium-ion batteries, for example, firefighters and first responders must also adapt. They need information about the vehicle’s fuel and energy usage and guidance on extricating occupants following an accident. Emergency Response Guides (ERGs) can help responders by using standardized labels, colors, symbols, and graphics to make emergency information more complete, accurate, and accessible during training and response. ISO 17840 ISO 17840 is an international standard that ensures first and second responders have fast and easy access to the information they need to perform their lifesaving duties in case of an automobile fire or accident. The ISO 17840 standard includes a template layout of ERGs to provide necessary and useful information about a vehicle involved in an accident. in-depth information The goal is to shorten the "golden hour" and quickly identify the energy source and hidden hazards on any vehicle The guide can be communicated in paper or electronic format. The goal is to shorten the "golden hour" and quickly identify the energy source and hidden hazards on any vehicle. The standard supports the team to rescue as many occupants as quickly and safely as possible. ERGs also provide in-depth information about fire, submersion, and leakage of fluids. New vehicle hazards Changing hazards of newer vehicles include propane- and LPG-powered vehicles that can explode more powerfully if tanks are heated, and fuel bottles that can become projectiles. Also, electric and hybrid vehicles have high-voltage batteries and electrical wiring that can electrocute first and second responders and victims if not properly disarmed. Furthermore, hydrogen and other fuel cells produce toxic and flammable gases that behave differently than gasoline or other traditional fuels. ERG template The ERG template follows in principle a flowchart for the main actions of first and second responders arriving at an accident scene. The template provides relevant information for a vehicle involved in a traffic accident (including immobilization, disabling of hazards, access to occupants, shut-off procedures, and handling of stored propulsion energy). Standardized colors and pictograms make it easier for first and second responders and vehicle manufacturers to understand each other. Information on the ERG is linked to the “rescue sheet” (ISO7840 parts 1 and 2) to inform training and development of rescue procedures. The headings/content of the rescue sheet and the ERG are aligned. knowledge and preparation Public safety organizations can download free examples of ISO 17840 templates for creating rescue sheets International Technical Committee for the Prevention and Extinction of Fire (CTIF), the European New Car Assessment Programme (Euro NCAP), and the Swedish Institute for Standards (SIS) created the ISO 17840 standard. With more alternative fuels and propulsion systems entering the market, more knowledge and preparation are necessary in order to approach an accident scene safely. Public safety organizations, educational organizations, and first and second responders can download free examples of ISO 17840 pictograms, templates for creating rescue sheets for any vehicle, and other information to create ERGs for training purposes and as guides for local rescue procedures. recommendations of ISO 17840 Among the vehicle manufacturers who have complied with the recommendations of ISO 17840 are Honda, Hyundai, Mitsubishi, and Volkswagen. In addition, another dozen or so manufacturers are progressing on the road to compliance, including BMW, Ford, General Motors, KIA, Nissan, Subaru, Tesla, and Toyota. The National Fire Protection Association (NFPA) maintains a collection of emergency response guides, and most manufacturers have posted their updated ERGs on their websites.
In Ann Arbor, Michigan, USA, in May 2022, a helmet camera recorded firefighters extinguishing a truck fire along I-94, catching every detail as sparks flew and firefighters hosed down the truck to suppress the blaze. Firefighters also hosed down the grass on the side of the freeway to put out hot spots and prevent a grass fire, MLive.com reported. The helmet-cam was part of a voluntary program that involves Ann Arbor firefighters wearing cameras when responding to active structure fires to capture video that can be used as a training tool, in order to better understand what went right and what went wrong. Video can also be released to the public to showcase how tax dollars are being spent. A focus on structure fires precludes any concerns about privacy. Helmet-cams used by firefighters Helmet-cams used by firefighters can provide a valuable tool for training and post-incident analysis Helmet-cams used by firefighters can provide a valuable tool for training and post-incident analysis. On the other hand, they could impact how a firefighter does his or her job or even violate privacy concerns and/or the public trust. While debate around the use of body-cams by law enforcement officers has mostly been settled, opinions still vary about the use of helmet-cams by firefighters. In one sense, the rules and regulations have not caught up with the technology, including smaller (and inexpensive) video cameras that can easily (and even discreetly) be mounted on a firefighter’s helmet. Some departments have banned use of helmet-cams, while others have sought to restrict and control their use. Still others haven’t given it much thought. Multiple perspectives for post-incident analysis An advantage of helmet-cams is to record video of the actions of officers and firefighters at an incident and to provide multiple perspectives for post-incident analysis. Critiquing performance is a learning tool to encourage continuous improvement. In case of an injury or line-of-duty death (LODD), helmet-cam footage provides an unblinking record of exactly what occurred. If a time element is being assessed, a helmet-cam video can display each activity along with a time display, thus eliminating the need for a stopwatch. Clear and time-marked audio recording In addition to video, helmet-cams can provide a clear and time-marked audio recording, not limited by radio-frequency interference. (Audio recordings are subject to additional privacy concerns in some jurisdictions.) A possible downside of using helmet-cams is to distract a firefighter from his or her duties or to narrow their focus to the detriment of a broad awareness of their surroundings. It is important that a firefighter not miss something that is happening at the periphery of his or her line-of-sight. Helmet-Cams can distract a firefighter’s attention Conscious of how they appear in a video recording, a firefighter might be more guarded in their actions or words; at the other extreme, they might be tempted to “show off” for the camera by taking greater risks to provide more dramatic footage. A firefighter with a helmet-cam might also become preoccupied with operating the camera to optimize video to the detriment of other concerns. Becoming fixated on the technology can distract a firefighter’s attention from the real job at hand. Creating a policy that addresses issues are helmet-cams use Departments should consider carefully the issues surrounding helmet-cams and create a policy Departments should consider carefully the issues surrounding helmet-cams and create a policy that addresses those issues. Fire service leaders may benefit from collaborating with local police leaders who have worked with body-cam video and know the possible evidentiary value of video that can be captured on the devices. Fire departments should be aware that any captured footage may have evidentiary value, if it relates to a crime or police internal affairs investigation. Unlike body-cams used by police, which download video to the department at the end of a shift and are covered by department policy, helmet-cams are less restricted and less well-managed. Firefighters may even own their cameras. Privacy concerns surrounding the use of helmet-cams Some fire departments, such as Houston, San Antonio, and San Francisco, have banned helmet-cams because of privacy concerns and worries about how a video might embarrass a department. Privacy concerns include the use of helmet-cams in medical calls, which make up most a firefighter’s daily responses. There should be rules that ensure that videos do not eventually make their way to Internet sites such as YouTube. In New Jersey, for example, Cathy’s Law (passed in 2012) restricts images and recordings at emergency scenes, such as motor vehicle accidents.
Among the ways, garments protect firefighters is by reducing the heat stress and discomfort created by the need to carry heavy gear. Making the garments more comfortable to wear means less physical stress. Garments also help to protect firefighters from the toxic elements in the fire environment. The extent to which plastic materials can generate toxic smoke when they burn has previously been ignored but is now better understood. Concerted effort to understand end user As a manufacturer of fibers used in firefighting garments, DuPont makes a concerted effort to understand the end user of their products; that is, the firefighter. They seek to keep the firefighter safer and to extend the time available to do his or her job safely. DuPont works with fabric and garment manufacturers to focus on minimizing the impact of the toxic environment. Firefighter’s awareness Multiple initiatives seek to make firefighters more aware of potential dangers and best practices Awareness by firefighters of the negative impact of toxic materials has increased substantially. Multiple initiatives seek to make firefighters more aware of potential dangers and best practices to avoid exposure to contamination. Organizations promoting greater awareness include firefighters’ unions, the International Association of Fire Chiefs (IAFC), and the National Fallen Firefighters Association. Toxic smoke For example, testing confirms that toxic smoke often affects firefighters in the neck and jaw area, where sweat promotes absorption of smoke particles. A woven hood or baklava avoids the absorption, reflected in the NFPA Standard 1971, which makes particulate protection hoods mandatory. The Nomex Nano Flex hood increases the comfort of the gear. Avoiding toxic materials also includes no inclusion of per-and poly-fluoroalkyl substances (PFAs) in garment materials themselves. Standards and Specifications Testing is an area of focus for DuPont, which has the capabilities to test the layered structures firefighters are wearing. One tool is the Thermo-Man, a fully instrumented mannequin that tests the likely burn injuries of flash-over fires. DuPont works with the NFPA, ISO, EN, and other standards committees to develop testing and certified standards to ensure the performance of firefighter garments. Fire gear is specified in each region according to a standard (minimum) performance. In many cases, garments out-perform the requirements. Other variables Other variables of firefighting garments include the fitting and weight Other variables of firefighting garments include the fitting and weight. A less expensive approach might yield a garment that sacrifices comfort. Geographic and climate differences matter, too. A firefighter in the North would prefer a different garment than in the South. Garments should be comfortable, lighter, and warmer in cold environments. On the topic of gender, garment makers offer female designs that are cut and shaped differently. Garment makers evaluate the weight of the assembly, how well it protects against the heat, and the comfort. DuPont works with garment makers to test various materials and how they perform in fire garments. The company works with firefighter consultants in the U.S. and Europe who help them understand the language of firefighters. Addressing Dangers of Toxic Materials Cleaning fire gear of toxic materials is a challenge related to garments. Toxic materials on fire gear returned to the fire station can also expose the station environment to danger. Changing logistics and processes are driving how gear is handled in the fire station environments. Some stations are designating black zones, gray zones, and white zones, depending on the level of contamination of the gear in those areas. Washing and drying More frequent washing of bulky, heavy gear helps to circumvent the impact of toxic materials, but repeated washing and drying can cause mechanical stress and resulting damage to a garment. DuPont collaborates with weaving mills and garment makers to develop fabrics and garments that stand up well to frequent washing.Toxic smoke particles and mandatory use of hoods on firefighters is translating into more washing. As time goes on, the washing and decontamination process will likely become more professionalized with laundry companies stepping in to wash and handle the garments. Fire stations are not well suited to cleaning these garments. Nomex Nano fiber Nomex Nano Flex is a non-woven material that retains toxic and cancer-causing particles Developed to address the growing problem of heat stress, DuPont’s Nomex Nano fiber is engineered to be thinner than other advanced flame-resistant materials. Nomex Nano Flex was developed to help make products like firefighter hoods more protective against particles without compromising comfort. Nomex Nano Flex is a non-woven material that retains toxic and cancer-causing particles, and creates a particulate barrier. It also protects the firefighter from outside heat while cooling the firefighter by evacuating body heat. Higher evaporation rate Nomex Nano Flex has a higher evaporation rate. For the same thermal protection performance (TPP), it also has higher total heat loss (THL). Combining protection, thermal performance and toughness, Nomex Xtreme Performance is the highest performance category of solutions for flame-resistant personal protective apparel. Feedback from Firefighters “If we have a new innovation, or want to share our developments, we go proactively to fire departments to ask: Will this help you or not?” says Alfons N. Held, Global Market Leader, Emergency Response, DuPont Personal Protection. There is a difference between lab testing and what firefighters experience in the real world. Alfons N. Held adds, “We seek to understand what they need, and approach ‘lighthouse’ fire departments for guidance.” In any country or jurisdiction, there are fire departments – ‘lighthouse’ departments – that set the trends and work to evaluate the gear. If someone in Florida is using certain gear, it might also work in Texas or Arizona. The protection level Areas of continuing research in terms of firefighter garments include making them more wash-durable The question is: What protection level do we need? Given that level, departments seek to balance comfort with performance. Ironically, of the firefighters who die every year, some two-thirds of the deaths are attributable to overexertion, while less than 10% is linked to the fire/heat. Areas of continuing research in terms of firefighter garments include making them more wash-durable, more comfortable (with higher evaporation) and more lightweight. Complex systems Garments can be complex systems; heavy turnout gear is a five-layer garment with each layer contributing to performance – the outer shell, the inner liner, a moisture membrane, and one or two thermal liners. Sometimes attention is more focused on the outer layer of the gear with less awareness of the other layers and how the entire system works together. Importance of station wear In fact, protection of the firefighter starts at the skin, so station wear is important. “In our view, looking at all the layers on the skin and outwards is important,” says Alfons N. Held, adding “Firefighters wear various materials that are not always optimal.” For example, a cotton undergarment might get wet from sweat, stay wet and not evaporate. Environmental impact is another concern among garment-makers. Can the materials be reused or recycled? Some countries in Europe ask that manufacturers take back garments after they are used. New Garments, New Needs A special need is development of new garments that can perform at the wildland urban interface (WUI), where catastrophic wildland fires encroach on residential areas. Design of gear for wildland firefighting has been lighter and does not include breathing systems. When fires reach residential areas, gear needs change. Wildland firefighters are not equipped to enter a structure fire and do not have adequate protection against carcinogens. New gear designs are needed that address both environments.
Case studies
Providing innovative fire safety technology, global wireless solutions provider - Ramtech has revealed its role in protecting the prestigious F1 Hungarian Grand Prix 2024, with its WES system utilized across several temporary buildings for optimum site protection. Working closely with Hungarian partner, High-Security Kft, Ramtech supplied its EN54-25 compliant wireless fire and evacuation system (WES) for various structures including media spaces, bathrooms, dressing rooms, and conference areas. These facilities were purpose-built for the race and lacked permanent fire alarm systems, so the system helped to deliver enhanced safety for personnel and equipment throughout the event. WES fire points and smoke detectors Adam Kovics, Export Sales Manager at Ramtech, said: "It’s a privilege to get to work on such a renowned event as the F1 Grand Prix, which gives us the opportunity to showcase how robust and reliable our systems are on the world stage. WES provided an ideal fire safety solution for the temporary structures, offering ease of installation and removal post-event and ensuring safety and compliance with event regulations." He adds, "It is certainly a proud moment for the team in supporting the safety and 24/7 monitoring of this iconic race. WES fire points and smoke detectors were installed across four container groups at the Hungaroring racetrack in Mogyoród, Pest County. The WES interface was used to connect the system to the permanent fire alarm system, ensuring continuous monitoring and immediate response capabilities." Building reconstructions In the event of an evacuation, an alarm would sound to alert all workers The system’s robust radio mesh network also ensured seamless communication between devices without interfering with existing systems. In the event of an evacuation, an alarm would sound to alert all workers, prioritizing their well-being as well as helping to prevent potential disasters. Hungarian Grand Prix The famed Hungarian Grand Prix was held across the weekend of 19–21 July with 20 initial drivers competing in the 70-lap race. The event was the thirteenth round of the 2024 Formula One World Championship and the 39th running in the Hungaroring circuit’s history as part of the Formula One World Championship. The containers and the temporary system were necessary due to ongoing permanent building reconstructions that will only be completed for the 2025 Formula 1 Hungarian Grand Prix.
Cygnus’ world-first 100% wireless and EN 54 certified SmartNet-Pro fire detection and alarm solution has been installed at the Contractor’s Village at Heysham Power Station 1 in Lancashire, providing reliable life-saving fire protection equipment in a challenging industrial location. Manchester-based installer - Marlowe Fire & Security worked together with its client, Equans, a provider of technical services, FM, regeneration and energy services, on the project. Marlowe Fire & Security selected Cygnus’ SmartNet-Pro solution having successfully worked with the Cygnus team on several projects previously. Challenging Setting Contractor’s Village consists of twenty cabins, each equipped with a Detector and Manual Call Point The Contractor’s Village consists of twenty cabins, each equipped with a Detector and Manual Call Point, connected to a SmartNet-Pro Control Panel in one of the nearest cabins to the main site, alongside an interface for the signal to the main site. Simon Hilton, Systems Account Manager, Marlowe Fire & Security, said "We chose SmartNet-Pro thanks to its proven reliability, robustness, and impressive installation speed. This project presented quite a challenge due to the amount of metal in the cabin construction, which would cause issues if installing a wired system, and means we needed a product with robust signal strength." He adds, "Thanks to SmartNet’s 100% wireless capabilities, it ensured minimal disruption to the site and was quickly deployable. We’ve used Cygnus products before in similar settings and we’ve always been impressed with the outcome and this project was no exception." SmartNet fire detection and alarm system Heysham Power Station 1 experiences intermittent outages for maintenance purposes. SmartNet runs on wireless radio devices as part of a robust, self-forming and self-healing mesh network technology, in which the infrastructure nodes connect dynamically to provide highly efficient and robust network performance. This ensures that the SmartNet fire detection and alarm system can keep operating through these outages for the continuous on-site safety of workers. Being 100% wireless, SmartNet not only reduces cabling complexities that would arise trying to install through metal, but also provides a scalable solution for future needs. Successful Results Simon Hilton commended the fast responsiveness of the Cygnus team, stating, "The support from the Cygnus team was exceptional. They were always on hand to assist us, ensuring a smooth and successful installation." Simon also highlighted the value of the Cygnus Academy one-day training session and becoming a Cygnus Certified Installer, commenting "The team found this hugely beneficial as it combined both theoretical and hands-on practical training to enable them to complete a successful installation." The Cygnus Academy The Cygnus Academy presents a high-specification, in-person training program, that can be carried out in two bespoke locations. Installers gain understanding and attain certification for installing SmartNet. Geoff Copsey, EDF Energy, expressed satisfaction with the installation, stating, "The implementation of Cygnus’ SmartNet-Pro system at Heysham Power Station 1 has provided us with a reliable and robust fire detection solution. We are impressed with the system’s performance and appreciate the peace of mind it brings to our operations."
ZIEGLER is delighted to announce the successful handover and commissioning of two new Aircraft Rescue and Firefighting vehicles (ARFF) to the airport of Saarbrücken. The two identical Advancer ARFFs are setting a new standard in their class and mark a significant advance over the airport's older models. Equipped with advanced technology, including thermal imaging cameras, these vehicles offer unrivalled performance in terms of firefighting and rescue operations. New ZIEGLER Aircraft Rescue and Firefighting (ARFF) vehicles Another major advantage of the new vehicles is their improved maneuverability Their versatility is what particularly characterizes the vehicles. They are not only suitable for use on the airport premises, but thanks to their road license they can also be used outside the airport. This means that they can react quickly and effectively wherever they are needed. Another major advantage of the new vehicles is their improved maneuverability and reduced weight. New ZIEGLER ARFF offer more maneuverability and flexibility Weighing around eight tons less, the new ZIEGLER ARFF are significantly more maneuverable and flexible than their predecessors, still having enormous extinguishing agent reserves. This helps to shorten the response time in emergency situations and increase the efficiency of the emergency services. The procurement of the new firefighting vehicles was a necessary measure to replace the previous models, which had been in service for two decades.
When an employee working alone suffered a health incident, Marmon/Keystone’s investment in connected safety tech proved invaluable. The Challenge Providing safety and security for lone workers Marmon/Keystone is a wholesale distributor of tubular products with over 27 warehouses across the US, Canada and Mexico. Operating for over a century, many things have changed, yet one constant remains - the belief their employees are their most valuable asset. The company’s commitment to employee safety through their investment in extensive training and technology is one of the many reasons it has an average employee tenure of over 15 years. Robust and responsive solution These workers often work alone for extended periods and can be exposed to potential hazards As part of their comprehensive safety program, Marmon/Keystone was seeking a personal monitoring solution to ensure the safety and security of their warehouse workers. These workers often work alone for extended periods and can be exposed to potential hazards. The company needed a robust and responsive solution to provide employees with an additional layer of protection in case of an emergency. “If we didn’t have the Blackline device and the AED, I don’t think (our employee) would be alive today. This goes to show the importance of having both lone worker devices and AEDs in place,” said Amy Cottrell | Human Resources Manager, Marmon/Keystone. Emergency response management Marmon/Keystone evaluated several personal monitoring solutions before selecting Blackline Safety to equip their lone workers with G7 wearable devices. G7 checked all their boxes including no-motion and fall detection, two-way voice communication, SOS alerts, and 24/7 monitoring by Blackline’s in-house Safety Operations Center (SOC). Agents are professionally trained in emergency response management and can send help to a location quickly. The integrated cellular and cloud connectivity of the G7s to link their workers to a live monitoring center sealed the deal and gave them and their workers assurance their safety was always priority one. Automated fall alert Blackline’s SOC received a fall detected and SOS alert from the worker’s device Results - G7c proved to be invaluable for Marmon/Keystone when one of their workers suffered a cardiac arrest while working alone in a saw house. The health incident caused him to fall and strike his head, triggering G7c’s automated fall alert. Blackline’s SOC received a fall detected and SOS alert from the worker’s device. Seconds later, the organization’s Operations Manager received a text message informing her of the potential incident. While the manager quickly headed to the worker’s location, Blackline’s SOC agent called the worker’s G7c personal monitor with built-in speakerphone but did not receive a response. Automated external defibrillator The Operations Manager arrived at the worker’s location and found him unconscious. She asked a delivery driver, who had just arrived, to fetch the automated external defibrillator (AED). Moments later, Blackline’s SOC agent placed a second call to the Manager’s mobile phone who answered, frantically requesting emergency assistance before the call disconnected. The Manager began performing CPR on the injured worker using the AED while Blackline’s SOC agent immediately dispatched local police and emergency services to the worker’s location. In short order, Blackline received an update that emergency services had arrived and were providing treatment to the unconscious worker. Soon thereafter, he was taken to hospital, later released and has since fully recovered.
The fire department of a southern U.S. city was trialing Blackline Safety technology when a dangerous fuel spill put the products to the test. The Challenge Routine fuel delivery turns dangerous While making a routine fuel delivery to a local gas station one morning, the driver of a tanker truck went inside to buy a coffee. When he returned to the truck, 32 gallons (120 liters) of gasoline had spilled out, and more was flowing rapidly onto the ground. Acting quickly, he shut off the tanks and called 911. The time was 8:15 am. Minutes later, firefighters – equipped with the G7 personal gas detectors the department was trialing – were on the scene. High gas notification From G7c personal gas detector By 8:19 am, the fire department lieutenant received the first high gas notification By 8:19 am, the fire department lieutenant received the first high gas notification from a G7c personal gas detector he had been testing. Initially, it seemed like a standard alert. But by 8:21 am, the lieutenant had received eight more similar notifications from multiple devices. It was clear the situation was hazardous – and had potential to get a lot worse. “Being able to hear the radio transmissions and see the location of the responders on the map, we were able to quickly direct and adjust the response remotely. And with the real-time data – we could follow how the incident was progressing. The safety devices proved their worth to us right then and there.” said Fire Department Lieutenant | Major US City. The Solution Firefighters empowered to assess and adjust on the fly As high gas alarm notifications poured in from the firefighters’ G7s to the lieutenant’s cell phone, he knew it was a high priority incident that needed his attention. Once he logged into the Blackline Live online dashboard, he could see the location of all of the firefighters devices on the satellite map and the gas levels they were experiencing, updating in real-time, even though he was over 5 miles away. Viewing the satellite imagery on the map The lieutenant knew the roadway in question was sloped and in which direction Viewing the satellite imagery on the map, in combination with his knowledge of the area, the lieutenant knew the roadway in question was sloped and in which direction. He quickly realized the fuel would soon be flowing into a busy roadway and down into the sewers. He instructed firefighters on the ground to investigate possible downhill movement of the spill. Moments later, he could see new high gas alerts appear on the map as firefighters moved multiple blocks down the roadway from the initial spill. Their G7 devices were detecting high concentrations of gas moving down the slope, just as he had suspected. The firefighters moved quickly to contain the situation, and by 9:57am the incident was resolved. The Results Saving lives in the moment – and over time Aided by real-time data from Blackline Safety, the Lieutenant was able to leverage his years of experience to diffuse a volatile scenario quickly and safely. Despite being remote, he could assess the situation, direct his people, and receive instant data and readings from their monitors to validate and adjust his strategy. G7 devices detected 38 instances of high gas exposures In total, the G7 devices detected 38 instances of high gas and 98 low level exposures In total, the G7 devices detected 38 instances of high gas and 98 low level exposures. Not only did this keep firefighters safe on the scene, but the data also quantified the amount of exposure each person had during the entire incident. This transparency means supervisors have the information they need to assess health risks to their personnel, and ensure they get medical attention when necessary – protecting people in the moment and over time. At a glance As firefighters arrive on scene, their G7s send high gas alerts to the fire department lieutenant, over five miles away. The lieutenant can see real-time location of personnel, plus gas type and exposure levels via Blackline portal. G7 data and the lieutenant’s knowledge of the area allows for fast, safe containment of fuel on roadway.
Comelit-PAC has been working with partners - GB Integrated Systems to fit the latest fire safety systems at the Hop House in Deva City Office Park, in order to ensure the safety of all who work and visit the unique work environment. Part of the former Threlfalls Brewery, an iconic feature of the Manchester city skyline, Deva City Office Park presents an eclectic mix of business space presented in a Grade II listed Brewery building or 17 high-spec self-contained office units. Balancing modern design GB Integrated System worked directly with the site management team to upgrade the addressable panels With the need to offer 24 / 7 security and fire safety, GB Integrated System worked directly with the site management team to upgrade the addressable panels, and specified Comelit-PAC’s latest LogiFire solution. Iain Taylor, Director of Asset Management at Northwood Investors International Limited, said: “We knew we had complex requirements for Deva City when it came to security and fire safety, with each individual business on site needing its own risk assessments. This was set against the buildings themselves, where any upgrades had to be sympathetic to the specific interest Grade II classification and balance modern design and use of technology.” Easy fire safety solution Iain Taylor adds, “GB Integrated Systems made it a priority to understand this and work with us right from initial design and specification to implement a bespoke solution that could accommodate our requirements. From a fire safety perspective, Comelit-PAC was recommended, to ensure we could reduce installation time and minimize disruption to business activity for the benefit of our occupiers.” GB Integrated System specified Comelit-PAC’s LogiFire Easy fire safety solution. The office park required a stand-alone 1-loop analog addressable panel. Fire safety solution We recommended Comelit-PAC’s Logifire solution essentially because of its simple design" Mike Gray, Technical Director at GB Integrated Systems, stated: “We recommended Comelit-PAC’s Logifire solution essentially because of its simple design, and ability to easily install using existing cabling, so as not to interfere with the style of the development and its unique character. From the owner’s perspective, its style and flexibility of use means that it is the best fire safety solution to protect the occupiers collectively and blend seamlessly with its surroundings.” Logifire addressable system, has been designed to offer a simple to install, fire safety solution that is compliant with BS and EN standards. It is complemented with a range of detectors, offered with award-winning designs to ensure systems blend with their surroundings. Mind fire safety Mandy Bowden, Comelit-PAC Fire Manager, concluded: “When it comes to fire safety, the market is growing rapidly amid greater awareness of the need for risk assessments, remediation work, building upgrades and ongoing maintenance in the new-build sector as well as at existing sites. What our work with GB Integrated Systems at Deva City Office Park demonstrates is the need to assess each development as early as possible in a works program to ensure solutions meet exact requirements." She adds, "We understood that any upgrade had to be carefully considered with regards to how it will impact on the aesthetics of the overall premises. Together, we identified how LogiFire as a single solution, could be installed quickly and effectively for the benefit of all who work on-site. It allows for total peace of mind fire safety.”


Round table discussion
Thermal imaging is an advantageous tool for firefighters on the frontline. As thermal cameras have become more compact and affordable, their availability has expanded, along with their usefulness. We asked our Expert Panel Roundtable: How does thermal imaging serve the needs of firefighters and how is it changing?
New tools and technologies are emerging that augment the efforts of the fire market to prevent and fight fires. Modern firefighting is benefiting from an ongoing sea change in technological capabilities, spanning equipment, electronic components, greater connectivity and firefighter monitoring, to name just a few. We asked our Expert Panel Roundtable: What technologies will have the greatest impact on the fire industry in 2021?
Products


Videos
Explosion Protection: Manufacturers & Suppliers
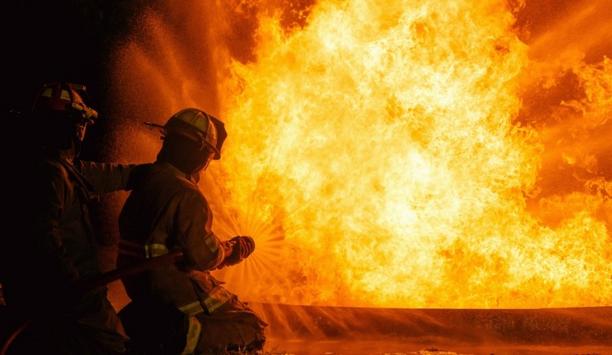
The New Future For Fire Agencies
Download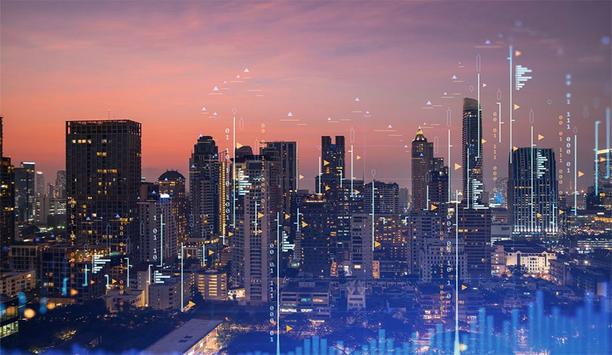
The Eight Key Trends in Fire Detection in 2023
Download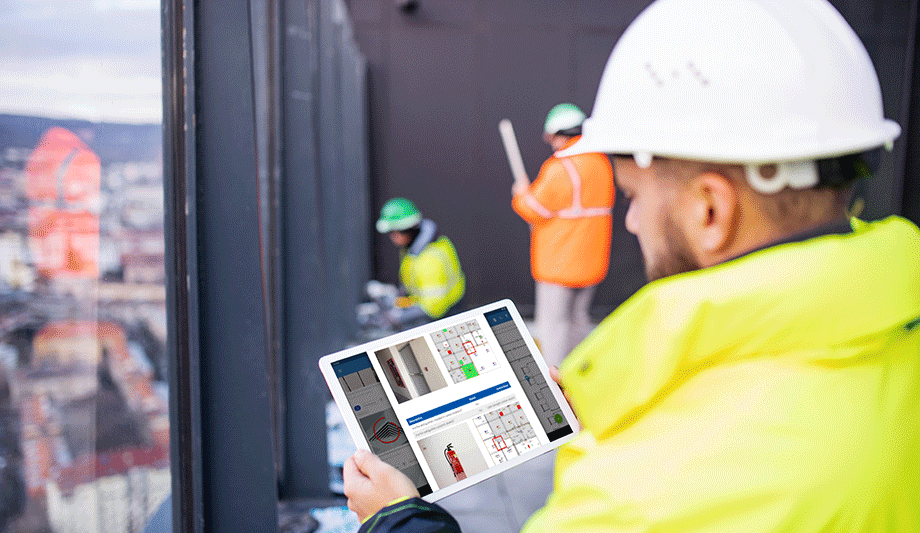
A Digital Platform to Improve Fire Safety Compliance and Inspections
Download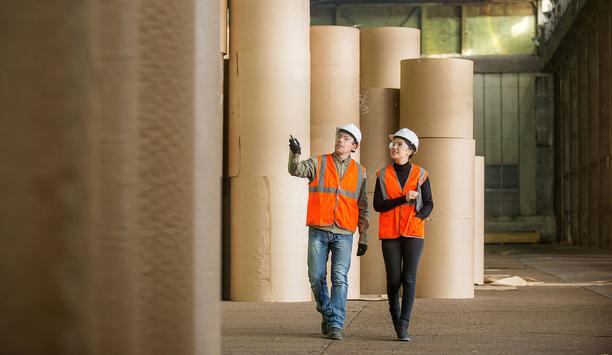
Overcoming the Challenges of Fire Safety in the Paper Industry
Download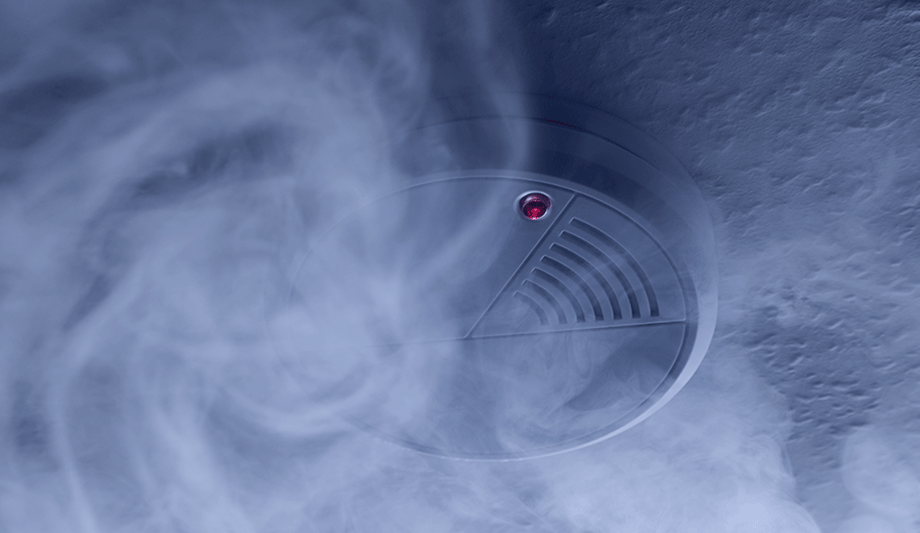
Carbon Monoxide: Creeping Killer Caught In The Act
Download